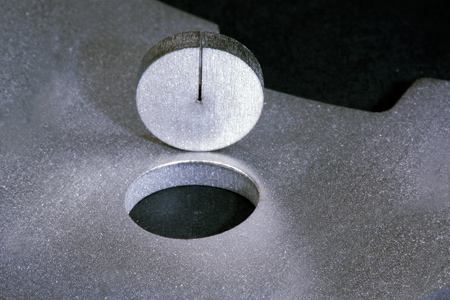
A clean and robust pierce using the SmartPierce process from Prima Power Laserdyne ensures a clean hole and cut as pictured. SmartPierce governs the overall quality of the laser processed feature.
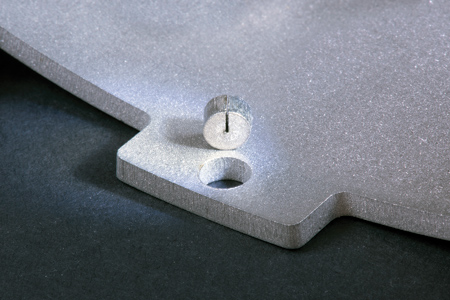
Intricate features with precise positioning and dimensions are possible using the SmartPierce laser process.
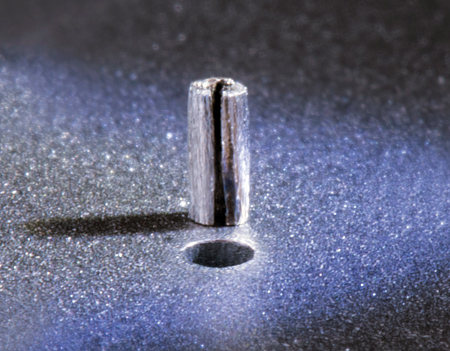
SmartPierce is equally effective for thick or thin metals with a debris-free, clean pierce. Pictured behind the laser trepanned hole is the slug from the hole. The clean, narrow pierce leads to a well controlled, high quality hole with negligible debris.
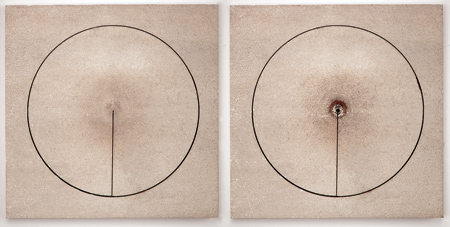
Laser cuts in 10 mm thick 304 stainless steel. The pierce point with SmartPierce (left) is the same diameter as the cut width (kerf). Using a traditional piercing method with fixed laser parameters (right), the pierce diameter is much greater compared to that using the SmartPierce process.
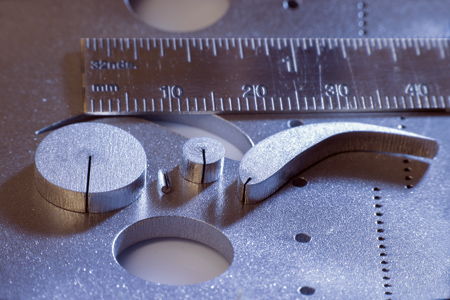
Slugs from precision cutouts of airfoil shapes and round holes in 3.5 mm thick stainless steel. The clean, high quality start is made possible by the LASERDYNE SmartPierce process.
SmartPierce enables drilling a pattern of 1,940 holes of 0.4 mm diameter holes at 0.8 mm center-to-center spacing in 1.5 mm thick stainless steel. Holes were drilled in less than 0.5 sec. per hole while avoiding distortion of the part or plugging of previously drilled holes with drilling debris.
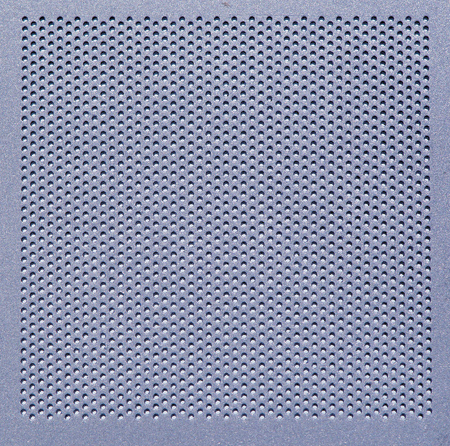
Regardless of material type and thickness, laser cutting and drilling (trepanning) processes for 2-D and 3-D parts begin with piercing that governs the overall quality of the feature. In other words, if the pierce is clean and robust, the stage is set for a clean hole or cut.
