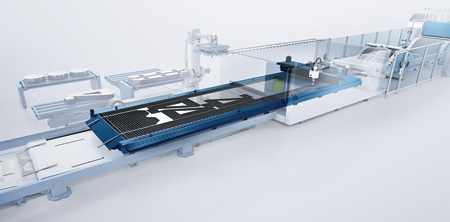
A new flexible laser blanking solution from TRUMPF, the TruLaser 8000 Coil Edition processes coiled sheet metal and can be operated completely automatically.
At FABTECH 2023 (booth A2104), TRUMPF will showcase the latest advancements in precision sheet metal fabrication and applications. A highlight this year is the TruLaser 8000 Coil Edition, a new laser blanking solution TRUMPF is launching in the North American market. The TruLaser 8000 Coil Edition can process up to 25 metric tons of coiled sheet metal from start to finish without any human intervention. It is suited for companies interested in flexible, high-volume solutions for sheet metal fabrication, including automotive suppliers and automakers, electrical cabinet manufacturers, elevator producers and HVAC manufacturers, the company reported.
"The TruLaser 8000 Coil Edition is another solution from TRUMPF that helps North American customers join the drive toward greater sustainability in manufacturing while simultaneously boosting efficiency," said Salay Quaranta, TRUMPF Inc. Head of TruLaser 2D. "Compared to conventional laser cutting machines, this set-up allows companies with high volume manufacturing to save up to 1,700 metric tons of steel a year, which can equate to saving approximately 4,000 metric tons of CO2 and reducing material costs."
Quaranta continued, "TRUMPF's new laser blanking system helps companies enjoy the benefits of laser processing even in high-volume production environments. Volume manufacturers often use die presses for blanking operations, but that means they need to adjust or even replace the tool whenever they make the slightest modification to their components, ultimately costing time and money. Many industries are seeing significant reductions in the scale of individual production runs, which makes modifications even more costly and time intensive. The laser allows users to carry out these modifications without requiring a new tool, so it is much easier, faster, cheaper and more flexible."
The TruLaser 8000 Coil Edition has already been successfully implemented by customers in Europe. In one example, TRUMPF's laser blanking system is used to produce high-strength aluminum structural components for vehicle-body manufacturing. Early adopters of the technology have noted production benefits due to the laser blanking system's high flexibility and quality. They also highlight that the system requires fewer tools than conventional blanking presses.
"Coil production enables users to achieve more efficient nesting of parts," said a company spokesperson. "Conventional sheets are limited by their four outer edges, which often makes it difficult for production workers to make full use of the entire sheet. Unused sections of the sheet either must be discarded as scrap or melted down. A coil solves this problem by allowing users to nest an almost endless number of parts on the sheet, which reduces material consumption by around 15%. Compared to conventional blanking presses, the new system also offers a significant reduction in construction and logistics costs. The TruLaser 8000 Coil Edition makes production more profitable by eliminating tooling costs, optimizing material use, reducing assembly costs and boosting flexibility in the production environment."
The spokesperson continued, "Compared to conventional 2D laser machines, material flow is different and leads to lower cycle times and new automation opportunities in high-volume production series. The system is designed for thin sheet processing, can handle sheet thicknesses of up to 0.25 inches, and can be flexibly adapted to any contours."
The production system is fully automated. An innovative system for transporting sheet metal during cutting keeps the material moving quickly through the whole process. The system also incorporates a TruLaser 3040 with TruDisk 8001. These features include Smart Collision Prevention, which prevents cut parts from tilting and damaging the laser cutting head. The system includes technologies such as EdgeLine Bevel to enable chamfering, and Smart Rerun to save uptime while cutting with reentry techniques.
For more information contact:
TRUMPF Inc.
Farmington Industrial Park
Farmington, CT 06032
860-255-6000
info@us.trumpf.com
www.us.trumpf.com
FABTECH Booth A2104