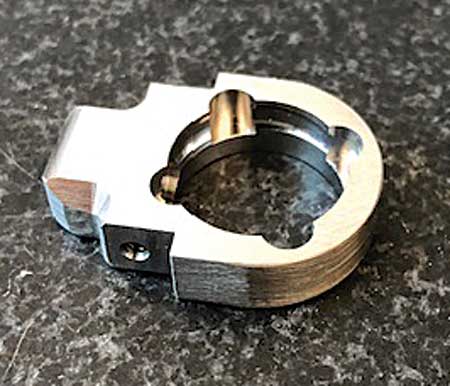
GLTS students produce parts for the NASA HUNCH program. The parts will be used on the International Space Station.
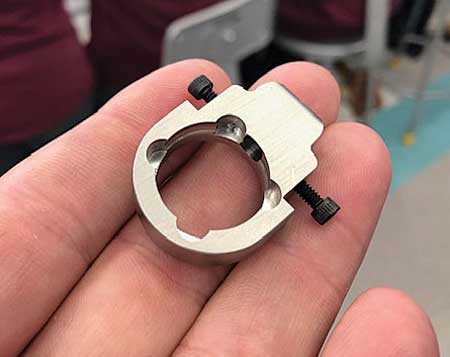
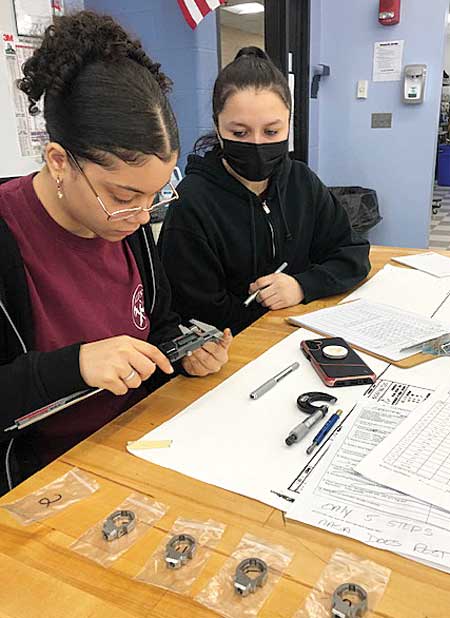
GLTS students inspect the parts they created for the NASA HUNCH program.
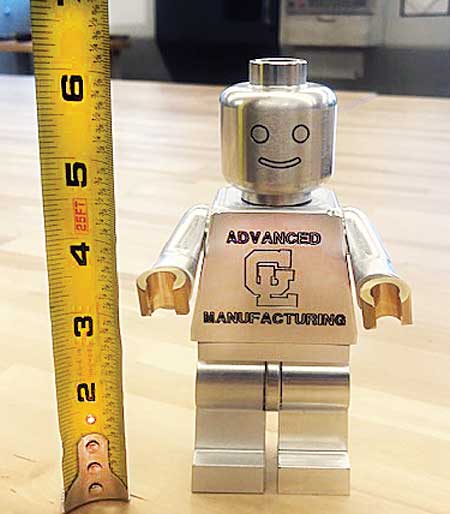
Miniature figurine designed and produced by GLTS students with Mastercam CAD/CAM software.
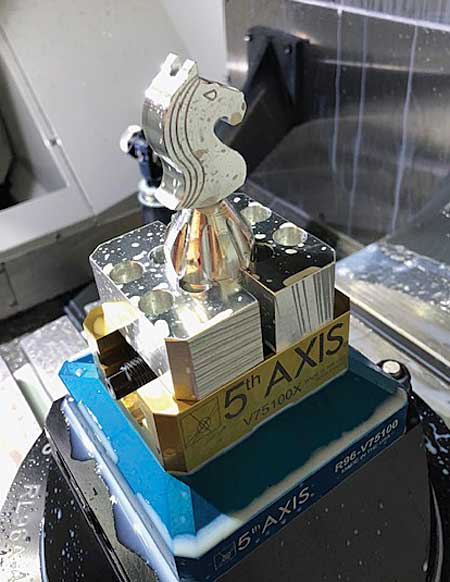
Seniors in the GLTS Advanced Manufacturing Program produced a full chess set and board with Mastercam CAD/CAM software.
