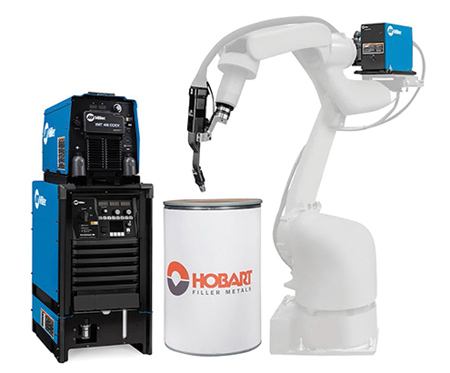
The new Hercules welding system from Miller, Hobart and Tregaskiss is a single-wire, high-deposition, automated MIG welding system that boosts welding productivity rates without the expense of adding more weld cells, according to the spokesperson.
Miller Electric Mfg. LLC, Hobart Filler Metals and Tregaskiss has announced the release of the Hercules single-wire, high-deposition, automated MIG welding system. The Hercules system significantly boosts welding productivity rates without the expense of adding more automation welding cells, according to the spokesperson.
"The system delivers a gain of up to 30% or more in deposition rates and corresponding productivity with no loss of weld quality," said the spokesperson. "Even operations that have optimized processes and consider themselves at the forefront of high-deposition-rate welding can benefit from the Hercules system."
"With Hercules, operations can go beyond the welding productivity it thought was possible, making it more competitive and profitable," said Seth Perrin, Advanced Welding Product Specialist, Miller. "This system sets the bar for state-of-the-art welding deposition rate."
The Hercules welding system is suited for medium to large manufacturing operations with robotic welding, specifically for those with long welds in the flat and horizontal welding positions. The system has been in a soft introduction phase with targeted Miller customers for several years, and Miller has worked with those customers to integrate the system.
"During the soft launch, we used customer feedback to continually improve the Hercules process to where it is today," said Perrin. "That valued relationship and feedback made us aware of where the system was lacking and therefore, we were able to revise the process to make it more reliable and robust. We thank our loyal customers."
Developed by Miller, Hobart and Tregaskiss, the Hercules MIG welding system combines Miller power source and wire-feed technology, a Tregaskiss torch and a specialized Hobart metal-cored wire. According to the companies the components include:
- Miller power sources and Hercules drive: Auto-Continuum 500 and XMT 450 power sources work together with the Hercules drive to deliver the amperage needed for the system and fast, precise wire-feeding.
- Tregaskiss Hercules torch: The torch has dual contacts that allow two sources of power input, which are crucial for the high-deposition welding process. Created specifically for the Hercules system, the torch's unique single-wire, water-cooled design maximizes electrical conductivity and optimizes filler metal delivery to the weld puddle.
- Hobart FabCOR Hercules metal-cored wire: Formulated exclusively for the Hercules system, FabCOR Hercules is the only metal-cored wire that can accommodate faster travel speeds to deliver the system's higher deposition rates and productivity while maintaining arc stability.
"Manufacturing operations can eliminate welding bottlenecks and unlock unutilized capacity with the Hercules system, all without adding more automation welding cells that require additional floor space or brick and mortar," said the spokesperson. "In many cases, the system does not require all-new welding automation, allowing operations to use equipment that is already in place. The Hercules system offers simple integration being easy to set up and install for EtherNet/IP, DeviceNet or Analog protocols."
For more information contact:
Miller Electric Mfg. Co.
P.O. Box 1079
Appleton, WI 54912
920-734-9821
info@millerwelds.com
www.millerwelds.com