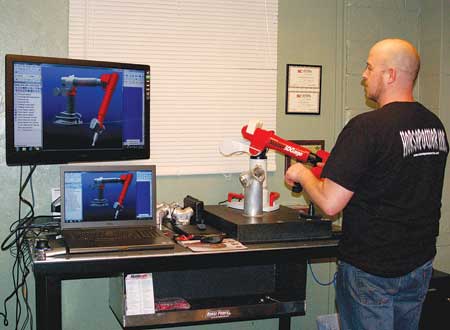
Eric Henderson uses a 3DGage measurement arm to capture measurement data from his hand ported intake manifold and throttle body designs. This data is the basis for reverse engineering the model, which is then used to create 5-axis machining tool paths using Mastercam with Port Expert software from CNC Software.
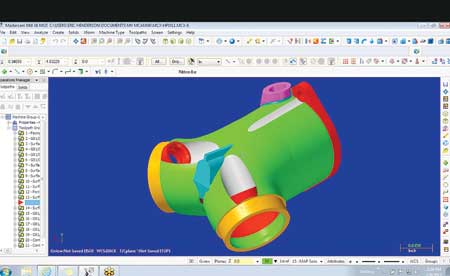
Intake manifold model rotated through multiple angles in Mastercam with Port Expert. The software makes it easy to visualize every internal surface that will require 5-axis machining using a lollipop cutter.
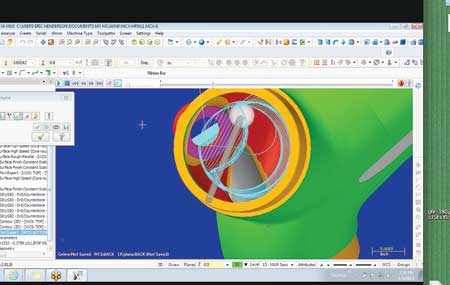
Intake manifold model rotated through multiple angles in Mastercam with Port Expert. The software makes it easy to visualize every internal surface that will require 5-axis machining using a lollipop cutter.
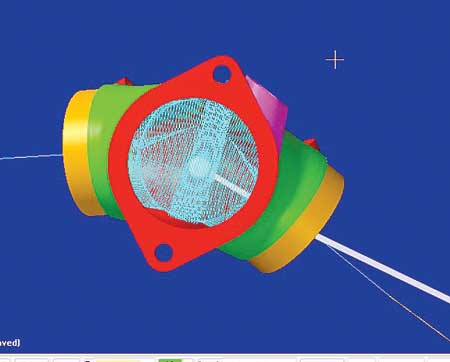
"Where this system really shines is in the transition areas where port cavities intersect," said Henderson. "Mastercam Port Expert automatically generates fine tool movements that smooth out these areas so there are no tool marks or abrupt changes that would disrupt the flow of air and fuel."
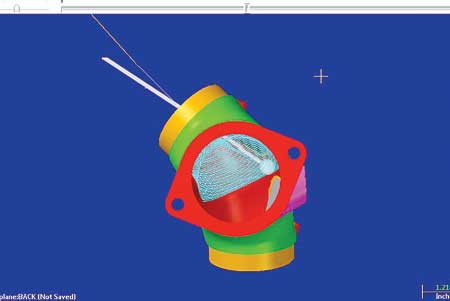
Intake manifold model rotated through multiple angles in Mastercam with Port Expert. The software makes it easy to visualize every internal surface that will require 5-axis machining using a lollipop cutter.
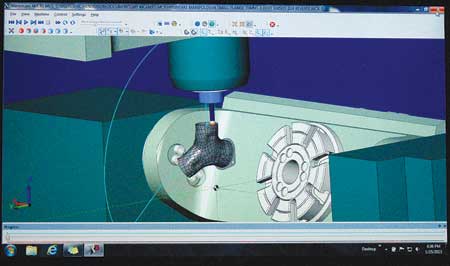
5-axis machine simulation in Mastercam makes it easy to avoid crashing the tool or cutter with part features or fixtures, even though tool movements are highly complex, according to the company.
