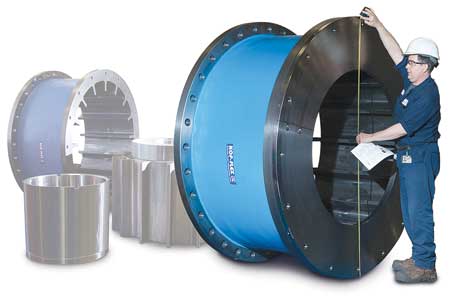
The Kop-Flex MAX-C WB hybrid coupling manages torsional vibration in high-performance drivetrains powered by synchronous motors, variable-frequency drives and diesel engines, or those driving reciprocating machinery or handling shock loads. It combines a maintenance-free, non-lubricated MAX-C resilient coupling half (at left) with a lightweight diaphragm, disc or high-performance gear coupling half, depending on the application.
The Kop-Flex MAX-C WB hybrid coupling is designed for managing torsional vibration in high-performance drivetrains powered by synchronous motors, variable-frequency drives and diesel engines, or those driving reciprocating machinery or handling shock loads.
"Developed by the Kop-Flex unit of Emerson's Power Transmission Solutions business, the design combines a maintenance-free, non-lubricated MAX-C resilient coupling half with a lightweight diaphragm, disc or high-performance gear coupling half, depending on the application," said a company spokesperson. "The hybrid design matches the advantages of a low-cost, lightweight flexible coupling half for the driven shaft, with the vibration-damping of a MAX-C coupling half on the motor end. The maintenance-free MAX-C dampens high drivetrain torque loads, while the overall hybrid design reduces weight, cost and inertia, eliminating the need for oversized and costlier drivetrain components. Various designs of the engineered hybrid coupling are capable of transmitting up to 56,000,000 lb-in (6,383 kN-m) torque. The MAX-C WB is ideal for use in drivetrains for ID/FD fans, torque converters, marine gears, drill rigs, crushers, kiln drives, mill pinions, ship thrusters, centrifugal compressors and feed rolls."
The MAX-C coupling consists of an outer sleeve with a bladed ID, an inner flex hub with bladed OD and resilient drive blocks that fill cavities formed when the sleeve and hub are mated. The wedge block cavity design formed by the blades is filled with incompressible elastomer blocks with a Shore "A" hardness of up to 80, allowing tailoring of the block compound for hardness, chemical resistance and temperature resistance. According to the company, the blocks typically last five years or more and are easily replaced, which makes the coupling like new.
The MAX-C design is also "fail engage": if an elastomer block fails for any reason, the coupling will briefly transmit torque through the metal-to-metal contact of the interlocking blades which would allow the user to immediately power down the equipment in a controlled manner. The MAX-C is designed to withstand wet, gritty and hot environments.
For more information contact:
Emerson Industrial Automation
8000 West Florissant Avenue
P.O. Box 4100
St. Louis, MO 63136
314-553-2000
industrialautomation@emerson.com
www.emersonindustrial.com