
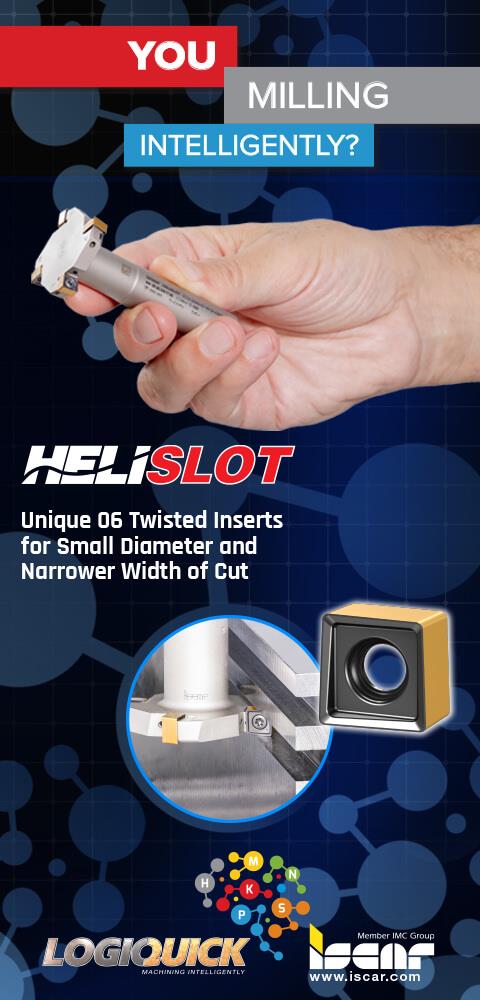
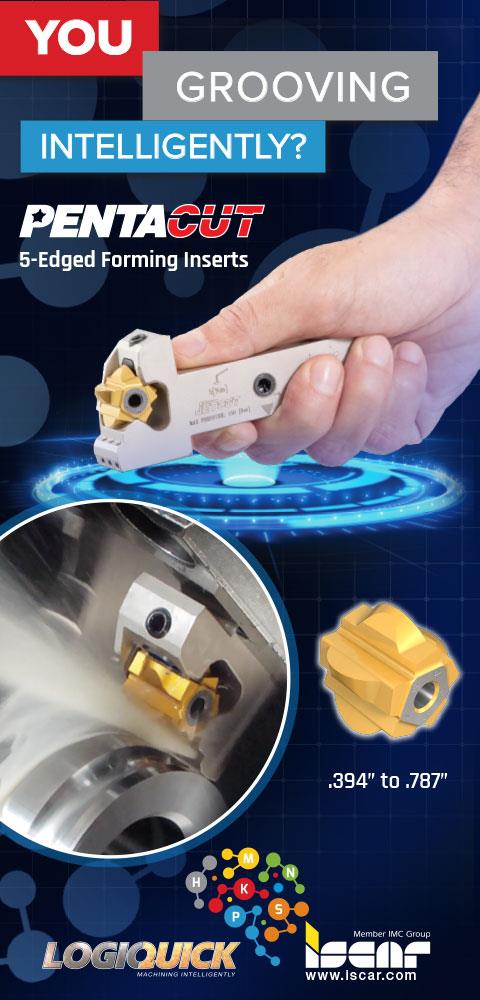
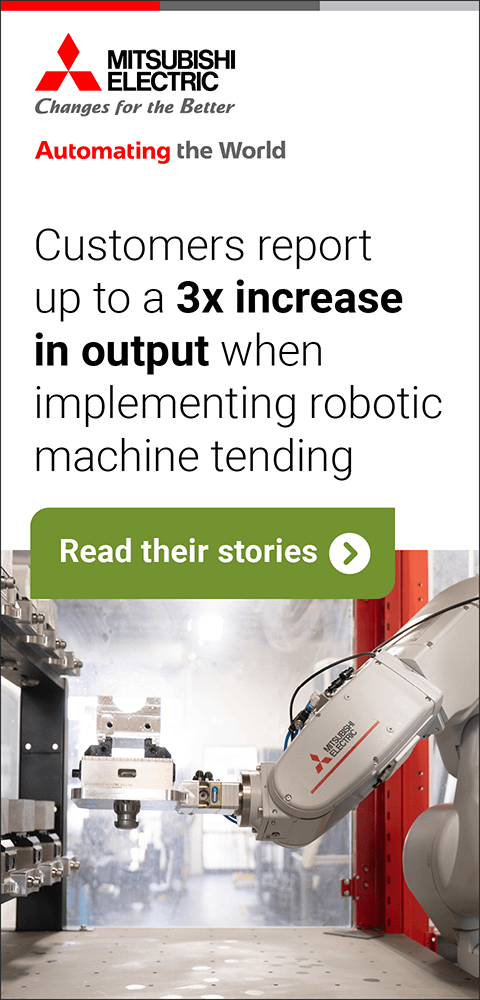
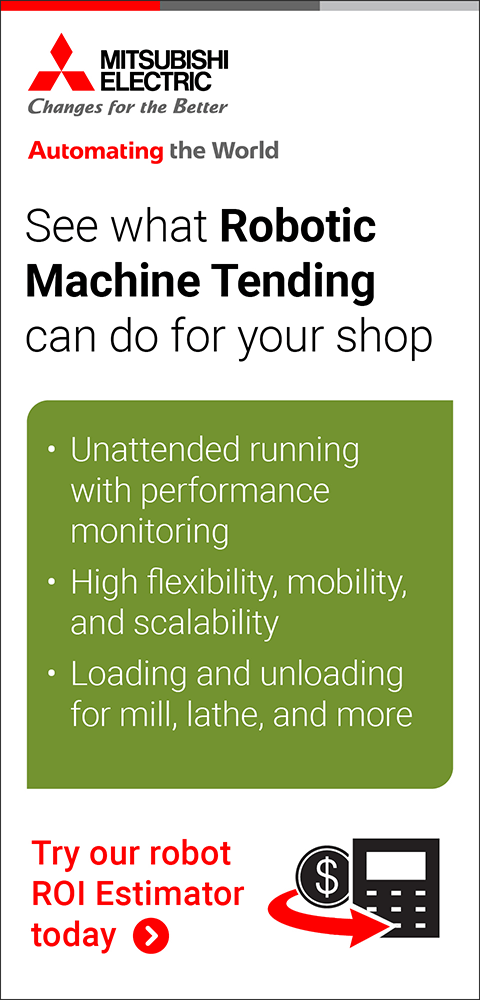
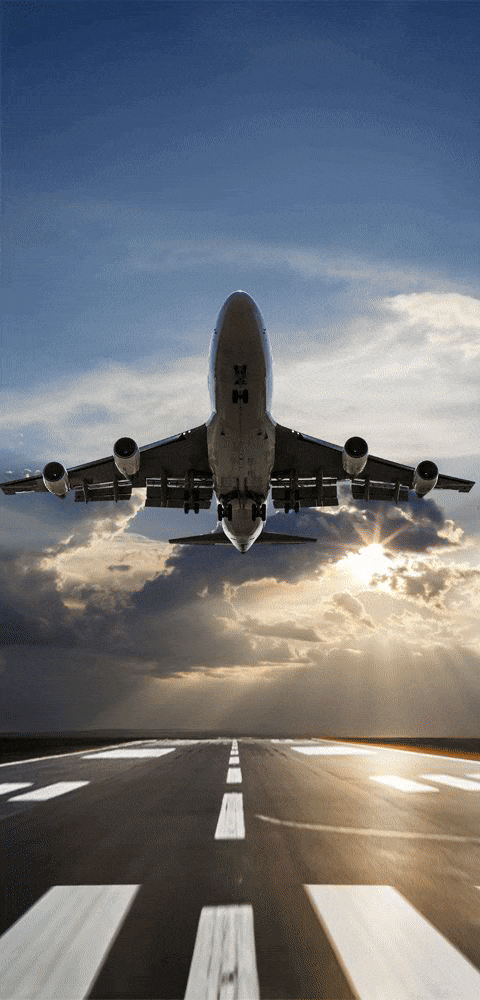
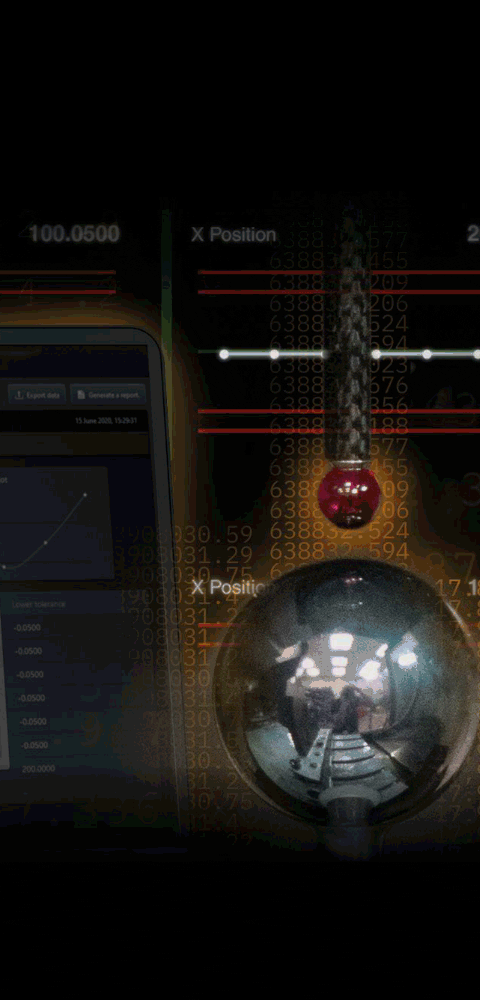
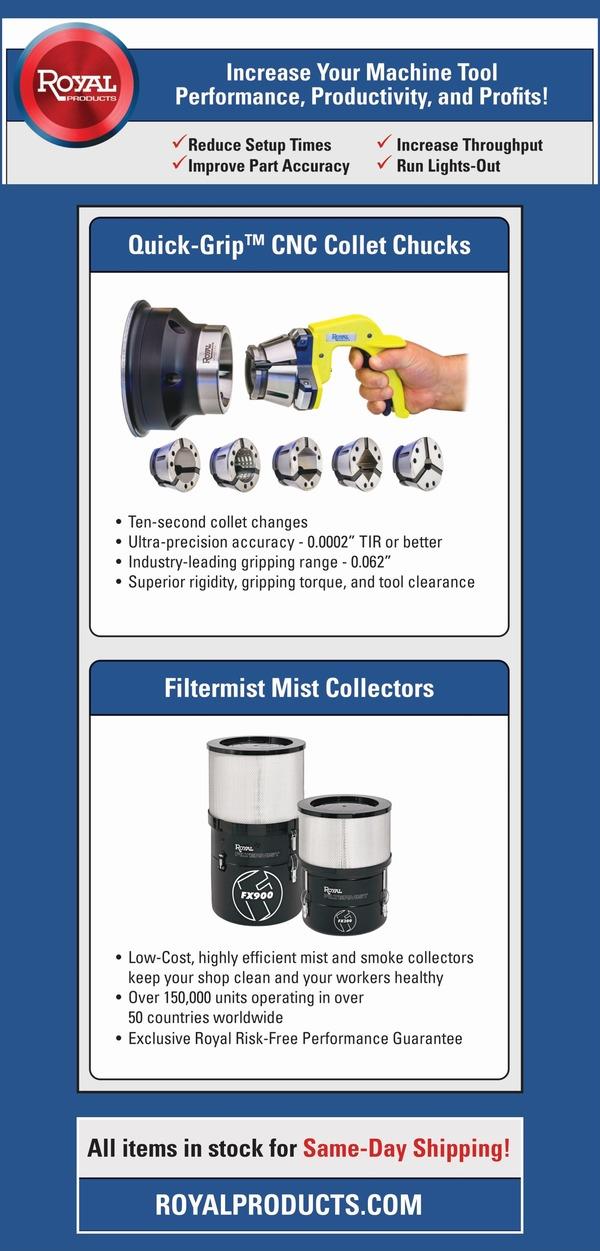
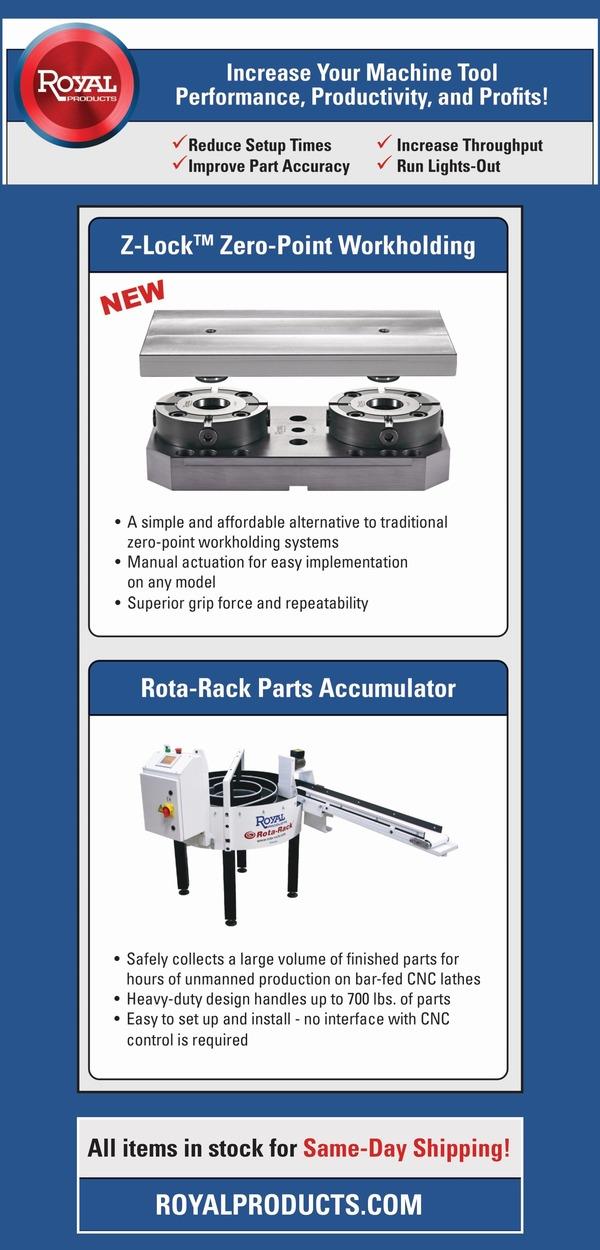

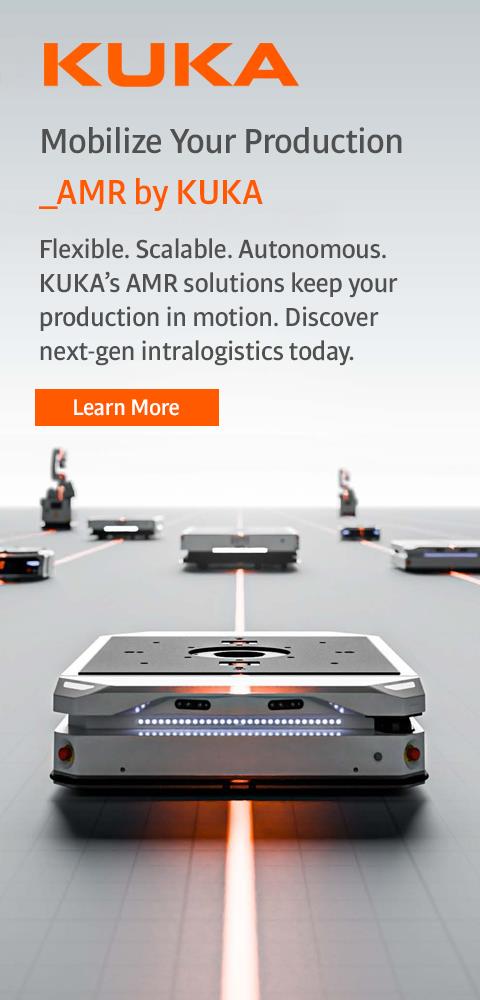
Copper Added to Metal AM Capabilities
August 1, 2017
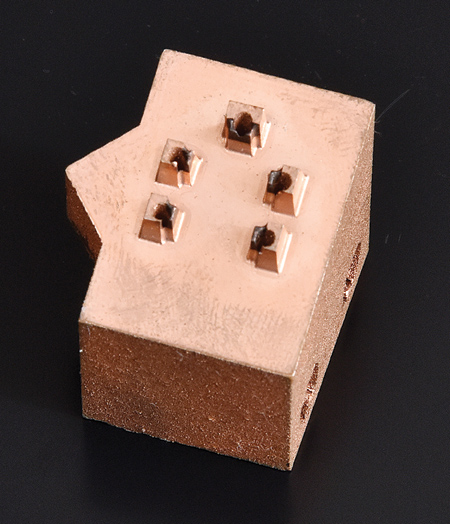
A copper EDM sinker with internal channels showcases Linear AMS' capabilities in printing copper alloys.
Focusing on improving process knowledge and metallurgical understanding in metal additive manufacturing (AM), Linear AMS has announced the addition of copper to the growing list of chemistries available to its customers.
