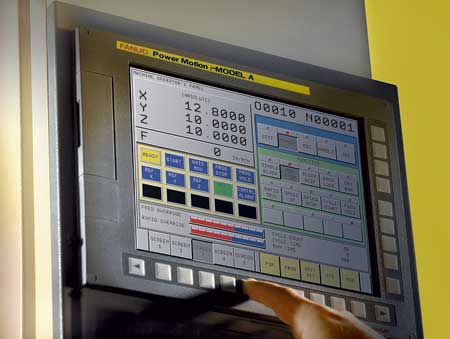
A solution for motion control challenges is the new FANUC Power Motion i-MODEL A introduced at FANUC's recent Open House Show at its headquarters at the base of Mt. Fuji in Japan. It is suited for a wide range of multi-axis and multi-path functions for motion control applications.
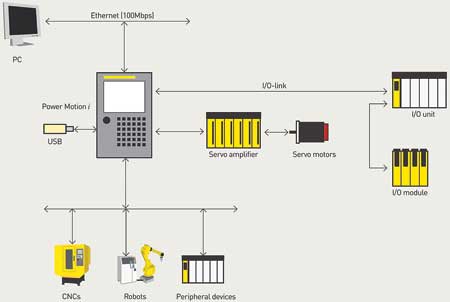
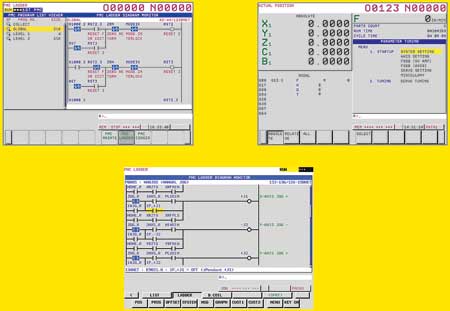
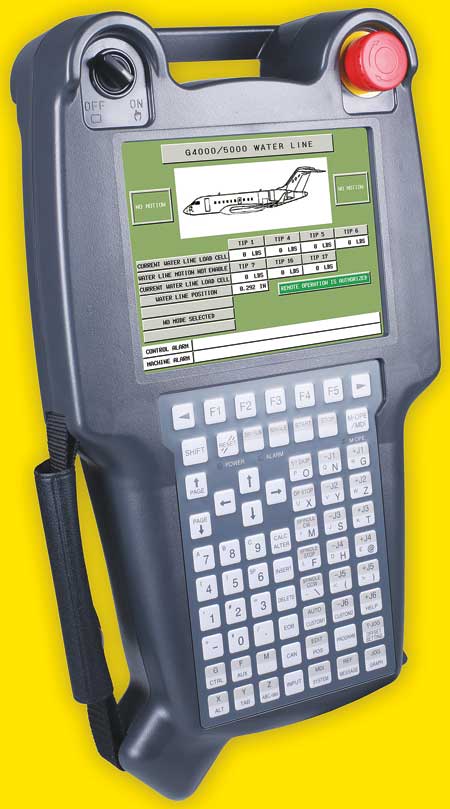
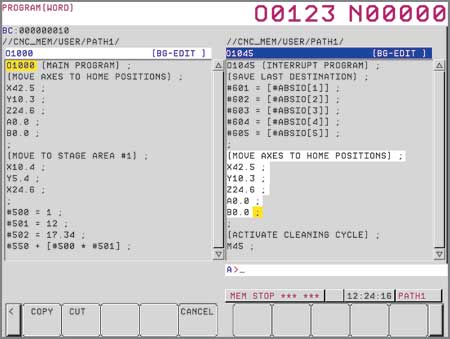
Today's manufacturing is incorporating servo motion in a wide range of new areas beyond traditional CNC manufacturing to increase flexibility and productivity. Applications include non-traditional material processing, winding machines, wire saws, die cushions, wing riveting machines, polishing machines, presses, multi-axis positioning systems and a wide range of material handling systems such as gantry loaders and large robotic table positioning systems.
Many of the integrators contracted to develop non-machine tool motion applications immediately reach inside their traditional toolkit and start designing a programmable logic control (PLC) solution, creating custom operator interfaces (OI), adding racks of motion control boards, input/output cards and a large quantity of custom application code to stitch the pieces together.
Over the life cycle of the application, manufacturers find themselves reliant on that specific integrator and sometimes the specific engineer that designed the application. Unless personnel are already familiar with the individual hardware and software components of the system, maintenance can be challenging.
For these emerging applications, an integrated motion controller is often a more robust and cost effective solution. It allows integration of operator interfaces, motion, programmable logic and input/output devices into a single package. Most of the application code is provided, embedded in the integrated motion controller, eliminating the costly development and support of custom code.
The whole system is backed by a single source and supported by a global service network that is experienced in motion applications. For machining-centric users, much of the technology will be familiar to maintenance departments.
Elements of a Motion Application
Typical motion application architecture includes several key components. In a PLC-based solution these components may be manufactured by multiple vendors, which complicates sourcing, interconnecting wiring, application code and maintenance support. With an integrated motion controller, all the components are manufactured from a single vendor, simplifying sourcing and product support. An integrated motion controller significantly reduces both the interconnecting wiring and custom code development.
