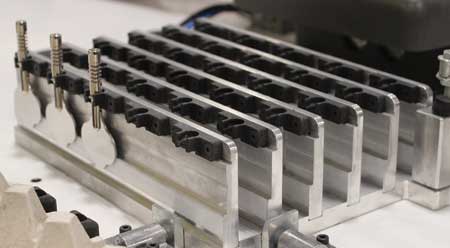
Hipshot Bass Xtender
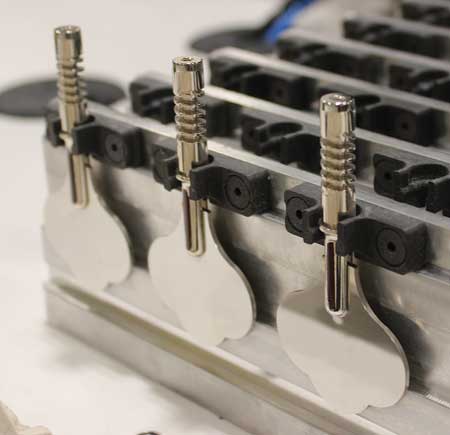
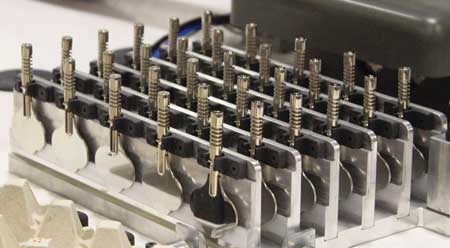
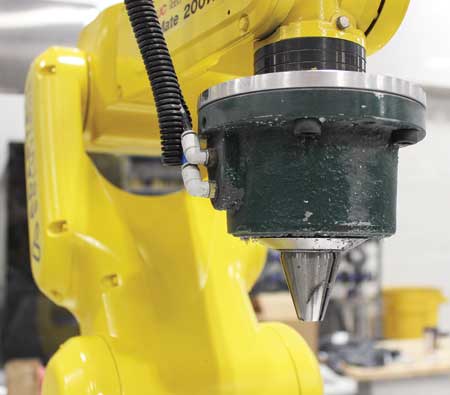
Closeup of end-of-arm tooling on the FANUC LR Mate 200iD
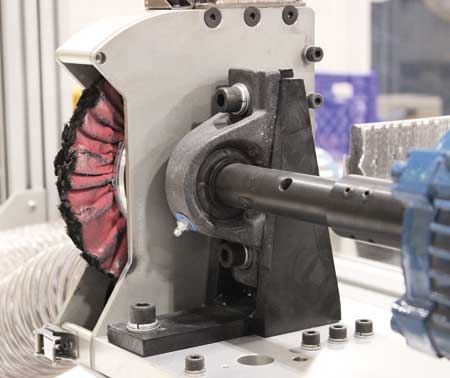
Buffing wheel
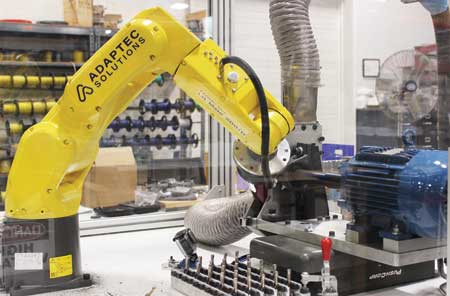
FANUC robot in action
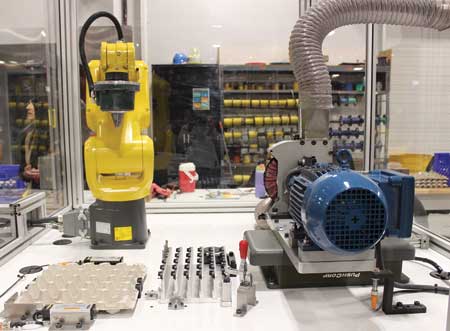
A complete view of the robotic cell.
Hipshot, a manufacturer of high-quality hardware for guitar and basses, faced ongoing labor and production challenges in its deburring and polishing operation. Due to an increase in demand for Hipshot Bass Xtender key, the manual polishing process made it difficult to increase capacity and production of the product. The Bass Xtender product line is a patented extender key that allows bassists to instantly drop the tuning of the low string and bring it back up again with the flip of a lever. Seeking increased consistency, quality and production, Hipshot aimed to integrate a robotic solution to polish their Bass Xtender key. The objective of integrating a robot was not to cut staff, but to automate the least desirable processes, enabling team members to focus on higher complexity or value-added tasks.
The manual operation is extremely dull and repetitive task, requiring an operator to sit in front of a buffing wheel for hours a day. The quality of the polishing,Äîgetting the part to look beautiful and worthy of the end user's instrument is a significant part of the production process. While looking for a solution, Hipshot tried high-energy tumbling and chemical etching, but neither process compared to the high-quality finish produced using a high-speed wheel. The transition from human to machine would be a challenge, since the human can quickly think and react during polishing, while a robot cannot.
Adaptec Solutions, a full-service integration provider, conducted a comprehensive site visit and proposed a solution that provided robotic programming expertise, with Hipshot actively participating in teaching the robotic system how to polish the part. This collaborative effort aimed to mitigate the risk of unfamiliarity with the process and allowed Hipshot to optimize robot motions.
The solution included a FANUC LR Mate 200iD robot, a compact 6-axis robot with the approximate size and reach of a human arm. It combines best-in-class robot weight load capacity with standard IP67 protection. It features a 7 kg payload and 717 mm reach.
The program is set up to teach roughly five or six points per face and per edge. These points are stored in position registers to be reused multiple times with an offset applied to rotate the gripper and handle the backside of the part. The program creates looping patterns based on the predetermined acute recipe. Additionally, a tool offset is applied on J6 to polish the opposite face with the same program and points, eliminating the need for extra teaching. The robot automatically adjusts itself using a user frame and a sensor, measuring wheel wear and compensating automatically.
Adaptec enhanced the solution by incorporating a Variable Frequency Drive (VFD) to the polishing wheel, enabling the adjustment of speed during the polishing process. This provides a level of control not previously possible. The VFD integration transformed a highly manual process into a repeatable and adjustable one, ensuring consistency in output and adaptability to different requirements.
The buffing wheel is mounted to a bidirectional bench mount compliance table to control the buffing force. The Pushcorp AFD-82-3 compliance table provides a compliant force that is proportional to the PSI setting on the regulator. A VFD controls the speed of the wheel. The robot will be able to set the speed during the buffing and compound application to one of four pre-programmed RPMs for rough polish, fine polish and wheel dressing. The combination of wheel speed and table pressure determines the pressure on the key during buffing.
Adaptec collaborated with the customer to design special trays for holding parts, facilitating the loading and unloading of the robot without manual intervention. This customization was essential to meet the unique requirements of Hipshot automation needs.
The solution significantly enhanced the repeatability of the deburring and polishing process, ensuring consistent quality in the finished products. The implemented automation allowed the process to run without the need for a physical operator presence, contributing to operational flexibility.
For more information contact:
Hipshot
8248 State Rte. 96
Interlaken, NY 14847
607-532-9404
info@hipshot.com
www.hipshotproducts.com
Adaptec Solutions
866-761-9338
www.adaptecsolutions.com