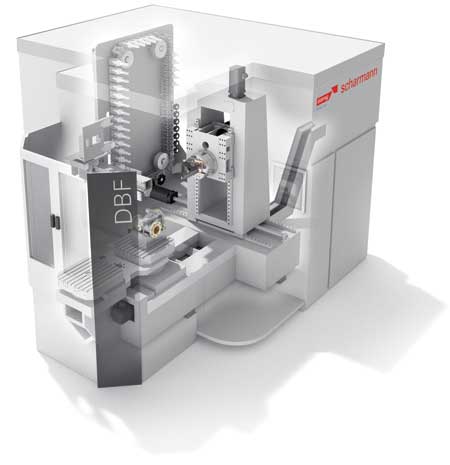
The Starrag Compact DBF series enables precise and efficient machining of pump housings, valves, fittings, sealing flanges and oil well drilling rock bits, according to the company.
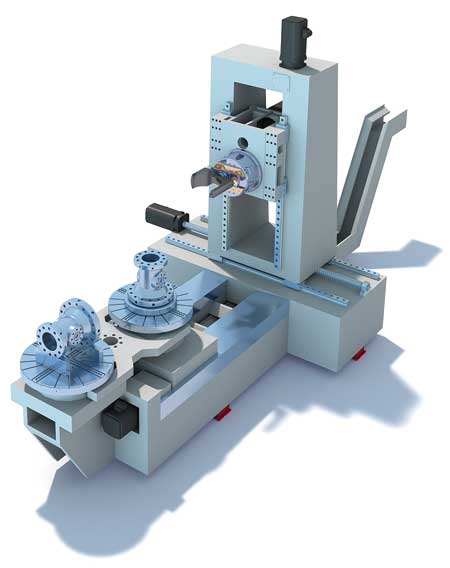
DBF configured with turning table. Example of tubing spool machining.
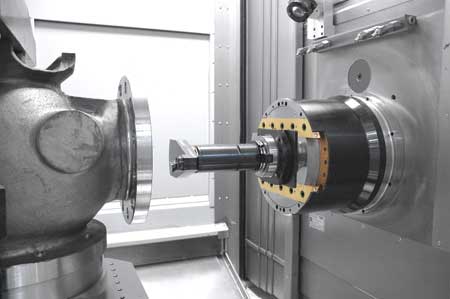
DBF head driven by 60 HP geared spindle - turning tool approaching the valve.
The Starrag Group features its horizontal machining center with integrated U-axis facing head for static turning process of components for the energy market. Facing head technology allows the use of one machine to do both turning and horizontal machining center operations in a single clamping. The company reported that this configuration is productive when manufacturing parts such as pump housings, valves, fittings, sealing flanges and oil well drilling rock bits.
"The valves start as closed-die forgings that are a mixture of carbon and duplex steels, Inconel and super duplex, and are often nickel or alloy-clad," said a company spokesperson. "By definition, such materials create machining problems in both heavy, rough machining and fine finishing, especially when machining the ports and ring grooves."
"The commonalities of these parts are features that require both turning and milling operations," said Bill Archer, Power and Engineering Market Sales Manager for Starrag USA. "The concept of turning, drilling and milling in one setup shortens the processing time with no loss of accuracy caused by re-clamping. No additional machine is necessary to accomplish the multitasking job. At first look, the machine appears to be a typical horizontal machining center. However, when you look closely at the spindle, you notice the U-axis moves across the radial face when the spindle is rotating. This allows turning operations, including contouring, without spinning the part. You do not have out-of-balance problems from these awkward shaped parts when the part remains stationary. Move the cutter rather than the part in turning operations. The internal U-axis can also supply through spindle work coolant for the turning tools, including high-pressure cutting coolant. For normal drilling and milling, the radial facing U-axis slide moves the tools in the center position, as a standard machining center with a 60 HP geared head."
One design feature of the DBF head (translation of DBF in German is turning, boring and milling) is the compensation weights integrated in the head which compensate for the imbalance which occurs in conjunction with balanced tools. Therefore, spindle speeds up to 1,200 RPM are possible for the turning process as well as cutting speeds of up to 9,843 in/m, with constant surface footage. The 60 HP geared spindle accelerates to 3,500 RPM for drilling and milling. The DBF series offers complete machining with radial and axial true running accuracy between 5 and 6 µm.
The Heckert Athletic Series machining center design is the basis for support of the Scharmann DBF head. "The thermosymmetrical machine design and rigidity are the prerequisites for both progressive cutting powers and high precision needed to support the DBF head," said a company spokesperson. "High axis dynamics with rapid traverse up to 2,362 IPM meets the needs of production environments. The open center base configuration allows chips to drop directly into the wide chip conveyor exiting out the back of the machine. The NC rotary table with direct drive up to 80 RPM and input resolution of 0.001° complements the quick linear axis."
As an option, this table can also be used for traditional turning and turn-milling when configured in the MT series (multitasking). The directly driven torque motor for turning the table reaches speeds up to 500 RPM to allow for turning mode with the B-axis rotation. The ability to do both traditional turning of some features on this table and static turning on non-symmetrical features is the key to machining energy components such as valves, said the company.
Tubing spool machining example:
- Setup 1 (90 min)
- Bottom flange: DBF turning
- Bottom and top flange: DBF drilling
- Packing ports: DBF drilling and milling
- Test port: DBF drilling and threading
- Main bore: DBF internal turning
- Setup 2 (70 min)
- Flange diameters: table outer turning
- Packing ports: DBF drilling and tapping
- Connector surface: DBF drilling and milling
- Locking screw holes: DBF drilling
- Drilling/milling mode
- Max. 3,500 RPM
- Max. 60 HP, S1 rated
- Max. 1,250 lbf-ft
- DBF turning mode
- Max. 1,200 RPM
- Max. 1,250 lbf-ft
- Dia. range .5" - 19.5"
- Table turning mode
- Max. 100 RPM
- Max. power 76 HP
- Max. 1,650 lbf-ft
- Max. load 5,500 lbs.
This Compact DBF machine is available in both the 630 and 800 pallet size. Pallets are exchanged by a 180° pallet changer or can be integrated into a multiple pallet machining cell.
Tool handling options include chain magazine up to a maximum of 80 tools or a tower magazine with 180, 240 or 320 pockets and tool lengths up to 800 mm length. A dynamic tool changer driven via hydraulic double arm gripper and spindle positioned parallel to the magazine tool arrangement allow for short chip-to-chip times. The tool changer can change turning tools or milling tools just as with any typical horizontal machining center.
"The DBF machine is built for operators in the demanding production environments; the ergonomic design helps to reduce fatigue. The operator station can accommodate either the FANUC 31i or Siemens 840D sl CNC controls," said the spokesperson.
For over 20 years, Scharmann, with its manufacturing plant in Mönchengladbach, Germany, has provided facing head technology. The Heckert Athletic Series machining center is manufactured at the Chemnitz, Germany, plant.
For more information contact:
Bill Archer
Starrag USA Inc.
2379 Progress Drive
Hebron, KY 41048
850-534-5201
ussales@starrag.com
www.starrag.com