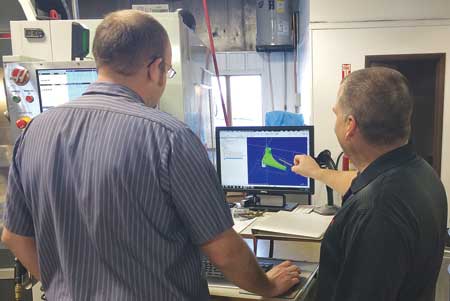
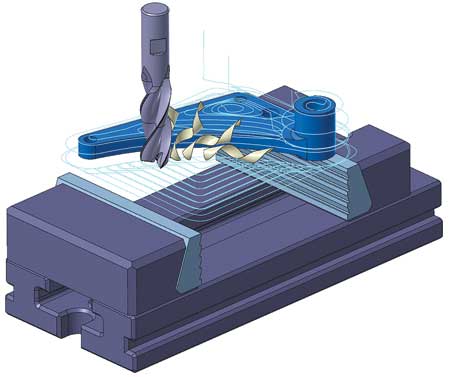
Dynamic Machining Technology in Loudon's Mastercam X7 CAM software (from CNC Software, Tolland, CT) tightly controls tool engagement, making it possible to remove material much faster than conventional motions. Because the tool is never overloaded, tool life is increased and the user can accurately predict when to replace the tool.
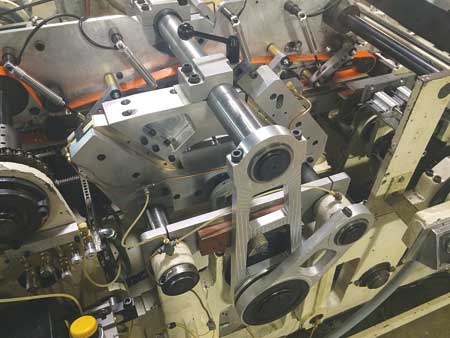
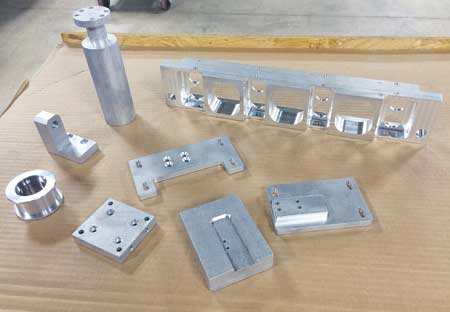
Capturing a New Market: For more than three decades Loudon Machine specialized in the worldwide supply of bindery equipment, parts and service for commercial printing equipment like the custom designed and improved top end of a magazine trimmer (above right). To compensate for a shrinking printing marketplace, the company turned its attention to making custom automotive fixtures and tooling. With the help of Mastercam's Dynamic Machining Technology, CNC machining productivity has increased and the company's sales volume has doubled.
For more than three decades Loudon Machine has specialized in the worldwide supply of bindery equipment, parts and service to the commercial printing industry. But that industry has been in decline and it is unlikely that it will ever be as robust as it once was. For a number of years the company offset the decline in new bindery equipment sales by innovative retrofit and service packages to make existing equipment more productive.
However, by 2011 it had become obvious that the company would have to refocus its manufacturing on another market to be viable for decades to come. The management team decided that it could compete effectively in a highly specialized job shop niche, manufacturing fixtures and tooling for the numerous local manufacturing plants.
"We had dabbled in this business for a number of years and had some success on a very limited basis," said Howard Stuemke, Director of Operations, Loudon Machine. "If we were going to compete seriously for this work we were going to have to get much more efficient at precision manufacturing of one-of-a-kind and two-of-a-kind components. To do this we would need to replace our outdated CAM system and very quickly get proficient in using the new one."
