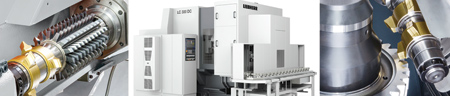
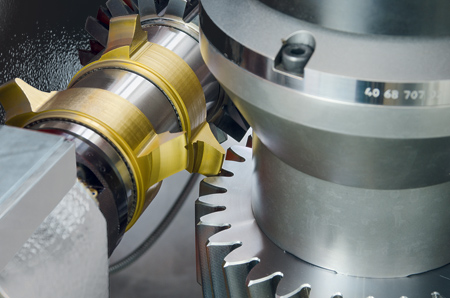
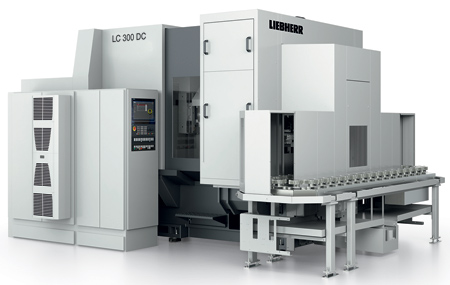
The Liebherr LC 300 DC gear hobbing machine with integrated ChamferCut unit for chamfering parallel to machining
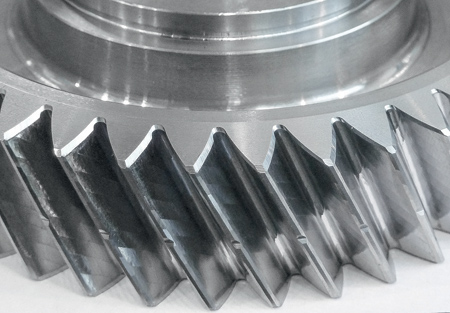
Chamfer form with ChamferCut
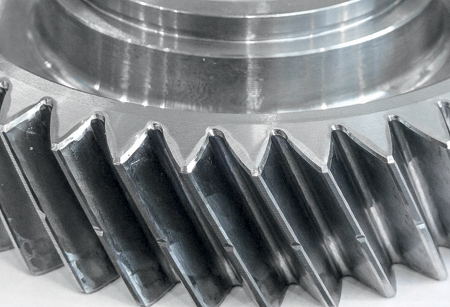
Chamfer form with the traditional chamfering method
"Liebherr-Verzahntechnik GmbH optimized its gear hobbing machine portfolio for the ChamferCut process and offers the customer enhanced technologies with increased cost-efficiency," said a company spokesperson. "Additional machining is now no longer required following chamfering in the Liebherr ChamferCut unit. As a result, chamfering can be performed more precisely, reliably and economically than with competing processes, such as press deburring."
The ChamferCut process enables a complete and even chamfer right down to the tooth root. "There is no need for a second cut, which is often required during the deformation-based deburring process for the removal of build-up material," said the spokesperson. "Since the exact chamfer shape is generated during chamfering, there is no effect on the material structure, unlike with deformation-based processes. An optimal starting point is created for the downstream hard gear finishing, through grinding or in particular honing. The quality of the chamfer defines a new standard, since both very precise chamfer geometry and high chamfer quality and reproducibility are achieved. The tool costs are also lowered, which in turn leads to a low amortization period of the machine."
The advantages for the customer during chamfering include fast retooling and simple adaptation in the case of varying flank modifications, in addition to user-friendly software. Simple adjustments or corrections are also possible via the CNC axes. In general, dry and wet machining is possible with the optimized machines. The machine tools are flexibly automated - for instance, via a plastic chain conveyor or a palletizing cell. The automatic loading is affected by the flexible ringloader principle. Alternatively, the loading can also be done using a robot or gantry.
The following machine types are equipped with the integrated ChamferCut unit:
- Gear hobbing machine LC 180 DC: The LC 180 DC with integrated ChamferCut unit is a compact gear hobbing machine. This integrated automation solution enables hobbing and simultaneous chamfering of workpieces with a maximum diameter of 180 mm and a module of 3.5 mm.
- Gear hobbing machine LC 300 DC: With the LC 300 DC gear hobbing machine, workpieces with a maximum diameter of 300 mm can be economically produced with high gear cutting quality and precise chamfer quality. Workpieces up to module 6.5 mm can be hobbed and simultaneously chamfered.
- Chamfering machines LD 180 C and LD 300 C: The LD 180 C and LD 300 C are compact stand-alone machines whose main task is the chamfering of gears. They can be integrated easily, quickly and cost-effectively into all existing production/manufacturing lines.
The classic ChamferCut process with the chamfer cutters on the hob arbor can be retrofitted on all existing Liebherr gear hobbing machines with Siemens 840 D control and higher.
For more information contact:
Liebherr Gear Technology, Inc.
1465 Woodland Drive
Saline, MI 48176-1259
734-429-7225
info.lgt@liebherr.com
www.liebherr.us