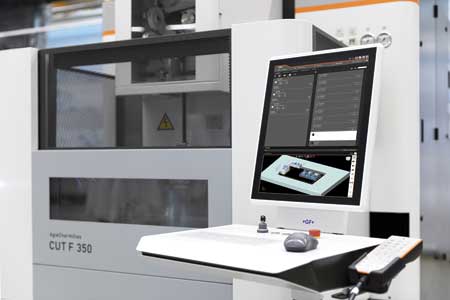
With the development of its Uniqua HMI, GF Machining Solutions merged the best of ISO G-code and Dynamic wire-EDM programming formats into one onboard control.
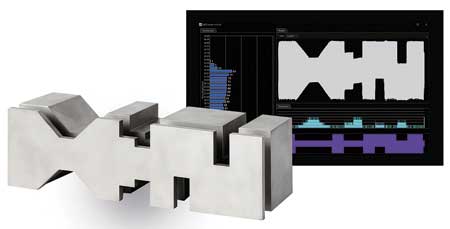
The GF Machining Solutions Spark Track platform detects and tracks each spark generated along the wire during the EDM process and includes the company's Intelligent Spark Protection System (ISPS) that then prevents wire breakage by automatically optimizing cutting parameters.
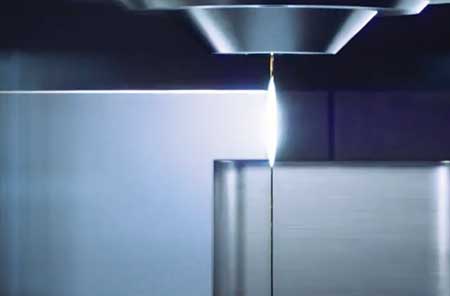
For efficient use of wire, GF Machining Solutions iWire module adjusts wire speed with changing component height/thicknesses during the wire EDM process.
New innovations in control technology continue to push wire EDMs to new levels of speed, ease of use and productivity. By merging the worlds of ISO G-code and Dynamic programming protocols, shops can optimize not only their machines and cutting parameters to changing conditions, but also enhance operator efficiency by reducing the amount of time spent in front of the machine.
Deciphering the Code Worlds
Traditionally, ISO G-code dominated the world of CNC machining, including wire EDMs. Programmer/operators would write or load line upon line of G-codes for axis locations paired with M-codes for particular machine functions. Once the program was loaded and cycle-start button pushed, the program would cascade from beginning to end, directing the machine's every movement and function.
While precise, G-code was (and is) equally rigid in its execution. Any desired deviation from machining parameters contemplated by the original program dictates that the program be revised with a new set of ISO commands. For uninterrupted runs of simple parts, ISO programming has and continues to perform adequately. Deviations of almost any kind, however, can be problematic.
Suppose, for example, that one job already in progress must be interrupted to substitute another job that has taken on a more immediate priority. The machine is stopped, the second job is set up, the ISO program loaded and the part runs to completion. However, prior to resuming work on the original job, the operator must access the ISO program-assuming the operator has the knowledge and/or experience to do so-determine the exact spot in the code where the process was interrupted, then comment out or delete all that came before that point. Only then, can the initial job pick up where it left off. Rerunning that original work wastes a significant amount of production time.
The benefit of ISO G-code is found in its straightforward clarity and simplicity. The machine is told what to do, and it does it. For years, it was the mainstay of CNC programming, and the majority of programmers and operators understood it and used it. As a program, however, it is not at all intuitive, making adjustments cumbersome.
Dynamic Flexibility
Occupying the other programming hemisphere is a format known as Dynamic EDM programming. This method of programming opened up a tremendous amount of flexibility as compared to ISO G-code. Instead of being a rigid programming system with only one predetermined path to a destination, Dynamic programming allows operators to alter the route-similar to modern GPS devices that "recalculate" if a course deviation is encountered. Dynamic programming still gets you where you want to go; you just do not have to stop the program, input a new parameter then restart the program base to continue.
By answering a series of questions on the Human Machine Interface (HMI) in the front of the machine, operators can manipulate and adjust component features and/or job parameters dynamically without re-entering the CAD/CAM system to access and rewrite lines of code that would generate machine commands. Moving or manipulating a feature in ISO requires a code-savvy operator to rewrite the G-code at the machine without having to go back to the CAD/CAM system to input information. Dynamic programming essentially puts the power of CAD/CAM into the HMI, giving the operator ultimate flexibility on the shop floor.
