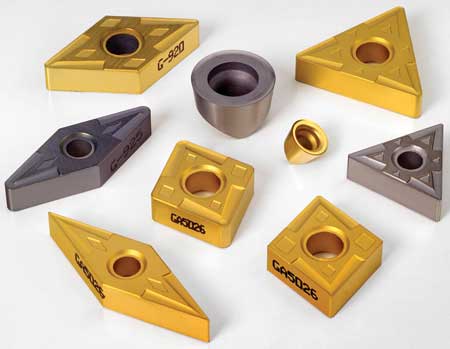
Greenleaf's TurboForm inserts utilize a chipform that addresses the machining of new thin wall engine designs by reducing cutting forces.
Greenleaf Corporation offers a variety of indexable cutting tools designed to meet the demanding machining applications specific to aerospace.
WG-300, WG-600 and WG-700
Greenleaf's WG-300, WG-600 and WG-700 whisker-reinforced ceramic inserts are engineered for machining high-strength alloy materials and for use in complex turbine machining operations. "Combining a high degree of heat, wear and impact resistance, these grades provide maximum predictable metal removal rates in high-strength alloy machining applications," said a company spokesperson.
According to the company, WG-300 is designed to bring high productivity increase to the most critical component of the aerospace industry: the jet engine. "It offers machining at eight times the production rate of traditional carbide cutting tools," said the spokesperson.
WG-600 is a commercially available, coated, whisker-reinforced ceramic for use in production. "This is a very predictable insert grade that expands the speed envelope of WG-300 at the same feedrates, providing a new productivity range to the application," said the spokesperson. "It is particularly well suited to applications in which extended tool life is critical."
WG-700 was introduced to meet the needs of new developments in hot section materials for jet engines. The new base material of the WG-700, combined with a nano-layered platinum coating, is designed to productively machine the newest breed of materials, such as Inco 718+ and other super alloys.
XSYTIN-1
XSYTIN-1 is engineered specifically for the machining of difficult-to-cut materials at aggressive feedrates. "As the engines get lighter and lighter for fuel savings, there are sections that become very thin," said the spokesperson. "A wall section of 0.050 inch (1.27 mm) in thickness is not an application for a ceramic cutting tool. Carbide must be used as the cutting tool and controlling the chip becomes the paramount issue.
"The structure of XSYTIN-1 exhibits high wear resistance and outstanding thermal shock resistance, which makes this grade a predictable, high-strength, high-performance product that is capable of a wide range of speeds and higher feedrates than competitive ceramic grades."
TurboForm
The Greenleaf precision ground TurboForm insert utilizes a chipform that addresses the machining of the thin walls of new engine designs by reducing the cutting forces involved. Material chips are controlled at a range of depths of cut down to 0.005" (0.127 mm). This design features a high, positive-rake cutting edge in a negative-style insert for maximum economy at high-performance levels, according to the company. The TurboForm insert design - as well as other standard Greenleaf carbide grades such as G-925, G-920 and GA5026 - are all designed for the high-speed machining of high-strength alloys, titanium, high cobalt and stainless steel applications.
For more information contact:
Sales
Greenleaf Corporation
P.O. Box 1040
18695 Greenleaf Drive
Saegertown, PA 16433
800-458-1850 / 814-763-2915
sales@greenleafcorporation.com
www.greenleafglobalsupport.com