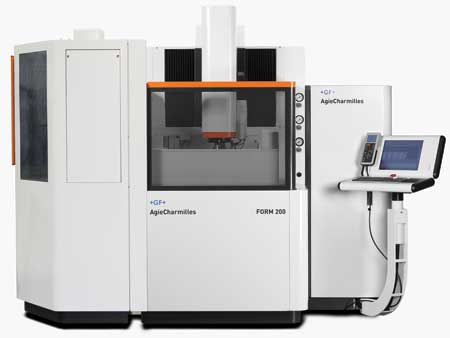
The FORM 200 with rotary tool changer (RTC) offers enhanced flexibility and autonomy.
The GF Machining Solutions FORM 200 die-sinking EDM machine now has a rotary tool changer (RTC) with a large tool changing capacity: from 16 to 160 tools depending of the tooling configuration. The FORM 200 is designed for industrial areas including automotive, home appliances and aerospace where it is essential to machine a high number of electrodes with high quality and efficiency. The compact RTC manages tool changing and the data around those processes.
The FORM 200 features the AC FORM HMI for improved logic, speed and safety. Developed to streamline the moldmaking process, AC FORM HMI is organized on one menu level where all icons are arranged logically and in chronological order of use, and dynamic contextual help is a click away.
FORM 200 features easy set-up, a smart module to enhance machining efficiency and reduce unproductive time, a high-power generator and built-in technology to eliminate electrode wear.
Moreover, the FORM 200 has onboard intelligence designed to make it easy for less experienced machinists to achieve expert results with little training. Elimination of a steep learning curve means novice machinists can operate the FORM 200, and expert machinists can be allocated to more demanding tasks.
GF Machining Solutions' own Intelligent Power Generator (IPG) is at the heart of the FORM 200. "With integrated quality-enhancing and cost-saving intelligence, TECFORM ensures that the EDM process is continuously optimized with each pulse to significantly reduce electrode wear or even reach the finest finishes," said a company spokesperson. "The embedded TECFORM module allows the FORM 200 to quickly and safely achieve the best performance and produce the desired result. Segment-dedicated technology eliminates the need for the operator to adjust the generator's parameters.
"Process control takes a fraction of a second and produces an extremely homogeneous surface finish. In combination, these features yield greater reliability, improved machining efficiency and significantly less unproductive time."
The FORM 200 offers problem-free work insertion via its "Piece Insert" command, allowing urgent commands to be executed in the middle of an current job by recording the current maching situation, inserting the urgent work, then resuming the previous job at the same location where it was interrupted - with no need to modify or add data recording.
Standard on the FORM 200 is GF Machining Solutions' iQ (innovation + Quality) technology that reduces, and in some cases completely eliminates, electrode wear. This is an advantage especially valuable in the aerospace and power generation industries where graphite electrodes often play a central role. GF Machining Solutions' iQ system means reduced set-up time and more machine running time.
The FORM 200's dynamic mechanical concept features a fixed 500 x 400 mm table and a three-sided drop tank for enhanced accessibility to the mold or part. FORM 200 work tank dimensions are 790 x 530 x 350, accommodating pieces up to 530 mm in diameter and programmable workpiece bath level from 100 to 325 mm. FORM 200 XYZ travels are 350 x 250 x 250 mm.
The footprint of the FORM 200 is 1,900 wide x 1,690 long x 2,650 tall (mm), making it an ergonomic workshop addition. By integrating electrical, filtration and dielectric components, developers were able to keep the machine compact while offering improved functions. Ergonomics of the FORM 200 are further improved by its independent console with touchscreen and outstanding remote control with embedded HMI functionalities. The machine features the same contemporary programming functionalities as GF Machining Solutions' FORM 20/30 range and the high-end FORM 2000 HP/VHP and FORM 3000 HP/VHP machines.
For more information contact:
Gisbert Ledvon
GF Machining Solutions
560 Bond St.
Lincolnshire, IL 60069-4224
800-CTC-1EDM
gisbert.ledvon@us.gfac.com
www.gfac.com/us