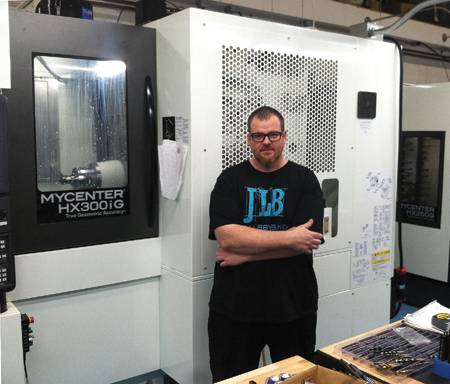
Jim Libby with JLP's newest Kitamura horizontal machining center with a 15k spindle, extremely fast tool changer and rapids of 2,362 IPM. "The DD table also rotates very fast," said Libby. "At over 20,000 lbs. the Mycenter-HX300iG 300 mm horizontal weighs more than most 400 mm horizontals. The machine weight/travel is the first thing we looked at when purchasing a machine at JLP because it has a lot to do with the longevity and accuracy of its life. Mass is the only way to dampen the vibration caused by the machining process."
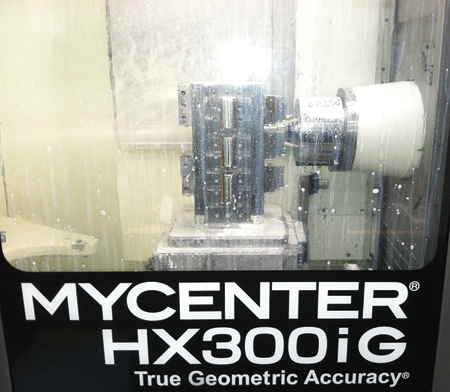
JLP employs a lot of dovetail workholding. "We manufacture our own dovetail fixtures from 17-4 PH stainless steel and then heat treat them to H900 for longevity," said Libby. "The Mycenter-HX300iG at JLP is utilizing the Renishaw NC4 laser non-contact tool detection and the OMP 400 spindle probe. After implementing these on previous machines, JLP will never buy another machine without them. The ROI is almost immediate in a job shop."
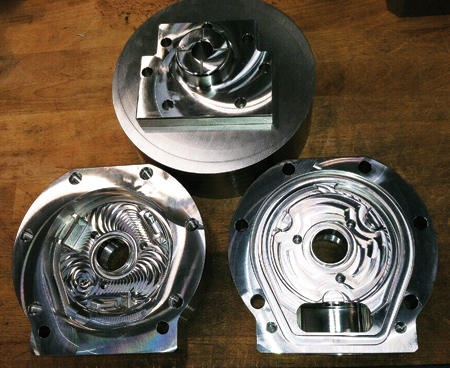
"The components for which the Mycenter-HX300iG was purchased to machine are cut from 6.5 inch diameter 316 ss," said Jim Libby. "The HX300iG handles these parts with ease. A one inch Sandvik 880 insert drill cuts the center hole 2.6 inches deep. The majority of the roughing is done with a Dura-Mill Whisperkut series 1/2 inch endmill. VoluMill or trochoidal type roughing works extremely well on the HX300iG because of its ability to move in and out of extremely high feedrates. It remains very smooth in and out of cut. The HX300iG is quite happy with the feedrates required to fully utilize VoluMill. JLP has been using this kind of roughing strategy since it became available with CAM software. It has been our belief that this kind of roughing is by far the best for productivity and getting the most out of the tooling. Having a machine that can handle the transition from low to high feedrates efficiently is critical to making VoluMill work. Kitamura has really achieved this."
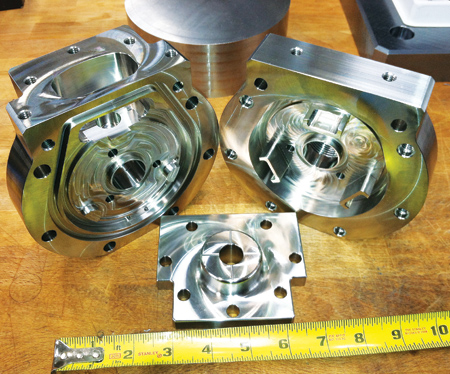
JLP Machine and Welding LLC thrives on efficiency, so when owner Jim Libby needed to add a horizontal machining center (HMC) to his growing lineup of machine tools, versatility was an important consideration.
