
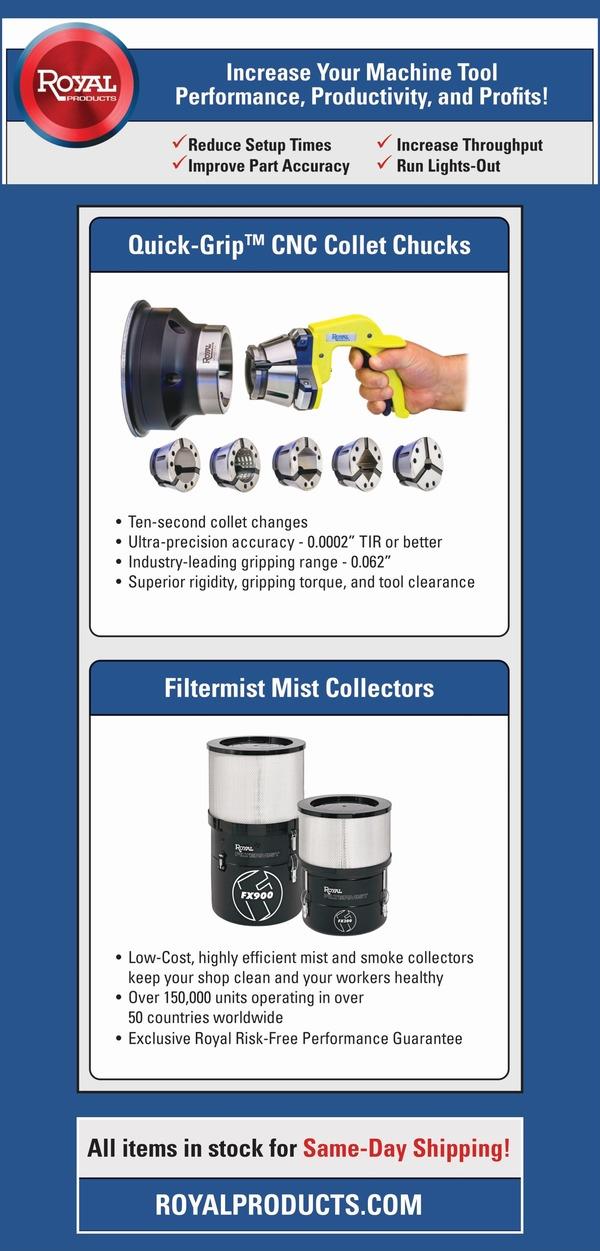
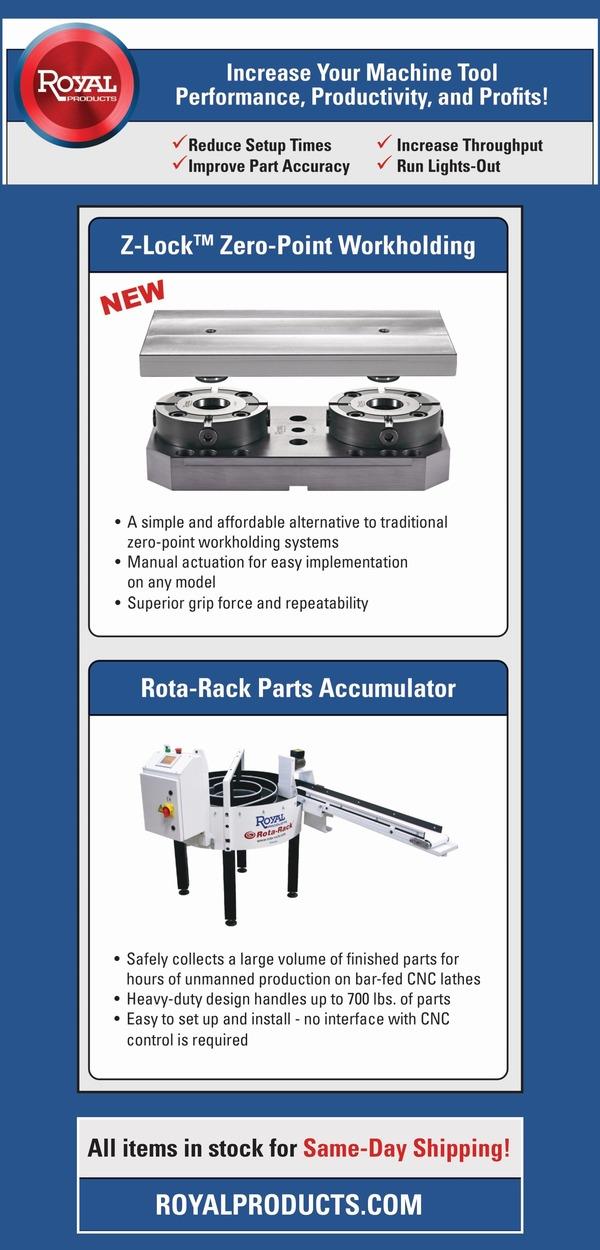

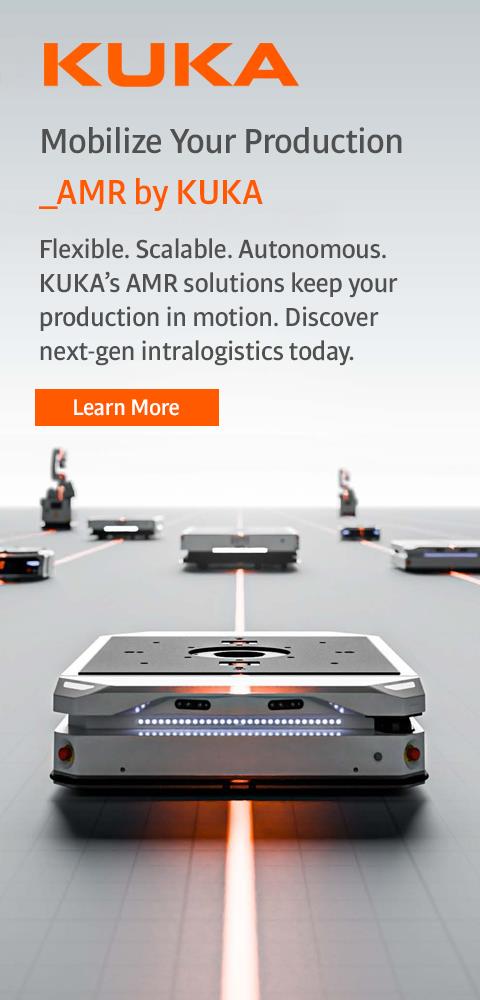
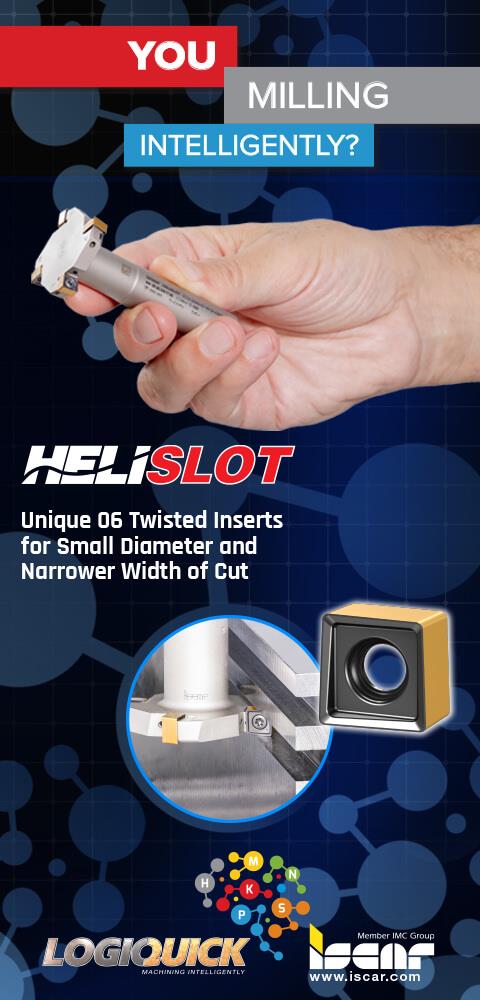
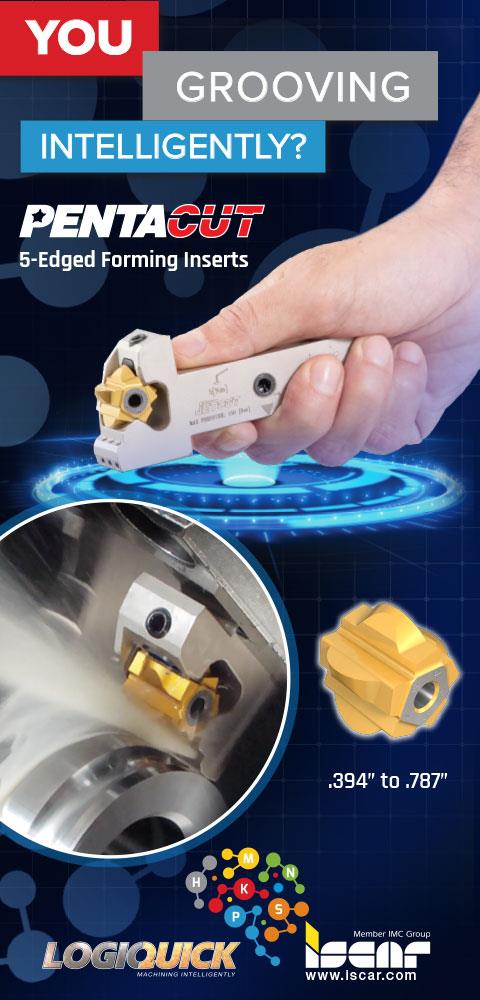
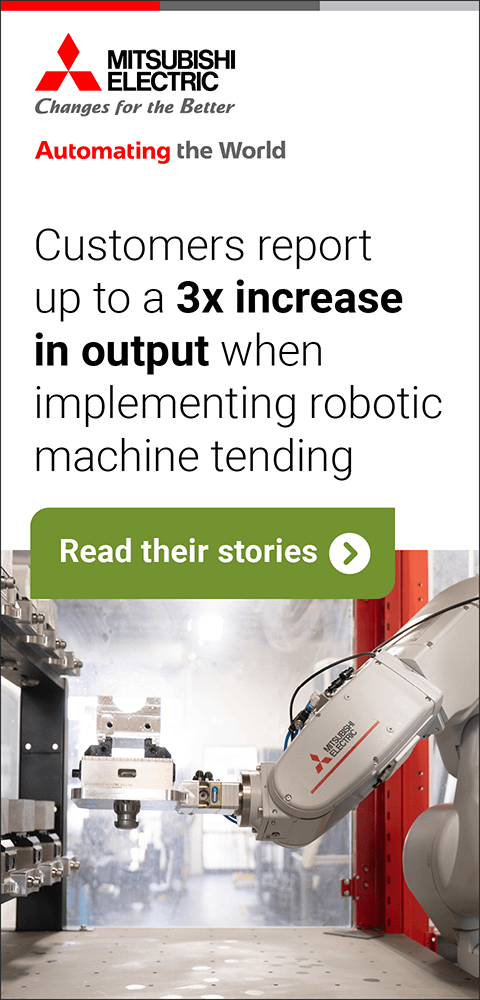
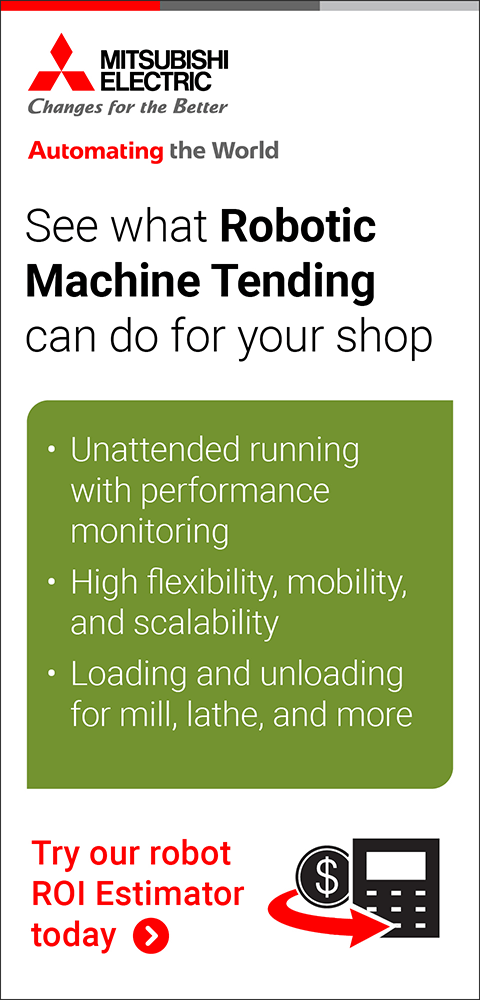
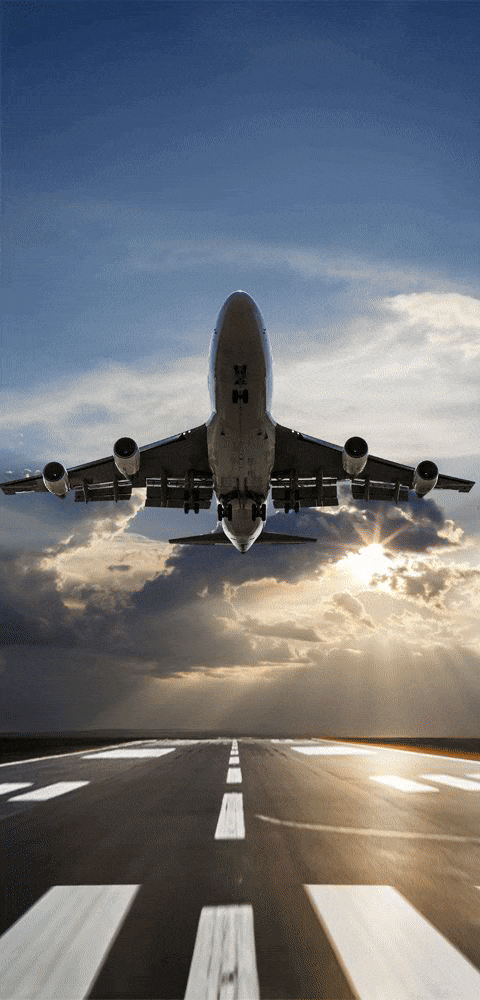
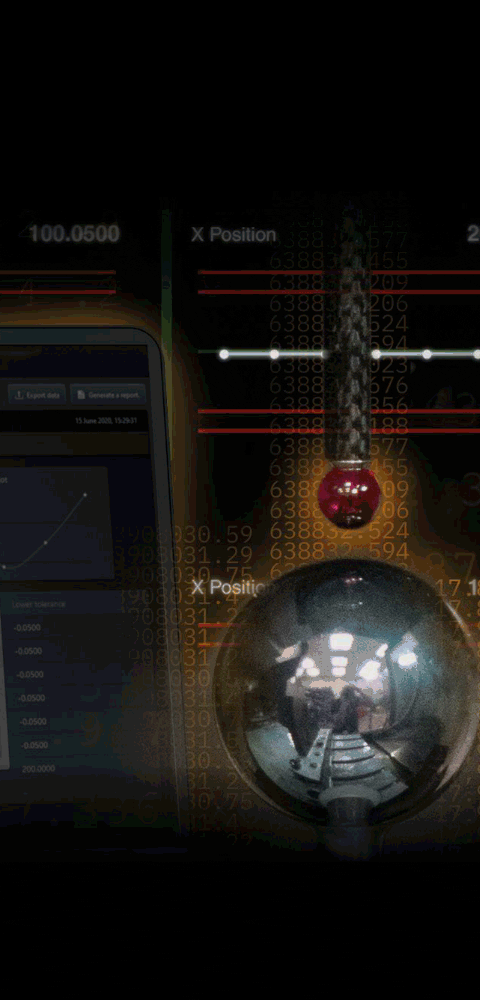
Welding Robot Provides Extra Long Reach; Reduces Need for Tracks
April 1, 2018
The Motoman MA3120 arc welding robot by Yaskawa Motoman features an extra-long reach arm that reduces the need for tracks. "It is the longest robot arm designed for