Importance of Clean Piercing
The fiber laser is intrinsically more energy efficient than previous generations of gas and solid state lasers, which was an early driver for laser users to adopt fiber lasers. Since energy is a major component of operating cost, the fiber laser has made laser processing more economical, opening the process to a greater number of applications.
Most 2-D and 3-D laser cutting systems make use of continuous wave (CW fiber) lasers from 2 to 6 kW average power. The choice of average power is based primarily on the thickness of materials to be cut and the required cutting speed. Higher average power can increase efficiency in cutting large radius or straight profiles. However, higher average power does not necessarily increase efficiency for all parts, especially those requiring high precision and involving many small features.
High power quasi-continuous wave (QCW) fiber lasers have dramatically increased the efficiency of laser processes used for precision cutting and percussion drilling of 2-D and 3-D parts that involve many features (pierces).
The QCW variety of fiber lasers offers even more. With average power up to 2 kW, a wide range of pulse parameters and the speed with which laser conditions can be changed, the high power QCW fiber laser has given rise to high processing speeds, increased quality and even new capability. With this flexibility and range of laser parameters available, it is common for a single 3-D laser system with a high power QCW fiber laser to find more applications for laser cutting, welding and drilling. This is especially true in job shops and production operations involving low volume, high value part production.
But just as this opportunity grows, so does the demand for higher laser processed productivity and quality. That is where the importance of advanced integrated laser and process control enters the picture.
Prima Power Laserdyne seized on the opportunity QCW laser systems provided and multiplied the potential with its Smart Techniques. This was possible because QCW fiber lasers operate in both CW and high peak power pulsed modes. The peak power in QCW mode is up to 10 times higher than the average power, allowing the system to do much more, especially when operating with Laserdyne's SmartTechniques.
Applications for QCW Lasers Equipped with SmartTechniques Grow
Laser system operating costs are a major consideration for every manufacturer. Considering that QCW fiber lasers provides much lower electrical usage (the main component of operating cost for laser systems in general), no replacement consumables, much lower overall maintenance and little lost time due to warm up, using systems with SmartTechniques makes more sense than ever. Here is why.
Working smarter, not just harder, starts with Laserdyne's advanced integrated control of all laser, motion, assist gas and process sensors along with its unique processing techniques. This article illustrates how one of the SmartTechniques-SmartPierce-is impacting 3-D laser processing in leading manufacturing industries.
An Intelligent Prerequisite to Successful Cutting and Drilling
A clean and robust pierce ensures that the stage is set for a clean hole or cut. If the pierce is poor or incomplete, there is significant opportunity for cut quality to be poor or, in some cases, for the cut to fail. In other words, a robust pierce is a prerequisite for every reliable laser cutting and drilling process.
Consistently high quality is key whether in aerospace and medical device parts produced in expensive, exotic alloys or produced in common steel and aluminum alloys for the automotive, electronics and a host of other industries.
SmartPierce contributes to a robust pierce by optimizing pierce parameters as the process progresses through the thickness of the material. In thin metal, the impact can be significant, particularly in terms of quality as measured by cleanliness of the finished part. For thicker materials, the opportunity for both greater throughput and quality improvements can be much greater.
Following is a review of the impact of the unique piercing capability with SmartPierce on productivity, quality and capability of precision laser processing.
Three Ways SmartPierce Leads to Increased Productivity
There are three important ways in which SmartPierce with the high power QCW fiber laser increases productivity: (1) by reducing the time to complete the pierce; (2) by reducing the distance of moves from the pierce point to the cut profile; and (3) by reducing, or in some cases eliminating, post processing (e.g. deburring or removing debris from piercing) of cut and drilled parts.
Reducing the Time to Complete the Pierce Minimizes Material Removed
The main laser parameters for piercing are pulse width, peak power and pulse frequency. Assist gas type and pressure are also important to achieve minimal pierce time without compromising quality.
With SmartPierce, laser parameters are optimized as the pierce cycle progresses through the thickness of the material to control the removal of laser-melted metal. This optimization minimizes the volume of material removed and maximizes the material removal efficiency with depth. One consequence is that the reduction in piercing time is greater as the material thickness increases. For example, pierce time for 9 mm thick carbon steel is 2 seconds with a standard continuous wave (CW) piercing process. With SmartPierce, piercing takes 0.5 seconds.
