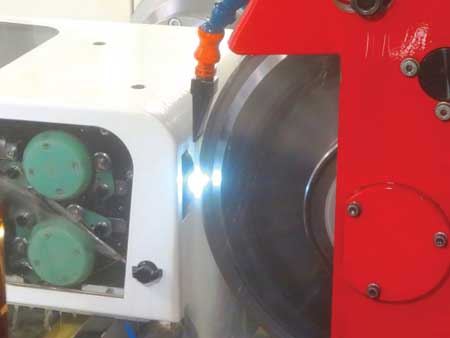
"The dressing unit is a wire erosion machine in principle," said a company spokesperson. "STUDER offers a new development for dressing metal-bonded diamond and CBN grinding wheels directly in the grinding machine."
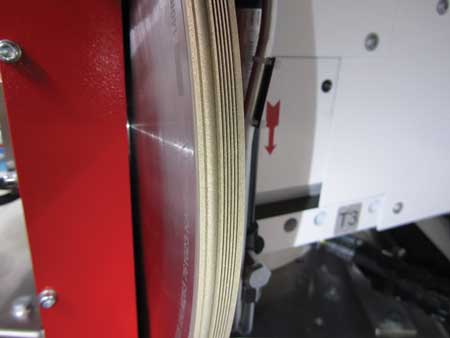
An example of an MD25 grinding wheel Ø400 mm, complex profile dressed with WireDress, is pictured.
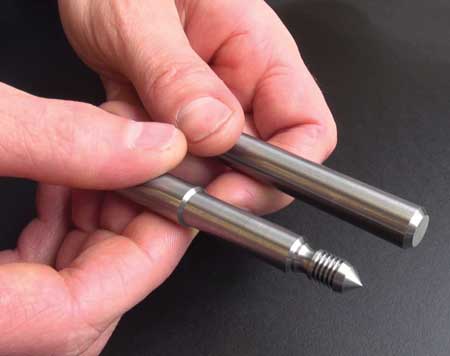
According to a company spokesperson, the WireDress technology allows free geometries and intricate contours with internal radii of 0.05 mm and external radii of 0.2 mm.
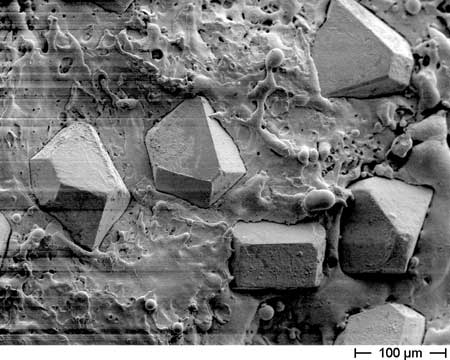
D126 grain space is shown after dressing with STUDER-WireDress.
"The integrated electro-discharge dressing technology WireDress opens up new possibilities for grinding with metal-bonded grinding wheels and drastically cuts auxiliary times," said a Fritz Studer AG spokesperson. "It has been possible to increase grinding power in the grinding process by 30% and reduce grinding wheel wear by 70% in comparison with ceramic and resin bonds. Grinding wheels with very intricate contours can also be dressed."
According to the spokesperson, metal-bonded grinding wheels offer particular benefits when machining difficult-to-machine materials such as high-alloy, hardened steels, tungsten carbides and ceramics. Such wheels offer superior dimensional and thermal stability and dissipate the heat produced by grinding more quickly. The grinding wheels consist of a sintered metal matrix with embedded diamond or cubic crystalline boron nitride (CBN) grains. They achieve high removal rates because the metal bond holds the abrasive grains well.
Electro-Discharge Dressing
"However, in addition to the advantages of metal bonds there are also disadvantages, as dressing these wheels involves greater expense and effort," said the spokesperson. "Dressing with silicon carbide wheels, for example, often does not achieve satisfactory results, and intricate profiles are not possible. In addition, the grains are difficult to mechanically extract from the metal matrix and are sometimes damaged in the process. It is also not possible to create the high grain protrusion heights necessary to achieve the full efficiency of such grinding wheels. The hard abrasive grains of metal-bonded grinding wheels also lead to heavy wear of the dressing wheels, which results in certain limitations in terms of geometrical precision.
"Experts see alternatives in electrochemical (ECM) and electro-discharge (EDM) dressing processes. Both create grains with high protrusion heights and operate without contact. However, electrical discharge dressing processes do not require any chemically active liquid to remove the metal bond.