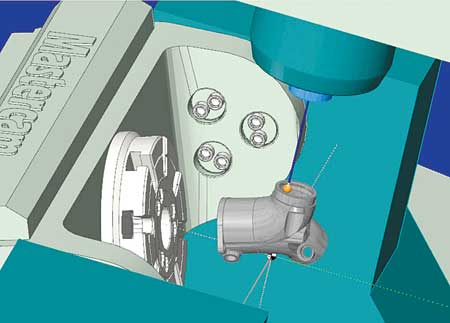
5-axis machine simulation in Mastercam makes it easy to avoid crashing the tool or cutter with part features or fixtures, even though tool movements are highly complex, according to the company.
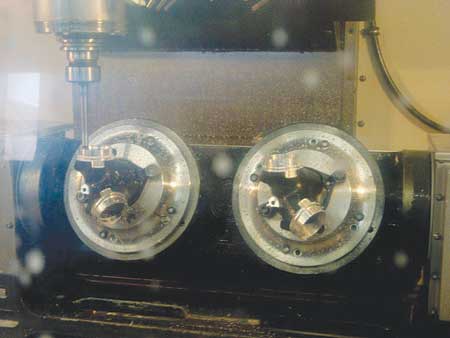
"Mastercam with Port Expert makes it possible to create programs for 5-axis manufacturing of port designs that are perfect duplicates of each other," said a company spokesperson.
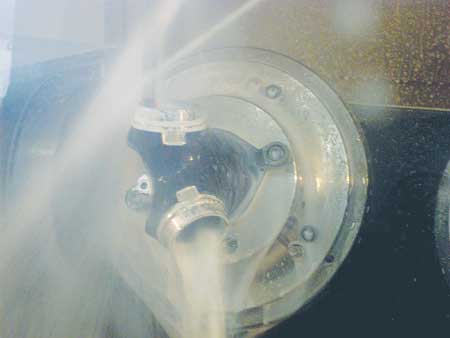
"Mastercam with Port Expert makes it possible to create programs for 5-axis manufacturing of port designs that are perfect duplicates of each other," said a company spokesperson.
Horsepower Inc. designs and manufactures its own line of off-the-shelf and custom engine components for racers, custom bike enthusiasts and third party labelers looking for products that help maximize Harley-Davidson power and fuel efficiency. Owner Mary Jo Light and her crew spend a lot of time reading about, thinking about and talking about all the things that are going on in the motorsports business so they know what is coming up for new engine designs. They are also keeping a sharp eye on the latest developments in CAD/CAM technology so that they can continue to introduce components for the latest Harley engine designs before others in their industry.
"We are all performance driven, with 'Made in the USA' quality as our main objective," said Eric Henderson, whose nominal job description of general manager spans a broad range of activities including the design, testing, engineering and manufacturing of bike engine components. "It was Henderson, Jimmy Light and Gary Salisbury who worked day and night to make Horsepower Inc. the first company to offer a throttle body upgrade for the V-twin industry when Harley Davidson switched from carburetors to EFI," said a company spokesperson. Their product development race was completed in time to install the upgrade on a bike and enter it in the 2003 Horsepower Shootout in Daytona.
Getting into CAM
"The same thing happened with electronic fuel injection," said Mary Jo Light. "As soon as Harley introduced its first EFI bike, we had customers looking to us for better throttle bodies and intake manifolds. We saw the need and manufactured the first big bore throttle body for the Harley. Now there are at least five other manufacturers who have introduced a version of this product."
That was back when the company's 2- and 3-axis mills were programmed manually and all of the porting was done by hand. Light realized at that point that without improving its manufacturing processes, HorsePower could not keep pace with demand for existing products and the pressure to quickly develop new ones. In 2006 HorsePower purchased a seat of Mastercam CAD/CAM software for programming its CNCs. Even then, the company was planning to make a fast but orderly transition into more fully automated design and manufacturing automation. According to the company, Mastercam was chosen because it allowed for seamless, fluid iterations between HorsePower's design, process engineering and manufacturing operations within the software. Mastercam also had numerous modules that could be added over time so the company only had to pay for what it needed at the moment.
Moving into 5-Axis
By 2008, a great deal of progress had been made. "When Harley came out with a drive by wire version throttle for their touring models, it had been in cars forever, so we knew it was coming," said Henderson. "Without the ability to do reverse engineering and make a part similar to their part, we would have been stopped in our tracks in 2008. But because we kept up on technology and software, we were able to do it before anyone else did."