Piercing on the Cut Profile Reduces Cycle Time
With a smaller, more controlled pierce point comes an ability to start the cut near the cut line. Those familiar with laser cutting know that it is common to pierce at or near the center of a feature to be cut, then move to an edge of the profile and follow the profile to make the cut before returning back to the pierce point.
When cycle time is a priority, as is the case with most medium and high volume component fabrication, the distance of this move is minimized while ensuring that the pierce related debris is contained within what becomes the scrap from the part feature. The shorter the distance between the pierce point and the profile the better, from a cycle time standpoint. In fact, it is best if piercing occurs on the edge of the feature to eliminate additional moves.
SmartPierce minimizes the diameter of the pierce point. In many applications, this means that piercing can begin on the profile edge. In fact, the requirement to start on the profile was one of initial drivers for development of SmartPierce.
Piercing Reduces and/or Eliminates Post Processing of Cut and Drilled Parts
Minimizing debris created during piercing reduces-and in many cases eliminates-the need for post-cut finishing of the surface. A common application in production of stator rings for both aero-engines and turbines for power generation is cutting of airfoil shapes in nickel alloys and stainless steel rings. Slots require clean, precise edges with minimal taper since a subsequent process involves brazing or laser welding blades into the slot. SmartPierce minimizes the amount of debris within a slot and in previously cut slots, minimizing the degree of cleaning of the rings required before brazing or welding.
Controlling Piercing Debris Improves Quality
Better control of piercing through SmartPierce with the QCW fiber laser reduces the amount of debris that is formed. Until the pierce is completed, all of the material in the pierce volume must exit from the top surface. For high power lasers operating in the microsecond and millisecond pulse regime, the mechanism for removal of this material is referred to as melt expulsion.
Melt expulsion involves molten metal particles being ejected from the pierce volume. The laser melted and expelled metal rapidly cools, falling onto the surface of the part or onto the edges of previously cut features. Minimizing the amount of debris is key to producing high quality parts as measured by: (1) surface appearance, (2) consistency of the pierce and (3) distortion.
One of the key challenges when creating dense patterns of laser cut or drilled features is avoiding contamination of previously cut features by piercing debris. Sometimes directing the debris from piercing onto the unprocessed material is used to prevent contamination of previously cut features. However, this is not a perfect solution in that the resulting rough surface is not conducive to precision gas assisted cutting since the roughness disturbs the flow of assist gas into the cut. Minimizing debris from piercing that attaches to the part surface leads to more consistent processes and higher quality laser processed features.
Another challenge in laser processing dense patterns of features occurs when molten metal spatter from piercing collects on the part surface. With this comes local heating of the part, which in turn leads to distortion or a non-uniform residual stress condition on the surface.
Distortion of the part from heating is more evident in thin materials. When this occurs, the stresses created by molten metal spatter heating the part on one side often is sufficient to bend the part, especially for sheet thicknesses.
For thicker materials, localized heating from metal spatter may not be sufficient to distort or bend the part. However, the surface is left with a residual stress that depends upon many factors. Residual stresses cannot be ignored in parts that involve fatigue cycling since these add to applied stresses and define a total stress state within the part material during use.
SmartPierce Expanded Capability Includes Wider Range of Materials
SmartPierce with the high power QCW fiber laser has enabled new applications based on a capability that was previously limited to a narrow range of materials or that required processing at speeds not economically feasible.
With SmartPierce, the ability to produce a dense pattern of small features has created new opportunities, including the production of intricate patterns in spray nozzles and spinneret and for fabrication of filters in a variety of materials and 3-D shapes. Changing laser parameters in microseconds has enabled production of distortion-free parts with clean, debris-free holes.
Additional SmartTechniques Enable New Applications
SmartPierce is one of a family of application-inspired capabilities for high quality precision laser processing. Separately and in combination, SmartTechniques build on the basic capability of the high power QCW fiber laser to expand the range of 2-D and 3-D laser cutting, welding and drilling processes for which laser processing is both economical and capable and is being adopted widely in many applications around the world.
SmartPierce is one of an entire suite of SmartTechniques available in all Laserdyne system models. In addition to SmartPierce, the SmartTechnique suite includes SmartRamp, SmartSense, SmartPerf, SmartShield and SmartStop. Laserdyne's advanced, integrated control of all laser motion and process sensors along with its processing techniques allow users to achieve enhanced results.
Authored by Terry L. VanderWert, President, Prima Power Laserdyne
For more information contact:
Prima Power Laserdyne
8600 109th Avenue North, #400
Champlin, MN 55316
763-433-3700
lds.sales@primapower.com
www.primapowerlaserdyne.com