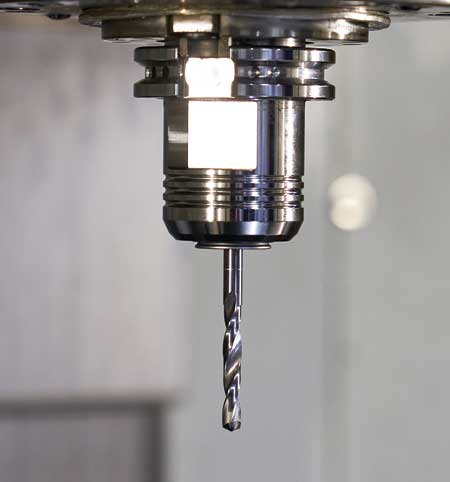
After incorporating two EdgeX4 drills from West Ohio Tool, FT Precision was able to generate nearly 583,000 holes on two production lines without a tool failure, exceeding the company's previous 5,120 hole-per-line performance by an astounding 11,386%.
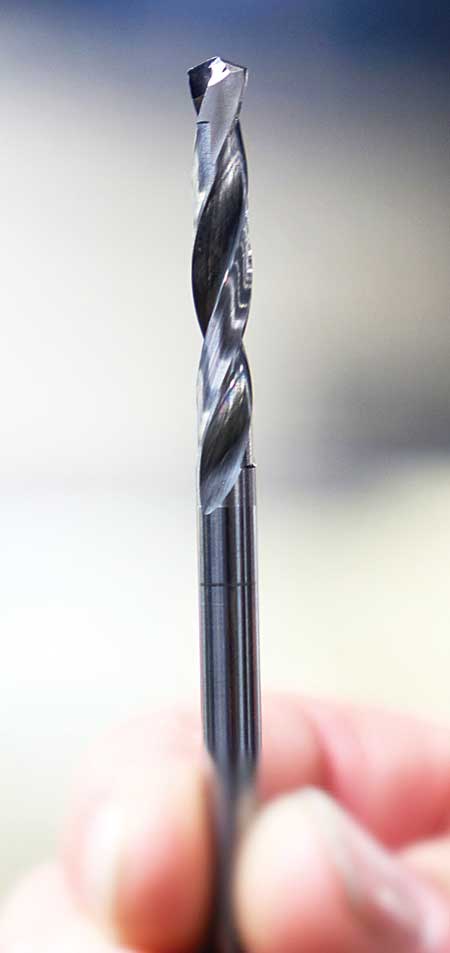
Besides an 11,386% increase in number of holes drilled, FT Precision slashed cost per hole by 98% from 0.0545 cents per hole to 0.00125 cents per hole with its use of EdgeX4 drills from West Ohio Tool.
For more than 20 years, Ohio-based Tier 1 automotive supplier FT Precision, Inc. has been producing and shipping high-precision parts to auto assembly plants across the country. As a prime supplier of aluminum and steel components that include rocker arms, chain tensioners, swing arms and outboard retainers for Honda and Toyota, the company's high-volume production depends on machine uptime along with the best tool life and performance possible.
The company runs banks of multiple drilling machines and CNC transfer machines for rough drilling operations on its rocker arm assembly line that runs 24/7. Roughing hole depths ranging from 14 mm to 17 mm while holding roundness to 20 microns require robust precision tooling to keep pace with the high-volume part processing.
"We ship to five Honda factories daily," said Kevin Davis, the company's tooling team leader, who has been with FT Precision for 25 years. "There are semi-trucks rolling out of here every day full of rocker arms. We are in constant production."
Unfortunately, the company began experiencing excessive amounts of rollover or exit burrs with the mass-produced carbide drills it was using on the aluminum rocker arms. As a result, tooling began to dull and wear prematurely, and Davis knew he had to find a solution to maintain production. With its existing carbide tooling meeting little more than 60% of its targeted goals on the production line, he began searching for alternatives. However, he had to be selective.
"You just cannot test any tool," Davis said. "I cannot afford to take a line or cell off for strictly testing then end up scrapping those parts. I need those cells for production, and I must have a high degree of confidence in the test tool."
The company endured several failed tests in its search for a tool that would keep pace with production schedules. Results were discouraging with tools breaking within a couple of cycles, not providing the required precision or causing excessive burring.
Then Davis heard from West Ohio Tool, and for FT Precision the timing could not have been better. In the past, Davis had worked closely with West Ohio Tool through its founder Kerry Buchenroth and was impressed with West Ohio Tool's responsiveness and ingenuity. Now Buchenroth's daughter, Kaci King, who became West Ohio Tool's CEO when her father stepped away, was reaching out to FT Precision about the EdgeX4 custom engineered, cross-tipped polycrystalline diamond (PCD) drill.
"West Ohio Tool is at the top of the list of the companies I can call and know that they will be over here tomorrow," Davis said. "I knew that we had to give the EdgeX4 a try."
The companies negotiated the terms of a test agreement, and FT Precision set up the EdgeX4 in side-by-side testing with its carbide drills. The results were immediately clear. Since installing the two EdgeX4 tools in December 2022, FT Precision generated nearly 583,000 holes on two production lines without a tool failure, exceeding the company's previous 5,120 hole-per-line performance by an astounding 11,386%. Additionally, the EdgeX4 drills slashed cost per hole by 98% from 0.0545 cents per hole to 0.00125 cents per hole.
Equally important to FT Precision's production efficiency, the EdgeX4 has saved more than 81 hours in downtime attributed to tool changeouts with the standard production carbide tooling. The actual tool life was finally determined after the EdgeX4 performed over 15 months of continual use.
Though the initial cost for the EdgeX4 is a bit more than FT Precision's original carbide drills, the dramatic reduction in overall cost per hole still lowered production costs, which Davis points out, "is what keeps us competitive."
King said she spends a good deal of time educating people about how paying a bit more upfront ultimately leads to sustained performance and cost reductions over time.
"We spend a lot of time helping customers understand that it is not necessarily the up-front costs that matter but the cost-per-hole," King said. "Once customers begin shifting their focus from initial cost to realizing they can significantly extend tool life and reduce production downtime-that is huge," she said.
The EdgeX4 has reaped big benefits for both companies. FT Precision solved a significant production problem and vastly exceeded production expectations. West Ohio Tool further strengthened an already favorable relationship.
"We are really grateful to Kevin because he was willing to stick his neck out for our test tools," King said. "We really do not get that many opportunities to test at facilities, but this was possible as a result of our long-term relationship with FT Precision."
As far as Davis is concerned, the proof is in the drilling.
"I have never seen a rough drill that performed like that," Davis said. "You never know what is coming down the road in the automotive industry because things change from model to model. But as far as I am concerned, the future here is the EdgeX4. My plan is to have an EdgeX4 on every machine producing aluminum parts in the plant."
For more information contact:
FT Precision, Inc.
9731 Mt. Gilead Rd.
Fredericktown, OH 43019
740-694-1500
www.ftprecision.com
West Ohio Tool Co.
P.O. Box 1457
7311 World Class Drive
Russells Point, OH 43348
937-842-6688
customerservice@westohiotool.com
www.westohiotool.com