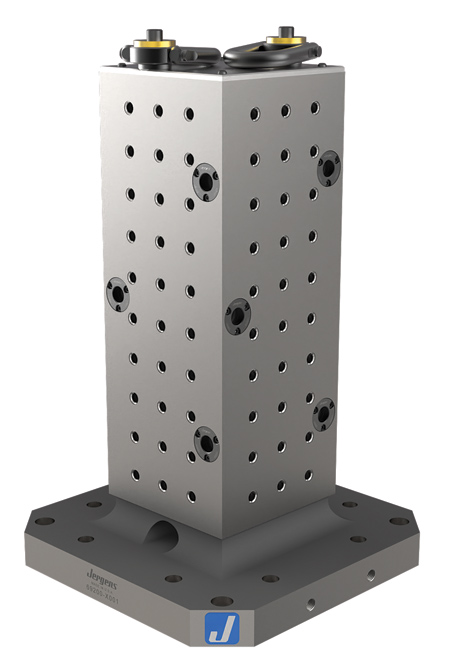
Columns offer standard grid patterns that can accommodate a range of workholding solutions, depending on part size and configuration.
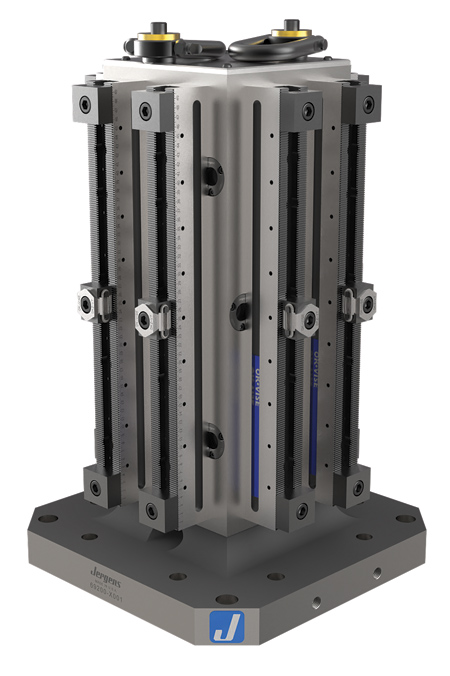
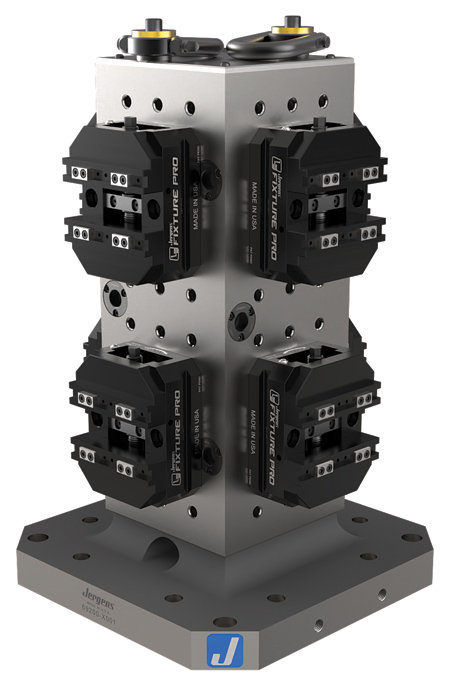
Tooling columns provide maximum productivity when used with quick change workholding systems. Standard or custom solutions are available to meet any application needs.
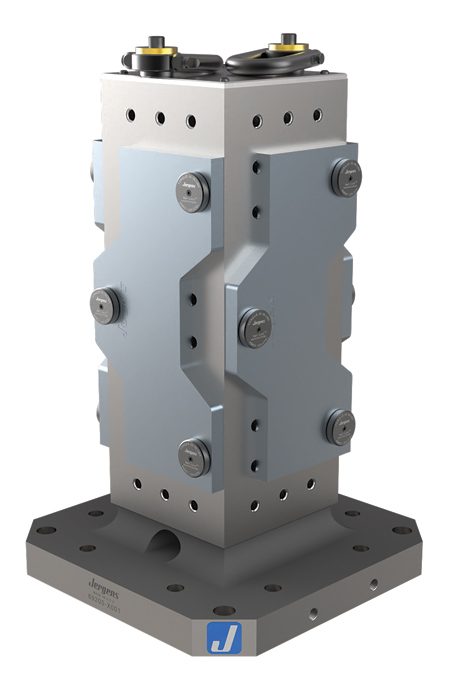
Tooling columns with standard grid patterns provide maximum productivity when used in combination with quick change workholding systems. Standard or custom solutions are available to meet any application needs.