"Electrical discharge dressing processes use the basic principle of electrical discharge machines (EDM). As with these machines, the material is removed without contact by very short direct current pulses following each other in quick succession, which generate a discharge in the gap between electrode and workpiece in the dielectric. During the discharge tiny areas of the metal bond of the grinding wheel are melted and flushed out of the gap as small particles by the dielectric medium.
"External dressing machines are sometimes used for dressing metal-bonded grinding wheels. The grinding wheels have to be removed from the grinding machine, transported to the dressing machine and, after return transport, mounted on the grinding machine and set up again. It is very difficult to achieve micron precision using this method. Moreover, the handling and logistics effort involved, with its time and cost disadvantages, makes machine-integrated dressing systems appear very advantageous."
Integrated Dressing with Wire Erosion
With STUDER-WireDress Fritz Studer AG brings a new dressing device to the market. This product is designed to use the wire erosion principle and is completely integrated into the grinding machine and its control system. "The grinding wheel never has to be removed for dressing," said the spokesperson. "Due to the high proportion of grain space, the wheel is very free cutting. This allows much more grinding oil to enter the grinding slot, enabling a high feed with less workpiece deflection. The dressing intervals can be longer. However, as the dressing process requires so little expense and effort, very complex contours can also be dressed at shorter intervals.
"The dressing device is a small wire erosion machine in principle. The electrode is a wire, which is drawn with a small gap tangentially past the machining point at a constant speed of 100 mm/s. The opposite pole is the grinding wheel, which moves at peripheral speeds of 50 to 140 m/s during dressing. It does not need any dielectric, as the grinding oil used during grinding fulfills this function. The dressing wire is guided in a groove on the circumference of a thin, circular ceramic disc. The ceramic disc has a notch at the point where the sparks jump between the wire and the grinding wheel.
"Feeds of 15 to 25 mm/min can be achieved when dressing a typical metal bond. In this way largely free geometries and intricate contours with internal radii of 0.2 mm and external radii of 0.05 mm are generated on the grinding wheel. Removal rates of up to 80 mm3/min are achieved. The grain retains its original shape during this contactless dressing process."
No Wear on the Dressing Tool
As the wire is continuously advanced during the dressing process, an electrode with precise geometry is always located at the dressing position, according to the spokesperson.
"The wire reel in the dressing unit contains 10 km of wire; this supply would allow dressing to be continued for approximately 16 hours without interruption," said the spokesperson. "The used wire is cut into short pieces immediately after the dressing process and collected in a container. The ceramic guide disc across which the electrode wire runs only wears after several thousand hours. The circumference of the disc has three of the above mentioned notches; if necessary it is simply turned further around by one of the three segments, and an intact wire guide is available again."
Control Unit
The STUDER-WireDress control unit is integrated into the control system of the grinding machine. "It has all necessary dressing functionalities and also contains a software program for intelligent profiling with path optimization (StuderDress integrated)," said the spokesperson. "The grinder does not need any special training for operating the dressing device, as he or she is guided by the clear and transparent guidelines on the screen of the control unit.
"The new development also brings significant energy savings as part of the Blue Competence measures at STUDER: it only needs around 500 watts during dressing and 25 watts during the standby phases. For comparison: Rotary dressing with diamond wheels uses 1.5 kW; the energy required for the provision of sealing air, which is constantly necessary, is 1 kW."
The development of the WireDress technology from basic research through testing to industrial product in seven years was also carried out on the S22, according to the spokesperson. This is a production platform designed for the mass production of medium-sized workpieces. It enables machining operations such as cylindrical grinding, form and thread grinding, heavy-duty applications with 160 mm wide grinding wheels or high-speed grinding (HSG) with cutting speeds up to 140 m/s. STUDER-WireDress is also available on the S31 and S41 CNC universal cylindrical grinding machines.
For more information contact:
UNITED GRINDING North America, Inc.
510 Earl Blvd.
Miamisburg, OH 45342
937-859-1975
info@grinding.com
www.grinding.com
Southwest
E. TX
Charles Harter
CJ Harter & Son Machinery Inc.
550 Westcott, Suite 375
Houston, TX 77007
713-227-7221
harterhou@sbcglobal.nex
AR, LA
Steve Wherry
Cardinal Machinery
7535 Appling Center Dr.
Memphis, TN 38133
901-377-3107
s.wherry@cardinalmachinery.com
www.cardinalmachinery.com
NM
Mike Geoffroy
The Geoffroy Company, Inc.
