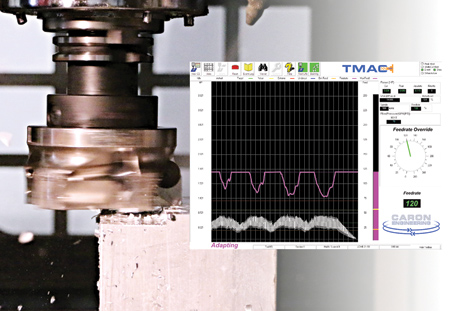
TMAC can monitor rough, low RPM cuts using the new Sawtooth feature of adaptive control. With the new Sawtooth algorithm, TMAC learns the tooth pass frequency of each tool to respond to the entire tool's cutting, instead of each tooth.
Tool monitoring is essential to improving and understanding the CNC machining process. Tool monitoring, particularly with an adaptive control, optimizes cutting and tool life, especially with varying material conditions. This is most critical for industries such as aerospace. Aerospace components, primarily engine components, are made from materials that are very tough to machine, such as titanium, Monel, Hastelloy, Inconel and other composite materials. In order to maintain the integrity of a part, (which is essential for aircraft standards), many aerospace parts are machined from solid blocks of material. In these cases, the operator must program the CNC for the worst material condition.
Caron Engineering's TMAC MP (Tool Monitoring Adaptive Control with Multi-Process monitoring capability) has optimized machining for the aerospace industry using adaptive control. TMAC's high-speed processor communicates with a multi-range power transducer to learn the optimum power load per tool. TMAC's adaptive control overrides the feedrate to maintain a constant motor power. The adaptive control automatically increases the feedrate with low power cuts and decreases the feedrate with high power cuts and as tools wear, since more power is required as the tools' cutting edges deteriorate. "Adaptive control significantly reduces air cutting and saves valuable time on low power cuts. Typical cycle timesavings with TMAC range from 20-60%," said a company spokesperson.
Caron Engineering's latest version of adaptive control includes a Sawtooth feature that is more robust for lower RPM cutting. With TMAC's traditional adaptive control, slow RPM cutters (under 1,000 RPM) created a spike with each tooth passing through the material. The feedrate would adjust to each of those power spikes.
With the new Sawtooth algorithm, TMAC learns the tooth pass frequency of each tool. Using the learned frequency, TMAC can calculate the exact power oscillation of each tooth coming though the material. TMAC will use the average power of all flutes of a tool for adaptive control. This allows the adaptive control to respond to the entire tool's cutting, instead of each tooth. Due to the material complexity of aerospace components, this new Sawtooth feature is heavily utilized in this industry to adapt to these rough, lower RPM cuts.
TMAC safeguards and optimizes the machining process with these difficult to machine materials. In addition to power, TMAC communicates with a variety of different sensors, including vibration, strain, coolant pressure, coolant flow and spindle speed. These IIoT enabled sensors collect a large amount of data for process diagnostics, system integration and advanced analytics.
"Adaptive control will reduce cycle time and increase tool life, but the hidden benefit is allowing more unattended operation and quick reaction to part and material anomalies," said Rob Caron, President of Caron Engineering.
For more information contact:
Caron Engineering, Inc.
1931 Sanford Rd.
Wells, ME 04090
207-646-6071
marketing@caroneng.com
www.caroneng.com