CAM on the Radar
Eric Tompkins, Loudon's Production Manager, surveyed the CAM marketplace and decided that Mastercam from CNC Software would best meet Loudon Machine's needs. Tompkins explained that the addition of this software, three seats of Mill and one of Lathe, has totally changed the way it goes about machining parts.
"The old software would only allow importation of 2D models," said Tompkins. "Programs could not be generated completely within the software but required a considerable amount of manual calculations and G-coding to get them right. This was slow painstaking work, yet crashes still occurred because of the potential for errors with manual data entry. A single skilled programmer who also operated one of the CNC machines performed all of this work. This put a heavy load of responsibilities on his shoulders and management was concerned about the potential problems that would arise should he develop a long-term illness or decide to leave the company."
Cold Turkey
"Today, programs are created based on models seamlessly imported from Inventor, SolidWorks and other CAD software," said Tompkins. Now every machinist writes his own programs. The transition to this mode of operation was accomplished in just two months with the assistance of QTE Manufacturing Solutions, Loudon Machine's Mastercam reseller.
"Basically we bought it; our machinists went to training; we got rid of the old software; and our programmer/machinists used nothing but Mastercam from then on," said Tompkins. "They did not have a choice. There is a learning curve like everything else but after a couple months our productivity surpassed what it was before and has been continuously improving ever since."
During those two months the Loudon programmers relied on assistance from QTE who would answer questions as needed. If that did not work, QTE would review problems the programmer/machinists were running into and email step by step instructions on how to solve them. QTE also worked with Loudon to modify post-processors so that workflow at each of the machines was more efficient.
30-40% Productivity Increase
"One of the best outcomes of the Mastercam training is that it changed the way the guys were machining," said Tompkins. "In simple terms, in the old days they would have had a large cutter taking big heavy cuts while the machine was shaking and vibrating and screaming."
"Now I think their main tool is a half-inch end mill and they are taking smaller cuts at higher speeds, getting a lot more work done and improving tool life. Our parts are not that complicated so our guys can write about 14 or 15 part programs a day. While the machine is cutting one part, they are writing or modifying a program to do another. With this approach we have seen about a 30 to 40% improvement in productivity over the way we did things previously."
Some of the new job shop work the company is generating is getting more complex. Loudon has discovered that the controllers on their older mills simply are not up to running some of these larger programs effectively. Upgrading the controllers would have been cost prohibitive so Loudon has retired two of its older mills and replaced them with new Haas 3-axis CNCs. Loudon expects substantial improvements using equipment that can take advantage of the programming refinements.
One Good Part Deserves Another
"Loudon has no intention of abandoning its printing customer base," said a company spokesperson. "Because of its rebuilding and retrofit offerings, 2013 was one of the best years ever on that side of the business. Remarkably, sales on the job shop side of the business are keeping pace. So in two years, the company has doubled its sales volume with no increases in manufacturing manpower.
"During the past two years, Loudon's customers in the job shop business have taken note of the high quality and increasingly shorter lead times and rewarded the company with more jobs, many of increasing complexity. This led to an opportunity to introduce these customers to broader surface offerings that might include such things as metal coating, electrical and electronic packaging, assembly and engineering. A rapidly expanding volume of work has made it necessary to farm out some work to other shops, sometimes hundreds of miles away. Improved machining capacity with the new Haas mills will allow the company to improve its profitability by retracting a portion of this work."
Stuemke estimates that it may take six to nine months to max out the full capacity of the new 3-axis mills. In the meantime Loudon management is already evaluating the CNC equipment market place. They will be looking for a highly flexible and productive system, perhaps 5-axis, that will allow them to present more unique capabilities tailored to the automotive job shop market niche.
For more information contact:
Loudon Machine, Inc.
709 W Wabash
Effingham, IL 62401
217-347-5066
info@loudonmachine.com
www.loudonmachine.com
Michelle Nemeth
CNC Software, Inc.
671 Old Post Road
Tolland, CT 06084
860-875-5006
info@mastercam.com
www.mastercam.com