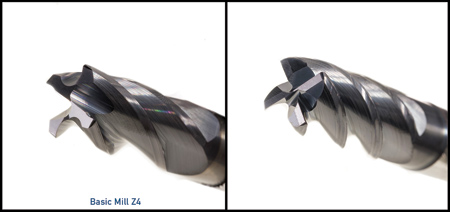
(l-r) Basic Mill Z4 variable helix vs. standard variable helix end mill
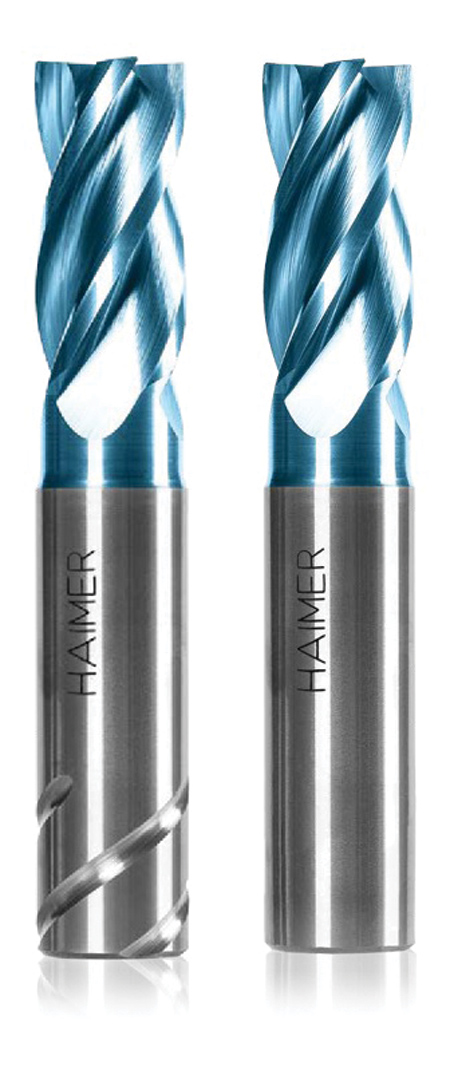
The Basic Mill Z4 for milling and drilling.
"Resourceful machine shop owners are quick to incorporate anything that increases production and reduces cost while maintaining the ability to turn out high quality parts," said a HAIMER spokesperson. "Versatility is often a key factor in the planning process. That is the reason the Basic Mill Z4 solid carbide end mill is popular. It not only provides superior milling capabilities, but is also specially designed to perform a wide range of applications normally done with a drill."
High Performance Milling
HAIMER's Basic Mill Z4 is a high performance variable helix end mill. This tool is designed to reduce harmonic resonance, thereby decreasing vibration and enabling higher speeds with increased depths of cut. HAIMER's German engineers found varying the helix from front to back within the same flute achieves the most efficient reduction in vibration and harmonics, making the Basic Mill Z4 (31° - 33° helix) suitable for roughing and finishing general steels, cast iron, alloy steels and stainless steels. "The HAIMER Basic Mill Z4 can easily slot up to 1.5X diameter without any reduction in feedrate," the spokesperson added.
HAIMER gave the Basic Mill Z4 a unique end gashing and flute design. The end geometry more closely resembles a drill than it does an end mill, adding the capability to do steep ramping and plunging (drilling) operations.
"A common misconception when it comes to milling is that any tool can be used as a drill," said a Haimer spokesperson. "The old school rule of thumb is that center cutting end mills can plunge if needed. It is generally not recommended, though, for a number of reasons - one being that the gashing and flute geometries of end mills are not designed for axial milling (drilling). The result of such operations with standard end mill geometry is poor tool life, slow speeds, poor finishes and frequent breakage. The Basic Mill Z4 from HAIMER changes this."
"One customer that was using a standard end mill for counterboring was turning out 8 parts (48 holes) before the tool was completely worn," said the spokesperson. "Equally noteworthy was this customer's satisfaction with this performance, as they had tested several brands and designs before they settled on the most cost-effective option. Upon testing the Basic Mill Z4, they were able to machine 860 parts (5,160 holes); more than 100X tool life at 3X the feedrate. This customer, like so many others, was simply not aware that while they had center-cutting end mills, none were truly designed to perform drilling operations."
While most drilling operations are best done with a drill, there are still a great deal of applications that can be optimized with a tool such as the Basic Mill Z4. Counterbores and pilot holes are two examples. Eliminating a drill in place of this 2-in-1 tool also represents cost-savings in terms of tool consumption (eliminate a drill) and tool change times. Lastly, such a tool gives startup shops or those without sophisticated programing capabilities, the ability to "plunge and run" when access to more sophisticated part-entry programming methods are unavailable.
For more information contact:
HAIMER USA
134 E. Hill Street
Villa Park, IL 60181
630-833-1500
haimer@haimer-usa.com
www.haimer-usa.com