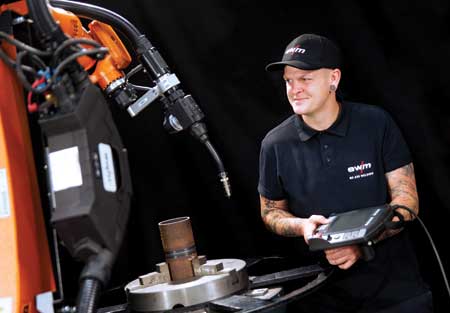
EWM React offers greater control and process reliability for automated MIG/MAG welding.

EWM has developed a robot torch with a dynamic motor specifically for EWM React. It pushes the wire towards the workpiece at a rapid rate and actively pulls it back again.
With EWM React, EWM is launching a new welding process. Using active wire movement, EWM's MIG/MAG welding process provides maximum control during automated welding. With this process, the full-range supplier of welding technology has maximized process stability. According to the company, users achieve up to 100% faster welding speeds and significantly higher quality results compared to conventional short arc processes.
"When you combine a short arc process with digital welding process control and add a highly dynamic torch drive, the result is EWM React," said a company spokesperson.
This solution consists of a Titan XQ R power source with an integrated RCC module and the new React control unit. "React" stands for Reversing actively controlled transfer. This describes a process in which the welding droplet passes into the weld pool in a controlled manner due to both the control of the welding voltage and welding current and the forwards and backwards movement of the wire.
To accomplish this, the wire is first moved towards the weld pool at high speed while the arc torches onto the weld pool and creates a molten droplet. As soon as the wire contacts the molten metal, the droplet passes into the weld pool through a short circuit. The wire is then precisely pulled out of the weld pool by an active and dynamically controlled retraction, and the arc is reignited at very low power. The combination of the quick current reduction offered by the RCC module and the controlled mechanical wire movement allows spatter-free results with high process stability, the company reported.
The active wire movement in the high frequency range is generated using a new EWM robot torch with a dynamic motor. "This breaks through the usual physical limits of the short arc; the droplet transition is completely controlled," said the spokesperson. "Due to the increased process stability, welding speeds twice as high as with a classic short arc can be achieved, while the heat input can be reduced by up to 35%. This reduces distortion to a minimum. EWM thus offers an efficient process for high-quality welding results in the application areas of cladding, joint welding and wire arc additive manufacturing (WAAM)."
For more information contact:
EWM AG
info@ewm-group.com
www.ewm-group.com/en/
Industrial Solutions & Innovation, LLC
4425 Mustang Rd.
Alvin, TX 77511
866-776-8367 / 281-824-0356
www.isi-llc.com