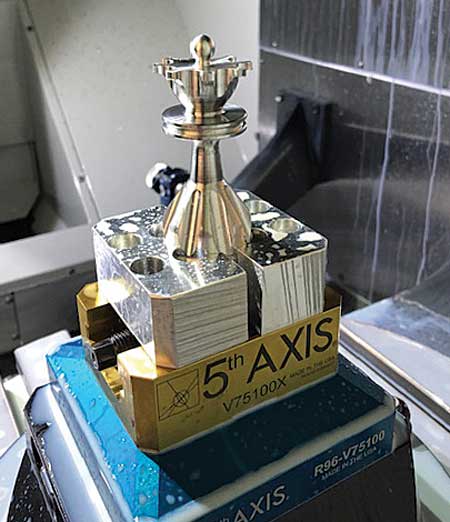
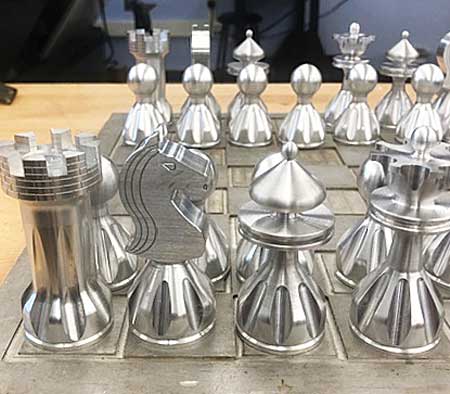
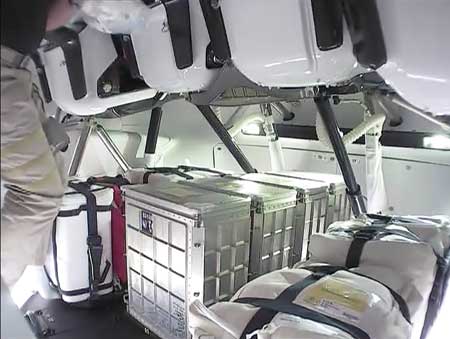
NASA stowage lockers onboard SpaceX's Dragon Endeavor en route to dock with the International Space Station. GLTS student signatures are written in the lower squares of the locker. Photo courtesy of NASA.
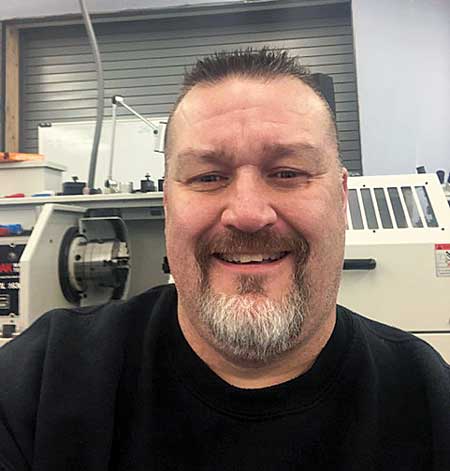
Don Ouellette, Advanced Manufacturing Program senior instructor at GLTS, Lawrence, MA.
As the Advanced Manufacturing Program Senior Instructor and a 1989 graduate of Greater Lawrence Technical School (GLTS), Don Ouellette honors the roots of his alma mater while growing a manufacturing program aimed at the future.
"I was born and raised in Lawrence, MA," Ouellette said of his hometown, located 20 minutes north of Boston. "To be part of the community and come back and teach at the school that I attended certainly gives me a sense of accomplishment."
After graduating from GLTS, Ouellete worked in industry for more than 25 years. At his former place of employment, he was well-versed in Mastercam CAD/CAM software (CNC Software, LLC). "Everything that came through the door was different, and we were heavily involved in 4- and 5-axis programming," he said. "It pushed me to gain even more knowledge of Mastercam."
In 2018, Ouellette made a career move to teaching and brought along his programming and machining knowledge to GLTS. Here, the Norman Martin Advanced Manufacturing Center is filled with new equipment for the 93 high school students enrolled in the program. Enrollment remains steady, said Oulette, due to an extensive equipment inventory, strategic recruitment efforts and creative opportunities for students. The waiting list for Greater Lawrence's Advanced Manufacturing program contains 800 names and 1,700 across all four grades.
"I teach Mastercam-I have been using it for 30 years. It is the only software that we use here in the shop. Anything tangible is created with it," said Ouellette.
GLTS is pushing the limits of space and machinery, Ouellette added. Currently, the school has two separate shops. One is loaded with eight Haas CNC 3-axis mills, 13 ProtoTRAK MH3 mills, six Haas TL-1 lathes and a Prototrak TMZ5 21-tool milling center. Next door, the Advanced Manufacturing shop contains several multi-axis machines, including Haas ST-20Y multi-axis lathes, ST-10 turning centers, a UMC-750 5-axis milling center and a VF-2 with fourth-axis capabilities. A ProtoTRAK 1630 CNC lathe rounds out the equipment inventory. To run the machinery in both of its shops, Greater Lawrence has 40 seats of Mastercam.
GLTS's teachers constantly work on curriculum and try to accommodate different learning styles. One goal is to discover and assign creative projects that pique student interest. The variety of projects and the creativity that goes into them is a huge draw for GLTS's Advanced Manufacturing Technology Program. During the 2023-24 school year, the students had the chance to make parts for a special employer: NASA.
The NASA HUNCH Program empowers students through a project-based learning program. To date, more than 2,575 students across 46 states have participated in the Design & Prototyping HUNCH Program. To produce the complex parts for stowage locks for the International Space Station lockers, GLTS students relied on CAD/CAM software and multi-axis machining. The lock has a complicated undercut inside the part. The part secures the lid of a 30" by 20" locker that holds NASA experiments and projects onboard station interior racks. The locks must meet stringent NASA requirements and be reliable in a zero-gravity environment.