"We needed a rigid, fast, precise HMC that could remove high rates of 316 stainless but also be a versatile job shop machine," said Libby. "We considered many different 300 and 400 mm horizontals. The tooling was already established since we were running multiple operations of the same part in vertical machines."
Libby determined that the Mycenter-HX300iG from Kitamura was the best choice for the shop. The HX300iG was purchased through Packard Machinery, a long-time Kitamura dealer that also services JLP's Kitamura machining centers.
"We already had a Kitamura HX250G and the Arumatik-Mi control was familiar," Libby said. "Glass scale precision and a 15K spindle make the Mycenter-HX300iG very versatile. One minute we are face milling or hogging stainless, and the next we are surfacing some tiny feature into a bone plate or medical part." JLP utilizes a Renishaw OMP400 spindle probe and Renishaw NC4 laser tool detection on the HX300iG.
According to Libby, the machine cut cycle time by 40% and handling by 50%. "We are also running longer cycle times because we can put more parts in the machine," he said. "The finishes are amazing and the machine has exceeded expectation. The parts simply come out better on the Kitamura."
Mycenter-HX300iG specifications:
- Table size: 12" x 12"
- Travel (XYZ): 18.1" x 20.1" x 22.0"
- Spindle taper: NST No. 40
- Spindle speed: 40~15,000 RPM (20,000 option)
- Tool storage capacity: 50 pcs. (field expandable option to 100/150/200 tools)
- Tool change time (T-T/C-C): 1.3 sec. /2.5 sec.
- Rapid feed (XYZ): 2,362 IPM
- Rapid feed (B): 54,000 deg./min. (150 RPM).
Features and benefits:
- Reduced set-up times for highly complex parts requiring multiple operations
- Small footprint saves on valuable floor space
- Positioning accuracy: ±0.000079" full stroke, repeatability: ±0.000039"
- High speed rapid feedrates of 2,362 IPM
- High speed 4th axis rotary table, direct drive motor driven 54,000 deg/min (150 RPM) rapids
- Two-station APC is automation ready and field expandable up to eight pallets for unmanned operation potential
- High power, high-speed processing Arumatik-Mi CNC with 67 million pulse encoder technology
- Ballscrew cooling and linear scale feedback in all axes.
JLP manufactures a wide variety of components, most of which are highly complex, as well as diverse CNC job shop work. Products include medical devices and fluid handling devices (valves).
A valve body and cover machined on the Mycenter-HX300iG is made from a 316 ss billet and requires 75% material removal from blank. According to Libby, "These parts are made faster and more precise than before."
JLP was founded in 1998 and has experienced growth every year. This is largely due to Libby's systematic and highly efficient approach to programming and set-up. "One man can operate 10 machines," said Libby. "This gives us more throughput, less handling and better quality parts." Pallet changers have added to the company's lights-out capabilities.
Libby's passion for manufacturing began at an early age. He became an accomplished TIG welder by the age of 18 and a CNC programmer by 22. He started the business three years after graduation with a TRAK mill, and is now looking to expand the current 4,000 sq. ft. facility. "There is no shortage of work or jobs," said Libby. "Manufacturing is booming."
JLP serves a range of industries including medical, aerospace, optics, fluid control, robotics, energy and semiconductor. "Our company goal is to continue providing the highest level of quality components to our customers," said Libby.
For more information contact:
Jim Libby
JLP Machine and Welding LLC
10 Winter Street
Kingston, MA 02364
508-922-4373
jlpmachine@yahoo.com
www.jlpmachine.com
Kitamura Machinery of USA Inc.
78 E. Century Drive
Wheeling, IL 60090
847-520-7755
info@kitamura-machinery.com
www.kitamura-machinery.com
(NE ONLY)
MA, NH, VT, RI, ME, CT
Packard Machinery Co., Inc.
504 Groton Road
P.O. Box 1618
Westford, MA 01886
978-692-3100
www.packardmachinery.com