"There is a lot of interest in thermal stabilization projects for copper components due to copper's excellent heat transfer properties and electrical conductivity," said Paul Breeding, Director of Engineering/Additive at Linear. "Tie in all the advantages of metal AM in removing design constraints and expanding part configuration choices compared to conventional milling and turning, and copper becomes a very exciting choice for particular parts."
Industries such as aerospace and automotive are breaking new ground with printing copper components. As recently as 2015, NASA announced its first 3-D printed full-scale copper part, a combustion chamber liner. "We are not trying to just make and test one part," a project leader said. "We are developing a repeatable process that industry can adopt to manufacture engine parts with advanced designs. The ultimate goal is to make building rocket engines more affordable for everyone."
Process development is an ongoing mission that Linear AMS shares as well. "It is a very interesting time in the industrial space with AM," Breeding said. "Team building, participating in standards discussions and improving process controls are just some of our efforts aimed at bettering our engineering and metallurgical understanding of not only copper, but all the materials our customers want."
While AM on Linear's direct metal laser sintering (DMLS) machines is a main process focus, Breeding noted the importance of the company's post-processing capabilities and knowledge. "Copper can reflect laser energy, but simply pumping up the power can also create challenges," he explained. "We are printing test builds to hone in on the process parameters not only with metal AM, but also hot isostatic pressing (HIP) and heat-treating to meet if not exceed part requirements. The challenges with copper as well as other materials have us continually refining the process."
For more information contact:
Linear AMS
12926 Stark Road
Livonia, MI 48150
734-422-6060
sales@linearams.com
www.linearams.com
< back