5910 S. University Blvd, C-18 #211
Greenwood Village, CO 80121
303-756-3684
TGCIdenver@comcast.net
Southeast
AL, MS, TN, FL (Panhandle)
Steve Wherry
Cardinal Machinery
7535 Appling Center Dr.
Memphis, TN 38133
901-377-3107
s.wherry@cardinalmachinery.com
www.cardinalmachinery.com
VA, NC, SC, GA
David Chesnutt
Methods Machine Tools, Inc.
13607 South Point Boulevard
Charlotte, NC 28273
704-587-0507
dchesnutt@methodsmachine.com
www.methodsmachine.com
Northeast
NY (All Except NYC & Long Island)
Gordon Britton
Britton Machinery Sales, Inc.
330 Castlebar Rd.
Rochester, NY 14610
585-721-4160
gbritton@brittonmachinery.com
W. PA
Mark Henne
Marcus Machinery
106 Bellefield Court
Gibsonia, PA 15044
412-862-0803
mark.henne@marcusmachinery.com
www.marcusmachinery.com
WV
Art Seyler
Ellison Technologies
5333 Muhlhauser Rd.
Hamilton, OH 45011
513-874-2736
aseyler@ellisontechnologies.com
www.ellisontechnologies.com
DE, MD, NJ, E. PA, NY (NYC & Long Island)
Chris Cowan
Tuckahoe Trading
94 N. Hamilton St.
Doylestown, PA 18901
215-345-9275
chris@tuckahoetrading.com
www.tuckahoetrading.com
Midwest
MN, ND, SD, N. IA, W. WI
Dan Hales
Hales Machine Tool Inc.
2730 Niagara Lane North
Plymouth, MN 55447
763-553-1711
dhales@halesmachinetool.com
www.halesmachinetool.com
NE, S. IA
Ken Erickson
Erickson Machine Tools
409 Market Ave.
Story City, IA 50248
515-733-4361
ken@ericksonmachine.com
www.ericksonmachine.com
E. WI
Bob Stoltz
Merwin Stoltz Company
N52 W13325 Falls Creek Court
Menomonee Falls, WI 53051
800-923-6255
bstoltz@dgisupply.com
www.merwin-stoltz.com
MO
David Smith
CJ Smith Machinery Company
2275 Cassens Dr., Suite 123
Fenton, MO 63026
636-349-7757
dsmith@cjsmith-machinery.com
www.cjsmith-machinery.com
MO, KS, S. IL
Bill Enright
Dynamic Machine Tools LTD
84 Hubble Drive, Suite 200
O'Fallon, MO 63368
636-329-9734
benright@dynamicmachinetool.com
www.dynamicmachinetool.com
IN, N. IL
Chris Tauber
Integrated Machinery Systems
101 North Prospect Ave.
Itasca, IL 60143
630-250-8305
chris.tauber@imscnc.com
www.imscnc.com
KY
John Stephenson
Tri-S
3 North Shaw Lane
Fort Thomas, KY 41075
859-380-5909
trisjohn@fuse.com
KY, OH
Art Seyler
Ellison Technologies
5333 Muhlhauser Rd.
Hamilton, OH 45011
513-874-2736
aseyler@ellisontechnologies.com
www.ellisontechnologies.com
MI
Brad Contrucci
Tooling Systems Sales
1782 Apple Ridge Court
Rochester Hills, MI 48306
248-656-2035
bradc@tssgrinding.com
www.toolingsystemssales.com
West
AZ
Richard Adams
Adams Machinery
215 S. Rockford Dr., Suite 101
Tempe, AZ 85281
480-968-3711
dick@adamsmachineryaz.com
www.adamsmachineryaz.com
S. CA
Jay Davis
DMARK Corporation
10552 Humbolt St.
Los Alamitos, CA 90720
562-799-9010
jdavis@dmarkcorp.com
www.dmarkcorp.com
NV, N. CA
John Franchuk
Die Mold Machinery
300F Danville Boulevard #323
Alamo, CA 94507
925-831-0920
john@diemoldmachinery.com
www.diemoldmachinery.com
CO, E. WY
Mike Geoffroy
The Geoffroy Company, Inc.
5910 S. University Blvd, C-18 #211
Greenwood Village, CO 80121
303-756-3684
TGCIdenver@comcast.net
MT, UT, S. ID, W. WY
James Grisley
JM Grisley Machine Tools, Inc.
1485 South 300 West St.
Salt Lake City, UT 84115
801-486-7519
sales@jmgrisley.com
www.jmgrisley.com
OR, WA, N. ID
Gary Anderegg
Machine Toolworks, Inc.
14600 Interurban Avenue South
Tukwila, WA 98168
206-575-3390
ganderegg@machinetoolworks.com
www.machinetoolworks.com