arc welding," said a company spokesperson. Available in floor-, wall- or ceiling-mounted configurations and suitable for multiple robot layouts, the MA3120 has been improved over the previous MA3100 model robot with twice the payload, longer reach and improved through arm wrist design for arc welding.
The MA3120 has a 6 kg payload, 3,121 mm horizontal reach and ±0.15 mm repeatability. Its integrated through-the-arm cabling is designed to eliminate cable interference, simplify programming and reduce cable wear. It has heavier payload capacity and an increased through hole wrist diameter making it easier to integrate pull-torches or welding sensors. Welding utilities (gas hose and feeder signals) can be routed through the robot base and the wire feeder mounts to the upper arm to reduce the torch length. The MA3120 is suitable for use in workcells with larger workpieces, such as automotive frames, agriculture parts and construction machinery. It is also suitable for applications that require access to parts in tight spots or those with possible interference from fixtures.
The DX200 controller features patented multiple robot control technology to easily handle multiple tasks and control up to eight robots (72 axes). The DX200 has been designed to improve process capability, reduce energy usage and improve maintainability and safety. An enhanced functional safety unit (FSU) provides control-reliable zone and tool position monitoring, standstill monitoring and speed limiting. This can reduce costs for safeguarding hardware, and it provides capabilities such as collaborative tasks. It is compliant to ANSI/RIA R15.06-2012 and other relevant ISO and CSA safety standards.
For more information contact:
Yaskawa America, Inc.
Motoman Robotics Division
100 Automation Way
Miamisburg, OH 45342
937-847-6200
www.motoman.com
< back