"Last year, we made parts for NASA and they were beautiful, but they were slightly out of tolerance," said Ouellette. "But we received many accolades from NASA representatives who told us that many schools were having difficulties making the part."
Ouellette asked if he and his students could try again, this time using a 5-axis machine. NASA agreed and sent over more materials. GLTS soon received confirmation from NASA that the last round of 10 pieces that the students made were approved for space flight hardware. It is now official: the parts are heading to space.
"Because of this long-term partnership with NASA, our kids receive certification for manufacturing parts that comply with inspection requirements," said Ouelette. "This is something they can put on their resumes and have for the rest of their lives."
After the parts were complete, a NASA representative allowed students to sign a stowage locker cover. When the parts go into space, an astronaut will hold the signed locker cover and take a picture of himself with a view of Earth in the background.
"It is exciting. When parents come to our shop, they see Mastercam and NASA banners all along the walls," said Ouellette. "The NASA project would not have happened without my department and the hard work that we all did. I would like to thank my coworkers Chris Waterworth, Deb Bettencourt and Mark Laderoute who helped make the NASA HUNCH opportunity possible."
When they are not making parts for NASA, GLTS students take on more earthly challenges. Some of the most interesting of those challenges originated right down the hall from their shop. Recently, the head of the school's automotive department asked if Ouellette and his students could design lawn mower engine components from acrylic.
The automotive students presented manufacturing students with a simple lawn mower engine; the top head of the cylinder was removed. The goal was to create an acrylic engine head that would allow a view of the engine's spark plugs. Ouellette and his students reverse engineered the engine head and designed fixtures in Mastercam Design, which simplifies the design of complex parts. The CAD software includes modeling and prep tools. Features include a comprehensive CAD platform, direct modeling, model prep and file import functionality.
"We made a couple of fixtures and drilled a pilot hole," Ouellette said. "We put the spark plug in and did some 3D modeling. I used Scallop, Contour, Drill, Flowline and 3-axis toolpaths to make the 6-inch by 6-inch part. We placed the acrylic piece on top of the motor with the spark plug so students can see inside the motor when the spark plug sparks. We made one, we got it down and made four more."
To showcase all that they have learned during their four years at GLTS, the senior class was challenged with creating a complete chess set. The chess board and 32 pieces were machined from aluminum using multi-axis machining toolpaths on a Haas UMC-750. The purpose of the project was to help students understand why and when to use multi-axis machining strategies. Also, it helped them appreciate the time and money that can be saved by using CAD/CAM software.
Ouellette admitted that after decades of programming experience, he is biased when it comes to CAD/CAM software: "I have been trained for 30 years in Mastercam and have training certificates on all levels. I appreciate the benefits that software provides."
For example, when creating the latch knob for NASA, using Dynamic Mill toolpaths in conjunction with Plane Manager for multi-axis operations resulted in significant savings in machine time, reduced stock scrap rate, fewer operation set-ups and more efficient matching of complex geometry.
Another major advantage of using Mastercam, according to Ouellette, is the ease of the Thread Milling toolpath. The side hole on the latch knob required a 4-40 threaded blind hole that is .125" deep that had to be thread milled in 15-5 PH stainless steel, a hard material. Thread Mill enhancements such as Speed/Feed Override for Lead In/Out, Gradual Lead In/Out and Tool Edge Feed Rate, were made available in Mastercam 2025.
Precision and creativity remain the focus at GLTS. The ideas keep coming, as do students. A recent project that they especially enjoyed was the design and manufacture of a popular building-block-style mini figure. GLTS students created an enlarged version.
"The figure was designed in Mastercam as a 10-piece assembly," said Ouellette. "Using Mastercam, our students designed and customized any feature they wanted."
The aluminum figure stands just over 6" tall. Each piece of the assembly was machined on the lathe and mill. Working as a team, GLTS instructors used Mastercam Solids to create the model and fixturing.
"In industry, we see a lot of Mastercam. That is why I push it," said Ouellette. "Our students get Mastercam. They understand it. Before I know it, they are way ahead of me. I love that because it gives them the chance to keep pushing. I continue to give them additional projects and provide extra assistance to those who need it."
At GLTS, learning does not stop once everyone leaves the classroom or shop floor. Students can access information about programing and machining through the Advanced Manufacturing Program website. The site was designed around student needs for resources, equipment and safety standards. It includes details about all shop operations, so they are always equipped with accurate information.
"From details on speeds and feeds to videos on setting up tooling on the lathe, mill or multi-axis machine, we give our students what they will need to succeed," said Ouellette.
For more information contact:
Greater Lawrence Technical School
57 River Road
Andover, MA 01810
978-686-0194
www.glts.net
CNC Software, Inc.
671 Old Post Road
Tolland, CT 06084
800-228-2877
info@mastercam.com
www.mastercam.com