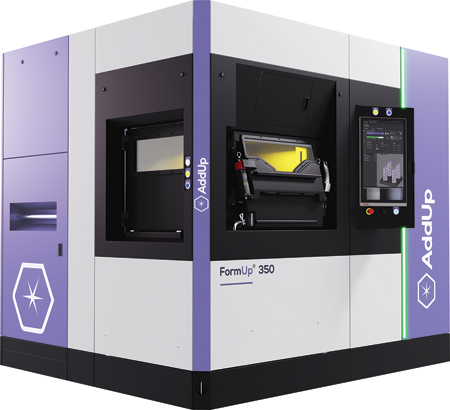
AddUp's FormUp 350 Powder Bed Fusion machine
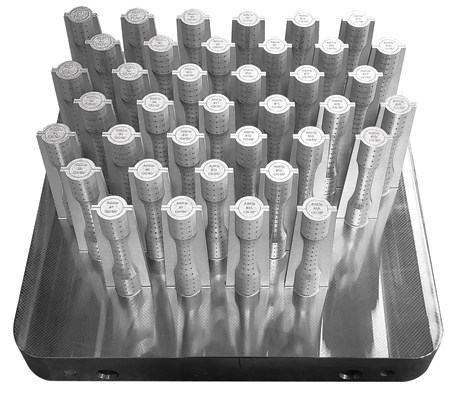
IN-718 fatigue specimens built on AddUp's FormUp 350 Powder Bed Fusion machine.
AddUp, Inc. has joined $1.5M research contract "Development of Manufacturing, Heat Treatment, and Surface Finishing Guidelines to Yield Ready-to-Use IN-718 Additive Manufacturing Components" through the United States Air Force (USAF) and the Small Business Innovation Research (SBIR) program led by REM Surface Engineering (REM).
The USAF is constantly seeking innovative solutions to enhance the readiness and performance of its armament systems. In pursuit of this goal, a project titled "Development of Manufacturing, Heat Treatment, and Surface Finishing Guidelines to Yield Ready-to-Use IN-718 Additive Manufacturing Components" was proposed and awarded. This project, funded through a Direct to Phase II Small Business Innovation Research (SBIR) contract, aims to harness the potential of laser powder bed fusion (LPBF) and surface finishing technologies to produce IN-718 components for legacy armament systems. This endeavor is researching the impact of various heat treatment and printing parameter combinations in association with REM's surface finishing technology on a component's mechanical properties, such as tensile strength and fatigue life. AddUp and Zeda (formerly PrinterPrezz and Vertex Manufacturing) are providing critical support to this project which aims to provide the USAF with set of manufacturing guidelines to maximize the capabilities of LPBF to meet fleet readiness and sustainment goals.
Significance of Fatigue Strength in IN-718 Material for the USAF
Fatigue strength plays a critical role in ensuring the reliability and longevity of components used in demanding applications within the USAF. IN-718, a nickel-based superalloy known for its exceptional mechanical properties and resistance to high temperatures and corrosive environments, has gained significant importance in aerospace and defense industries.
The combination of fine powder and a roller recoater in AddUp's FormUp 350 machine provides a synergistic effect on surface finish improvement, leading to enhanced fatigue properties in IN-718 material. By achieving a more uniform powder layer, reducing surface irregularities and minimizing defects, the fatigue resistance of the printed components is significantly improved. This is particularly crucial in aerospace and defense applications, where fatigue performance is critical for long-term structural integrity and operational reliability.
Collaboration for Fatigue Testing
To ensure the integrity and reliability of the IN-718 AM components, fatigue testing is a crucial step. AddUp, in collaboration with Zeda, will manufacture IN-718 fatigue specimens using LPBF technology with AddUp's FormUp 350. These specimens will be utilized in REM's testing matrix to establish expected material properties of LPBF components with several levels of surface finish and with different manufacturing and heat treatment parameters. Through this collaborative effort, the project seeks to validate the fatigue strength of IN-718 AM components manufactured via AddUp's FormUp 350 LPBF technology.
Impact and Benefits
The Development of Manufacturing, Heat Treatment, and Surface Finishing Guidelines to Yield Ready-to-Use IN-718 Additive Manufacturing Components project represents a significant step forward in advancing the USAF's capabilities and readiness. By leveraging the capabilities of LPBF technology and conducting rigorous fatigue testing, this project strives to enhance the performance, reliability and cost-effectiveness of aerospace and defense components, reducing downtime and ensuring mission-critical operations can proceed smoothly.
AddUp, a joint venture created by Michelin and Fives, is a global metal additive manufacturing OEM offering multitechnology production systems, including the FormUp range of open-architecture Powder Bed Fusion (PBF) machines, as well as the BeAM Modulo and Magic lines of industrial Directed Energy Deposition (DED) machines. The combination of these processes allows AddUp customers the flexibility to choose the technology best suited for their specific application while also offering the ability to meet technical challenges, such as manufacturing parts combining these complementary technologies.
AddUp's FormUp 350 PBF machine is modular and scalable to provide the highest productivity while ensuring user safety. The DED machines are designed for industrial production and equipped with in-house designed and developed nozzles to provide maximum precision and high productivity. To provide customers with a true Industry 4.0 solution, AddUp also provides a complete monitoring solution providing quality assurances after each and every build.
In addition to machine design and manufacturing, the AddUp group also offers part production, POC production, metal AM consulting services, AM training and design for AM.
For more information contact:
AddUp
5101 Creek Road
Cincinnati, OH 45242
513-745-4510
contact.usa@addupsolutions.com
www.addupsolutions.com
Zeda, Inc.
47929 Fremont Blvd.
Fremont, CA 94538
www.z8a.com
REM Surface Engineering
325 West Queen St.
Southington, CT 06489
860-621-6755
www.remchem.com