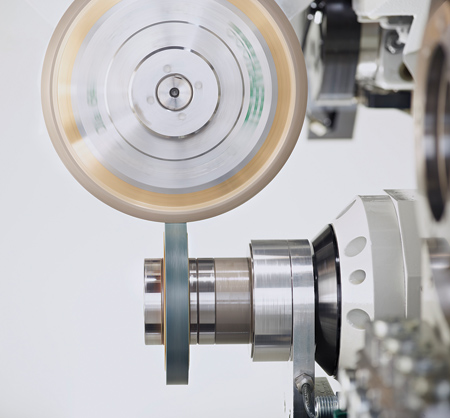
XING-dressing a tapered diamond grinding wheel, which is positioned at a 90° angle to the dresser wheel.
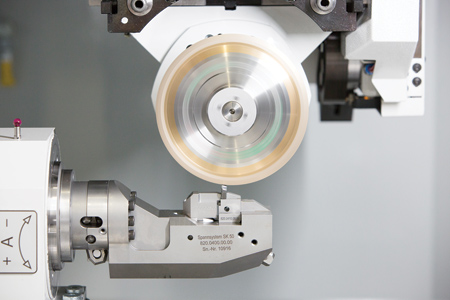
Machining a profile insert on a Multigrind CU grinding machine.
"HAAS Schleifmaschinen GmbH has many customers who manufacture profile inserts, all of whom value maximum dimensional accuracy and surface quality," said a HAAS Multigrind spokesperson. The Multigrind CU and Multigrind CA are the grinding machines most frequently used. The grinding tool of choice when it comes to machining profile inserts is often the tapered or V-shaped diamond grinding wheel, which has to be dressed - i.e. brought into the correct geometric form - on a regular basis to ensure enhanced grinding results.
Dressing with Profile Accuracy
"The extremely precise tapered diamond grinding wheels often feature an edge radius of just a few hundredths of a millimeter and are correspondingly sensitive, which is why HAAS opts for the XING dressing technique," said a company spokesperson. The dresser wheel axis is not positioned parallel to the grinding wheel axis, as it is with other techniques, but rather at a 90° angle, meaning the silicon carbide or corundum wheel often associated with other diamond grinding wheels can be used for dressing. Due to the NC-controlled process, the radius of the grinding wheel can be generated with the circumference of the dresser wheel, thus maintaining a consistent contact surface and pressure between dresser wheel and grinding wheel. The benefits of XING dressing include a lower pressure load and higher profile accuracy for the grinding wheel.
Dressing Without Unclamping and Re-Chucking
Like all other dressing techniques at HAAS, XING dressing is also carried out inside the grinding machine, eliminating the need to unclamp and re-chuck the grinding wheel. That has a positive effect on dimensional accuracy, while the grinding wheel features better radial and axial runout, making it possible to generate better surfaces. "This is something that can actually be heard while grinding - the wheel sounds much 'healthier' during the grinding process," said the spokesperson.
"Due to the positive experiences we have had with XING dressing, this technique will be expanded for use in additional applications at HAAS," continued the spokesperson. In current projects we are applying the technique to profile grinding wheels, grinding pencils or quills and grinding wheels with other grain types, as well as ceramic and hybrid-bonded grinding wheels. As a result, many different wheel contours can be dressed using the Multigrind grinding machines. But this is only possible if the option for direct or indirect wheel probing is available. A noise sensing system is always required for setting up, optimizing and operating the dressing process. When it comes to V-shaped wheels with a 30° included angle, the wear is highly dependent on previous wheel damage, meaning the existing wear behavior needs to be measured and compensated for.
For more information contact:
HAAS Multigrind LLC
137 Enterprise Drive
Warsaw, IN 46580
574-268-0053
info@multigrind.com
www.multigrind.com