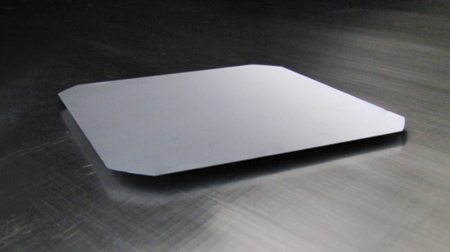
Levitating substrate
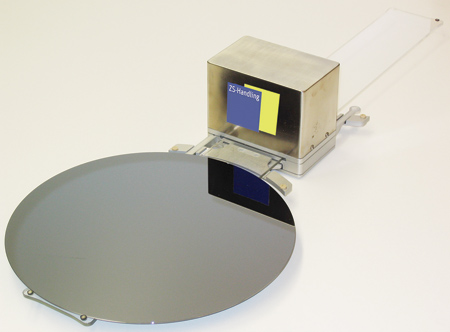
Quartz glass double paddle of ZS-Handling
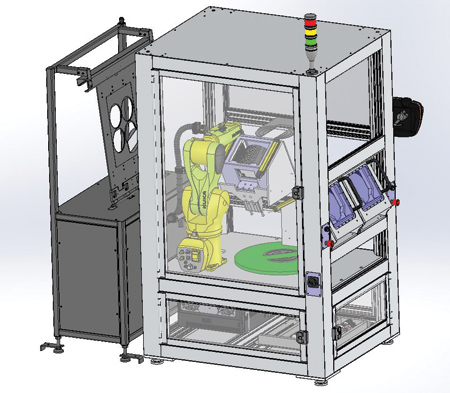
Robot cell
During the manufacturing and further processing of silicon wafers, damages happen from time to time. Besides downtimes, additional cleaning steps and readjustments, higher material and process costs can accrue. The likelihood of broken materials decreases when the handling is more frictionless.
The wafers are also becoming thinner and thinner, making handling even more difficult, since they are more sensitive to damage and also become more flexible and susceptible to sagging.
Conventional handling systems often have problems, for example particle contamination in air bearings caused by the air turbulence of compressed air (e.g. Bernoulli grippers). Other systems without air supply, for example vacuum grippers, can leave traces such as marks or scratches on the substrate during handling. With the help of the patented ultrasonic bearing from ZS-Handling, substrates can float evenly on an air film generated by vibrations and therefore be held without contact during handling. Through a combination of negative pressure and ultrasound, attracting and repulsive forces act simultaneously on the workpiece, thus keeping it at a distance even when gripping from above. Bows and warpage can be compensated to a certain degree.
How Ultrasonic Technology Works
The ultrasonic movement of the sonotrode creates a supporting gas film (air or process gas) between the sonotrode surface and the substrate. The substrate floats on the resulting gas film at distances of 10 - 150 µm, depending on the application. In special cases, higher hovering heights can also be achieved. By using buoyancy forces due to vacuum, handling from above is also possible. In this way, any mechanical surface contact is avoided.
The physics of the ultrasonic bearing results from the flow dynamics and not from acoustic principles. The gas pressure in the gap between the workpiece and the vibrating surface increases due to the cyclic compression and decompression of the thin gas film. It is therefore necessary to realize a uniform oscillation pattern in order to generate constant floating forces over the entire sonotrode. The vibrations are not transmitted into the substrates and do not lead to any impairment of the substrate material.
Advantages
With the repulsive forces of the ultrasonic bearing, the substrate can be moved without any friction even at very high speeds. In combination with vacuum, attractive forces can be applied simultaneously, which allows handling from above. In addition, flexible materials can be "smoothed" without contact by this technique, i.e., they can be kept in an even, centered position.
The force profile of ZS-Handling handling systems is similar to that of a conventional air bearing, but no compressed air supply is required. This means, for example, that in a clean room environment the laminar air flow-unlike with Bernoulli grippers-is not disturbed by high flow velocities and no particles can penetrate through external air or via pipes. Also, in new production lines the costs for the compressed air supply can be saved.
By avoiding surface contact and without dynamic turbulence in the ambient gas, no damage, micro-scratches, micro-cracks or contamination can damage the substrate. Handling on machined or coated surfaces is possible without contact, allowing more degrees of freedom in process and machine design. During handling, a high level of flatness of the substrate is achieved as well.
The systems can be used in all atmospheric processes and in up to 20% partial vacuum processes. This requires fewer resources, such as energy or compressed air, than a standard air bearing. This has a positive effect on the energy and cost balance for the handling systems of ZS-Handling.
In a cleanroom environment of ISO6, silicon wafers that have an IC structure on the topside should be taken out of a stack magazine, fed in a metallization process, and subsequently be placed down again. This should be realized for two different wafer sizes (6" and 8") that have a thinness up to 100 µm and a thicker fringe with a width of 3 mm. The refitting of the system to the appropriate wafer size can take maximum 10 minutes.
The ZS-Handling solution covers the complete robot cell. It includes the wafer handling system "LeviWafer-Gripper" in the double paddle version, which can be combined with any robotic system. The two sides of the paddle have different dimension, so that the two desired sizes can be handled with the same gripper. With the help of the end-effector, the wafers are taken out of an oblique standard cassette without touching the downside. Pins at the edges stop the wafers sideways, so that they do not fall off.
For the following process step, the wafers must be turned and therefore they need to be dropped down on the wheels to reach round.
Afterwards, the wafer gets gripped with the part of the multifunctional paddle that simultaneously uses negative pressure to enable overhead handling of the wafer. Therefore, the wafer can be transported to the prealigner without any contact. There, after the scanning of its code and the inspection, it gets aligned.
Afterwards, with an angular accuracy of +/-0.5° the wafer can be put down into the 2x2 matrix carrier, where the metallization process takes place.
After this process, the carrier gets unloaded contactless and the wafers are sorted back into the cassette. Due to the pins and the flattening, the wafer is kept in center during transport.
The complete process sequence for handling wafers is fully automated. With the help of ultrasonic oscillations, the wafer is held in a flat position on the evenly generated air film, so that scratches or any other contact or force effects are avoided. In addition, the laminar air flow present in the clean room is not affected by turbulence, which prevents contamination by particles. The customer was able to reduce the breakage rate to below 0.08%. In addition, the associated downtimes could be reduced and the process flow optimized.
Authored by ZS-Handling GmbH
For more information contact:
ZS-Handling GmbH
sales@zs-handling.de
www.zs-handling.com