When it comes to necessary job interruptions, Dynamic programming allows the operator to stop the original job, set up and complete the new job and return to the initial piece at the point of interruption simply by answering questions at the HMI. Dynamic programming simplifies and streamlines other operations as well.
Batching, in particular, is a demanding task to program with G-code. Filling a table with a number of workpieces, indexing and locating them then directing machine movements and parameters takes lines upon lines of ISO coding. However, a batching feature built into a Dynamic programming module enables the wire EDM to move from piece to piece very easily until the entire table is finished.
Though rich in time-saving features, Dynamic programming is an extremely sophisticated program and requires experienced operators to fully capitalize on its qualities and capabilities. Additionally, CAD/CAM developers did not provide post-processing utilizing Dynamic programming until 2018-2019.
Breaking Barriers and Building Bridges
Recent advances in wire EDM control technology, however, have bridged the gap between ISO G-code and Dynamic programming, making it appealing to both types of programmers. Now, operators and component designers can choose at the outset whether to use one format or the other. In essence, these new wire EDM controls merge the best of both programming worlds into one onboard control.
One company that was uniquely positioned to blend the two programming strategies for the wire EDM sector was GF Machining Solutions, which is currently celebrating 70 years of EDM innovation. The company's acquisition of EDM market leaders Charmilles and Agie put both programming protocols under one roof. Agie created the Dynamic programming strategy for its machines, while Charmilles was rooted in the traditional ISO G-code format.
For the past several years, the company has been slowly merging the best of each format into its advanced Uniqua HMI for wire EDM machines. The Uniqua control was designed to make Dynamic programming straightforward and easy to understand. Now operators accustomed to ISO programming as well as inexperienced operators can get the most from wire EDM and effectively manage and optimize their processes.
Apart from providing a choice between ISO and Dynamic programming in programming toolpaths and machining parameters for a variety of components, these Dynamic control programs allow operators to optimize the time they spend in front of their machines. Uniqua, for example, uses an execution mode that provides a timeline for a given operation-roughing cutaways, for example-with an icon indicating when the operator needs to be at the machine to unload the slugs. In the interim while the machine is cutting, that individual can be setting up another wire EDM and improving productivity.
Worktable set-up, orientation and measuring are also simplified with advance control technology. Once a piece is fixed to the table, a "measure" function can indicate in and touch-off a part for determining its exact table location. These capabilities often include a feature that can map the most effective table orientation for multiple parts to facilitate the most efficient cutting path.
In short, the latest generation of advanced wire EDM control technology reduces programming and set-up time and allows operators to fix problems on the fly at the machine, improving operator productivity and efficiency.
Multipiece jobs also have features that streamline batching by ordering the work process for maximum efficiency with just a push of a button. A table stacked with many components that require roughing, skimming and finishing can be processed by the control in a way that requires the operator to return to the machine only after the entire batch in completed, instead of being present to remove each component as it is completed. This type of operation can be accomplished with G-code, though it is difficult and requires an experienced programmer.
These latest control technologies also incorporate advanced graphics functions at the HMI that further enhance ease of use. Operators can click on a graphical representation of a component feature, for example, to access the programming code and parameters for that feature. The graphics functions also can serve as a simulation and validation for the process right at the machine.
Taking Control to the Next Level
In addition to their robust internal proficiencies, these advanced control programs allow developers to incorporate and access additional technology that cuts production time and expense. The GF Machining Solutions Intelligent Spark Protection System (ISPS), for instance, prevents wire breakage by monitoring spark distribution along the wire to automatically optimize cutting parameters. As a result, maximum machine efficiency is achieved without manual tuning.
ISPS is part of the company's Spark Track platform that detects and tracks each spark generated along the wire. The data collected is used by other GF Machining Solutions modules, such as iWire, that adjusts wire speed with changing component height characteristics. By adjusting wire speed to differing material thicknesses, shops can use wire as efficiently as possible.
In a strict G-code environment, compensating wire speed and other parameters to varying cutting conditions requires coding a technology change (wire speed, for instance). With Dynamic programming and advanced HMIs, however, data is fed into the control, and the machine automatically makes the appropriate adjustments.
Current advances in wire EDM control technology, as well as those in development, will not only benefit the shops that use them, but their customers as well. By easily and quickly programming machine paths for simple and complex parts, optimizing operations and machinists' time at the front of their machines, shops are able to capitalize on wire EDM's unique capabilities and expand its role in the manufacturing sector.
For more information contact:
GF Machining Solutions LLC
560 Bond St.
Lincolnshire, IL 60069
800-282-1336
info.gfms.us@georgfischer.com
www.gfms.com/us