Operator Interface
The operator interface (OI) is often the primary focal point to interact with the application. At minimum, there typically is at least one screen that provides a way to start and stop the application. In practice, several screens are required for:
- Program/recipe entry and editing
- Parameters to set application and system variables
- Maintenance
- Axes position display
- Error recovery (for when things do not go as planned)
- Custom application screens to simplify operator actions.
In a PLC based solution, all of these screens require coding that adds up to hundreds of hours of custom engineering. The integrator may have libraries of similar code that they can repurpose at a fee, but the customization can still be significant.
Most of these functions and many more are standard in motion controller applications with an integrated operator interface. It is likely that the application can be completed using the standard screens - saving tens of thousands of dollars in custom development expenses. Because these screens are common to numerous applications, field service and maintenance teams do not need to be trained on a custom solution.
Integrated motion controllers offer powerful touch screens and flexible HMI tools to create any custom screens required to simplify the application. Windows-based OIs are also available when it is the preferred development platform or when there is a need to integrate off-the-shelf, third party applications.
For large machines that need multiple displays or for applications that do not need a permanent display, portable IO devices can be connected to the integrated motion controller.
Motion Control
Motion control is the brains of the system that actually controls the movement of the axes in response to an event or the execution of a program/recipe. Motion control manages the path of the axes by controlling the position, speed and current (torque) of the individual axis motors and drives.
When there are just a few axes to move, motion control using a PLC may be achievable in a reasonable amount of development time. Custom application code may load a new position into designated registers and then set a few control bits to get an axis moving. Then the application code may monitor designated register locations and/or control bits to determine if the move was completed correctly.
As the axis count rises, however, this PLC-based motion management can be become unwieldy, especially when axes must interact. PLC motion modules are often designed to control just a few axes, so large axis count applications may require multiple racks of motion modules in addition to the typical CPU/IO rack, increasing the cost of wiring and application code and reducing reliability.
Easy, high-performance axis positioning is at the core of an integrated motion controller, supporting up to 32 axes in a single unit without any interconnecting wiring. The axes can be organized into independent paths, with separate program/recipe streams, that can be synchronized at critical points as required by the application. Connection of the motion controller to the drive system is a single, high-speed, noise immune fiber optic cable. Both rotary and high-speed, high acceleration linear drive systems are available.
Entering axis position programs/recipes in a simple text file using the powerful, integrated editor is all that is required for motion path development. All the application code to command and monitor the axis positioning are standard functions and require no engineering development. Multiple text files can be created for each task or event and adding variables and program flow control increases flexibility. Programs/recipes can be executed proactively based on operator selection or executed in response to an event trigger. Motion controllers can perform precise linear and circular path coordination (interpolation) with multiple axes.
Aside from standard distance positioning, motion controllers support specialized functions such as moving until a threshold is reached based on pressure, torque or speed, multi-axes synchronization, electronic CAM positioning profiles and high-speed response to signals.
Advanced acceleration and deceleration profiles increase performance and the accuracy of the motion path. Setup screens make basic servo system tuning practically automatic. Integrated, graphical screens provide tools to optimize the servo system tuning for critical operations.
PLC/PMC
Most motion applications will include functions that can be achieved using programmable logic control. Both PLC-based motion and the integrated motion controller solutions can easily meet this need.
Both include sufficient memory for large logic programs and register space for simple to complex applications. Whereas the PLC based solution typically starts as a blank canvas, the integrated motion controller solution has defined interfaces between the operator interface, motion control and input/output devices, encouraging commonality between application designs and saving development time.
The motion control solution can support up to five total independent ladders, allowing segmentation based on application needs. Some ladder programs may be secured to protect intellectual property, while others may be left totally open to allow subsequent customization. On large applications, ladders may be dedicated to different areas of the application. The independent ladders can communicate with each other using shared memory locations.
Both systems support a wide range of input/output (IO) technologies, either in a traditional rack configuration or mounted on terminal strips. Both systems support intelligent IO blocks that are ideal for large scale applications, allowing the points to be configured as inputs or outputs as required and minimizing the installation footprint.
PLCs and integrated motion controllers both support a variety of fieldbus for remote IO and simplified device interconnection. However, whereas each PLC manufacturer prefers a particular fieldbus technology, the leading integrated motion controller supports the most fieldbus standards, including Ethernet/IP, DeviceNet PROFIBUSDP, FL-net, Modbus/TCP, CC-Link and IO-Link i.
Interconnecting with other processes, machines and robots is also simplified using Ethernet, Ethernet/FTP, Ethernet/IP and Ethernet/IP Safe protocols, providing robust, high-speed and flexible interconnectivity over a standard Ethernet network.
Authored by: Bill Catalano
Manager, FA Systems
FANUC FA America
For more information contact:
FANUC FA America
1800 Lakewood Boulevard
Hoffman Estates, IL 60192
888-FANUC-US (888-326-8287)
www.fanucfa.com