At this point HorsePower added a 5-axis machine, which it was programming in Mastercam's Multiaxis software. The major benefit of 5-axis machining was the time savings and quality improvements due to minimizing the number of set-ups required to make a part. New head and throttle body designs were manually ported and then sent out to an external vendor to be reverse engineered. This data was brought into Mastercam to create the model. The Multiaxis software allowed Henderson to write 5-axis programs that could partially port these components, but a considerable amount of the porting work still had to be done manually.
Advancing to Expert
HorsePower took a step forward in 2011 with its product development and manufacturing evolution by implementing Mastercam's Port Expert software. This is one of several "Expert" software products developed by CNC Software, Inc. to fully automate complex multi-axis machining operations for specific applications. Henderson had never done reverse engineering, but a team from his Mastercam reseller worked with him to master the basic concepts and the transition was a smooth one.
HorsePower's reverse engineering and porting capabilities incorporate Verisurf Software and a 3DGage measurement arm to capture data from engine components that have been hand ported. Verisurf runs inside of Mastercam, where the model is created and further refinements to the design can be made. The Port Expert software is used to generate full 5-axis toolpaths to port the components on a Haas VMC.
All of the software needed for data capture, model construction and CNC toolpath generation resides within the Mastercam programming environment. Henderson can move seamlessly between various software tools at will without having to be continually closing one program and opening another. According to the company, this saves time and eliminates an enormous amount of frustration as components progress through various stages, based on fit, flow bench and dynamometer testing, until an ideal combination of power and fuel efficiency has been achieved.
"Being able to digitize components in-house eliminates numerous exchanges of files with the digitizing vendor and ensures that Henderson will get exactly the data he needs, in a format most appropriate for creating the particular model," said a company spokesperson. "This gives him a better starting point while subtracting days from the product development cycle. The porting toolpaths created automatically by Port Expert, based on the software's reading of the model's geometry, are very complete and require little fine-tuning. They use the shortest possible lollipop cutter to reach every area of the port with the tool at an angle that will keep it as rigid as possible for smooth cutting. Mastercam's Backplot, Verify and Machine simulation features make it easy to avoid crashing the tool or cutter with part features or fixtures, even though tool movements are highly complex."
"Where this system really shines is in the transition areas where port cavities intersect," said Henderson. "Mastercam Port Expert automatically generates fine tool movements that smooth out these areas so there are no tool marks or abrupt changes that would disrupt the flow of air and fuel."
Once the port design has been reverse engineered, all subsequent porting is done on the 5-axis system. "This saves us about an hour to an hour and a half on each manifold and we generally do 20-30 of these a day," said Henderson. "So every day, the Mastercam Port Expert is saving a man-week's worth of labor while manufacturing manifolds and throttle bodies that are perfectly identical." HorsePower's expert hand porter, Bryan Salisbury, then puts some finishing touches on the units and they are ready to ship.
What Next?
Is HorsePower's race to keep up with Harley over? Not yet. The company has started using 3D printing technology to manufacture first piece prototypes that can be used for fit checking. This shaves additional days from the product development cycle. HorsePower contemplates a time when hand porting of models can be eliminated in favor of models created entirely in CAD. It is also looking at the possibility of moving some of its products from sand to investment castings, making it possible to further minimize hand finishing.
More extensive reliance on CAD for product and investment casting tool design may favor using SolidWorks in conjunction with Mastercam, or Mastercam for SolidWorks for CAD/CAM. This is something the company is now considering. As for manufacturing, HorsePower will soon take delivery of a new 5-axis mill. This one will be equipped with a robot loader, allowing the company to port heads on a lights-out basis. Since HorsePower installed its first seat of Mastercam in 2006 and began a systematic program of upgrading its technology, the company has grown by a factor of three. "HorsePower still beats others to the street with alternative port designs for new Harley models and continues to offer the broadest range of port configurations for every Harley model year," said Henderson. "If we do not do it, one of our competitors will."
For more information contact:
Michelle Nemeth
CNC Software, Inc.
671 Old Post Road
Tolland, CT 06084
860-875-5006
info@mastercam.com
www.mastercam.com