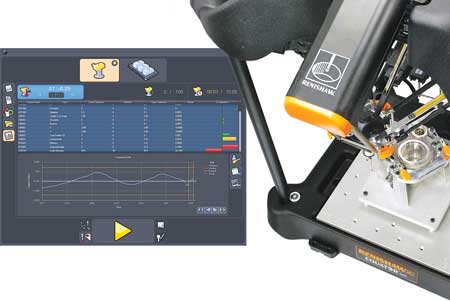
Renishaw's Equator comparative gauging system process monitoring software displays measurement results of inspected features, as well as the measurement history of each feature, instantly via a monitoring window added to the shop-floor user interface.
Renishaw's Equator comparative gauging system now includes new process monitoring software that displays measurement results of inspected features, as well as the measurement history of each feature, instantly via a monitoring window added to the shop-floor user interface.
The intuitive Organizer front-end software works with Renishaw's comprehensive MODUS program to allow operators to manage the re-mastering process based on temperature limits, number of parts or time since the last master. A status bar graph shows inspection results for the last part measured as a proportion of tolerance either side of nominal. Operators can configure the system to set extra warning limits on part features, beyond the pass/fail tolerance limits already set by the inspection program, allowing them to take action before a process reaches 100% of tolerance. The bar graph turns orange at the warning limit and if the pass/fail tolerance is exceeded, the bar turns red and re-mastering is enforced with an on-screen message to the operator.
History of Measurement
Selecting an inspected feature changes the graph to show the values measured for that feature on previous parts. The scale can be changed to show just the history of recent parts, or expanded to show more parts, allowing operators to spot any trend in the process - a feature that is especially helpful when dealing with cutting tool wear or other factor that causes the process to drift. If the value for a feature is steadily drifting towards its tolerance limit, the operator or engineer can decide to apply a tool offset or change the cutting tool used for that feature. The graph shows the tolerance and warning limits, along with vertical lines, when re-mastering points are recorded.
Managing Re-mastering
One of Equator's key strengths is that it can operate in factories with wide temperature variation due to its ability to cope with changes in shop-floor temperature by employing the traditional method of comparing production parts to a reference master part and re-zeroing the system with an inspection routine on the master part. This re-mastering is as swift as measuring a production part and immediately compensates for any change in the thermal conditions of the shop-floor environment. The process monitor now makes this even easier to manage by using a built-in sensor to detect changes in ambient temperature and warn the operator that re-mastering is needed. Engineers can set upper and lower drift limits - if the temperature chart is selected, the measured values can be seen plotted against each part inspected. Alternatively, the engineer can specify that re-mastering is required after a certain elapsed time or after a certain number of measurement cycles. The software automatically switches from measure mode into master mode, so the operator can run the mastering routine.
Historical measured data can be exported in two formats: .csv for use in spreadsheets or .jpg images for use in reports. These options are available through on-screen buttons and allow either file format to be saved on the Equator Controller or on a network location for other applications to use.
Equator Principle of Operation
Equator is capable of high-speed comparative gauging for inspection of high-volume manufactured parts. Equator is a lightweight, fast and repeatable gauge with "push-button" simplicity. It can switch between parts in seconds, making it ideal for flexible manufacturing processes or accepting parts from multiple machines.
Users take a production part and measure it on a coordinate measuring machine (CMM) to establish the variation from CAD or drawing nominals. The results from CMMs can be configured to be used directly with the Equator software. With the calibration file loaded into the software, measurements made in the Equator system can be referred back to the CAD or drawing nominals.
For more information contact:
Renishaw Inc.
5277 Trillium Blvd
Hoffman Estates, IL 60192
847-286-9953
usa@renishaw.com
www.renishaw.com