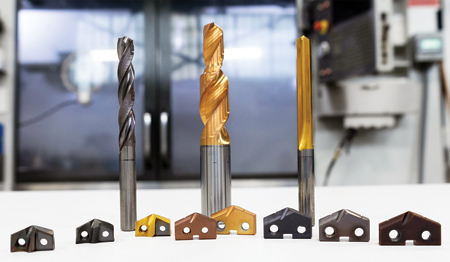
When it comes to broad capability, there are specific machine tools that production units and shops most prefer: 5-axis vertical and horizontal machining centers (VMCs and HMCs). The criterion for choosing between the two can look different depending on a person's role-from ownership to management to purchasing and finance. However, from the shop floor perspective, it is all about making chips.
Getting the most out of these highly sophisticated machines involves a combination of processes, programming, tooling, workholding and human creativity. Set-ups on VMCs and HMCs are very different, too. Workholding on a 5-axis VMC is very straightforward-literally-since the spindle points directly to the table. Setting up an HMC requires quite a bit more thought, however, because the spindle points to...well, nothing, just open space within the machining envelope. So, what does it call for?
Over the years, HMCs have evolved from single station to double, with the use of pallet changers, to pool pallets for multiple set-ups and now to even include hydraulics within the pallet to load and clamp on the machine-and the evolution continues. Today's HMCs have great productivity characteristics, including the ability to continue machining in one location while part change takes place in another. Many feature automatic tool changers and automatic pallet changers, making them well-suited for uninterrupted, unmanned and continuous machining. Configurations with multi-axis spindles also permit true 5-axis machining. And due to gravity, the chips naturally fall away from the parts.
To meet this great potential requires a review of several workholding considerations at the outset.
Angle Plate or Tombstone
First, consider the open-air orientation. All machining on an HMC starts with a workholding solution. This is either going to be an angle plate or tombstone (column) that mounts to the HMC indexing table to provide the positioning and orientation of the workpiece to the spindle. The choice of this fundamental base is dependent upon additional considerations.
The Four Basics
As in all machining applications, all basic requirements must be met: workpieces must be held securely; they must be positioned to allow access to machine all sides (ideally without having to change); operations have to be repeatable (within tolerance); and the set-up has to be operator friendly. This includes the ability to clear chips, load/unload and other ergonomic factors, with the safety of that individual always being first priority.
What is the Current Need?
When preparing for the next parts run, it is best to begin with a Scope of Work (SOW). Include everything, from what you are looking to accomplish now, to opportunities for greater productivity, and how to best support operator skill level.
What is Down the Road?
Savvy engineers are also mindful of future needs. Plan for it now and be ready when the demand arises. This past-the-horizon approach saves time when the need arises for further utilizing technology, such as incorporating robotics and other automation.
Opportunities for Increased Productivity
There are two additional productivity boosters available, depending on the application. The first is the move from an angle plate to a tooling column, which provides the ability to load a greater number of workpieces for any given set-up. This is just a matter of math: a two-sided column essentially doubles that number, three-sided triples and four-sided quadruples. For every incremental increase, there is a corresponding decrease in overall set-up time (or downtime), and conversely, an increase in productivity (or uptime). Connections are standard T-slots or grid patterns.
The second opportunity is the addition of a quick-change system that allows the entire column to be removed, changed and the next one connected and fully loaded-all in a matter of minutes or even seconds. This quick on and off works when repeatability is high and saves operators from having to find zero for every changeover.
Conclusion
Finding the sweet spot for a shop's productivity is very much a human effort and a matter of choosing the best combination of man and machine. In the case of high producers like HMCs, the goal continues to be loading and changing parts faster than the machine can make them.
Authored by Jergens, Inc.
For more information contact:
Jergens, Inc.
15700 S Waterloo Road
Cleveland, OH 44110
877-486-1454 / 216-486-5540
info@jergensinc.com
www.jergensinc.com