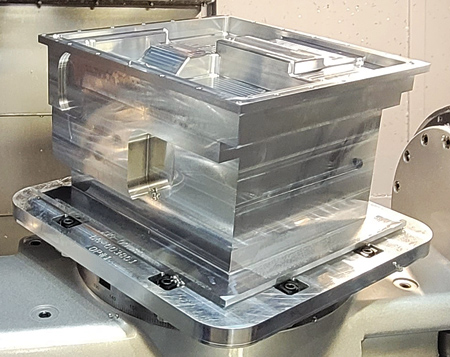
A housing made out of 6061 T6 aluminum, from a 9.5" x 13.88" x 14.88" block with a starting weight of 200 lbs. and a finished machined weight of about 18 lbs. "We could have never made this part or received this order if we did not have 5-axis capabilities," said Costa.
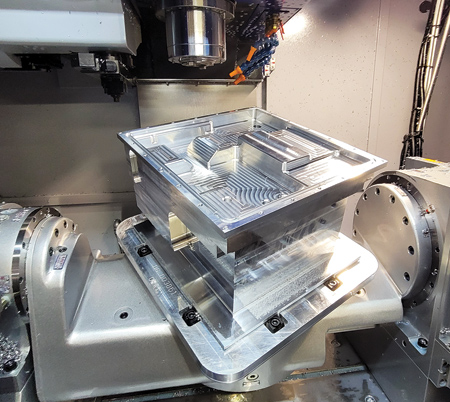
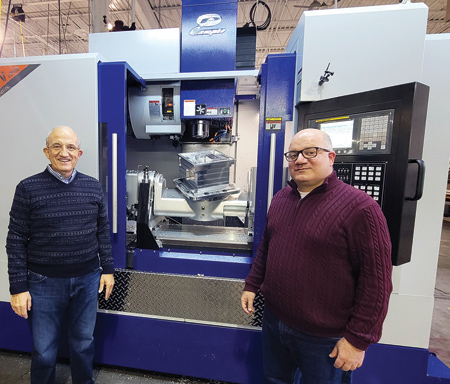
(l-r) Mario Costa Sr., President, and Mario Costa Jr., Executive Vice President, New Age Metal Fabricating
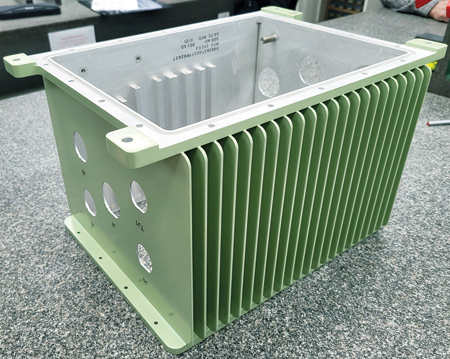
This unit is part of the Armored Multi-Purpose Vehicle (AMPV) Program for the U.S. Army. The components are all machined and then dip brazed at the New Age Precision Manufacturing NY facility. The final finishing is done in-house using the CARC application.
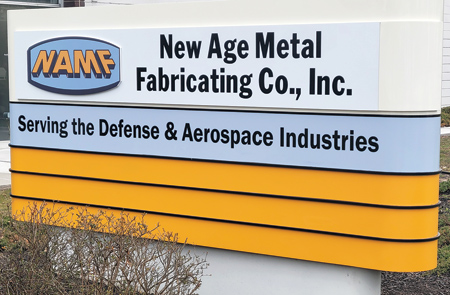
New Age Metal Fabricating is a New Jersey-based defense contractor continually looking for ways to improve its manufacturing processes. Recently the company sought to further expand its capabilities while improving productivity and efficiency. New Age Metal quickly realized that 5-axis capabilities would "allow us to secure new work we could not currently produce, as well as reduce set-up operations and simplify fixturing," according to Mario Costa Jr., Executive Vice President, New Age Metal Fabricating.
The majority of the company's manufactured/machined parts are ruggedized dip-brazed chassis and enclosures used in the defense and aerospace industries. One project is the Programmable Power Supply (PPS) for the Vertical Launch System (VLS) Program. The PPS is made up of 14 machined components that get dip brazed together and partially welded. It measures 26" x 21.5" x 9.5" and weighs just over 80 lbs. when completed. In addition to machining, brazing and welding, New Age Metal also installs specialty hardware and bushings, and also chem films (a chemical conversion coating to protect aluminum from corrosion), masks and paints the unit. "This project really stands out because of its complexity, size and weight; it also requires most of our manufacturing capabilities. It is the largest and heaviest part we braze and one of the largest and heaviest parts we have manufactured," said Costa. The company's work is primarily in 6061 T6 aluminum.
To meet its most recent goals, and after considering many alternatives, the company decided that a Campro U255C and a Campro CPV-1050B with a rotary/trunnion table would be the ideal solution.
According to Costa, "We were able to get a large new contract because of the capabilities the two Campros gave us. Also, we have been able to reduce set-up time as well as run times on existing work. We have moved parts to the Campro that we previously ran on a horizontal machining center and a vertical machining center, which eliminated two operations and 2.5 hours of set-up and significantly reduced total machining time. The reduced handling and set-ups also increased accuracies and virtually eliminated scrap." With 5-axis capabilities, Costa said they can also now take on work with contours and features which otherwise would be impossible to machine with a 3-axis machine.
"Having a machine with 30 in. of Z-axis travel, box ways and still having 1,200 IPM rapid traverse rates and 12,000 RPM gives our company the flexibility it needs for heavy machining as well as high accuracy work for the jobs we run for the aerospace and defense industries," said Costa. "Using the latest FANUC PLUS controls, as well as Marposs part and tool probes, adds to our productivity and efficiencies."
Features and specifications of the Campro CPV-1050B include:
- FANUC Oi PLUS Control
- AI APC Contour Control
- XYZ travels 42" x 20.9" x 30.7"
- Allowable table load: 2,200 lbs.
- Trunnion table: max. workpiece dia. 26.7"; max. workpiece weight 220 lbs.
- CAT 40 BIG PLUS spindle
- 12,000 RPM spindle
- 20 HP (30 min.) high torque spindle motor
- Twin arm 24 tool ATC
- Rigid tapping.
According to Bob Morrison, Managing Director of Campro USA, "Campro has been a leader in 5-axis machining since 2012. We recently introduced our second generation of 5-axis capable machines and continue to work with manufacturers to provide machine tools to assist in making parts more efficiently."
According to Costa, the transition to 5-axis capability has been smooth. "Our other 3-axis machines have FANUC controls, so there has been a very small learning curve as far as the operation of the machine goes," he said.
New Age holds NADCAP and NAVSEA approvals for dip brazing and welding. NAVSEA approval is required for any work being done for the Navy. "Companies such as Lockheed Martin, BAE, Raytheon, Northrup Grumman and Boeing require NADCAP approval for some special processes. Whether working directly or indirectly for these companies, our NADCAP approval automatically qualifies us to perform these special processes on products going to these companies," said Costa.
New Age is a single-source supplier of precision manufacture and dip-brazed products, offering customers complete turn-key solutions to their material purchasing needs.
For more information contact:
New Age Metal Fabricating Co., Inc.
26 Daniel Road W
Fairfield, NJ 07004
973-227-9107
info@namf.com
www.namf.com
New Age Precision Manufacturing Co., Inc.
151 Remington Blvd.
Ronkonkoma, NY 11779
631-471-4000
info@napm.com
Campro USA
5 Highland Ave., Suite C
Bethlehem, PA 18017
484-892-6333
www.campro-usa.com