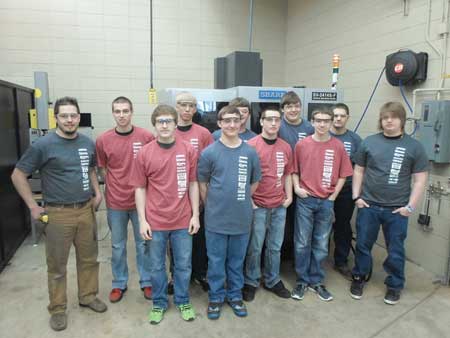
Instructor Jacob Hostettler (left) and a group of Hurley High School students
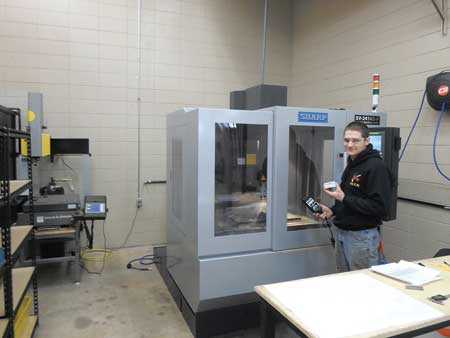
Student working with the SHARP SV-2414S VMC

Metals workshop

Woods workshop
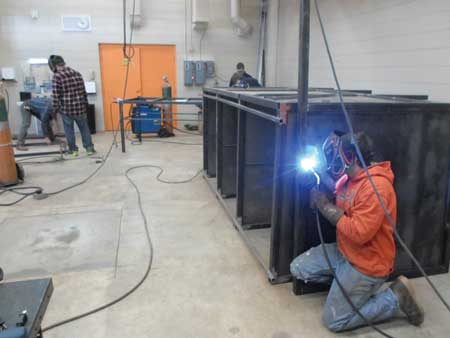
Student welding in the Northwoods Manufacturing metals workshop.
High school students working as welders, fabricators, machinists, etc., might not be a common sight, yet this is exactly what can be found in the Hurley High School manufacturing program in Wisconsin. Operating out of the Hurley High School Technology Education Department is Northwoods Manufacturing, a student-run business that aims to teach students about careers in manufacturing while giving them real-world and hands-on manufacturing experience.
"Northwoods Manufacturing processes all work projects quickly and accurately. Teaching and learning is our main priority," said Jacob Hostettler, Metals Teacher, who along with Roger Peterson, Woods Teacher, spearheads the program.
The students produce all of the products sold by Northwoods Manufacturing, which range from small wooden turned pens, products produced on a CNC router, a variety of metal fabrication jobs, welding projects and machined parts on a CNC machining center.
The program began last year with the support of the Hurley Manufacturing Committee, the Hurley Education Foundation, the Hurley School Board, Bretting Manufacturing and other local industry professionals or businesses. There was concern stemming from a decline in the number of young people entering the manufacturing sector and related fields. This skilled labor shortage prompted them to approach the school with the idea for a technology education program that would serve the needs of the community by giving students training and skills in a trade that regularly has job openings.
The program is a real-world work opportunity for students and it covers a range of fields. Bolstered by partnerships with local industry professionals and businesses, students produce real parts and products that are actually sold. The shop requires a marketing plan, managing of receipts, billing and shipping, which are all handled by students. Students interested have to present resumes and be interviewed to get into the class. Students share in the profits garnered by the shop and are paid at the end of the class.
The class starts with basic aspects of manufacturing and machining. For instance, beginning with small sheet metal projects that gradually build up to low tolerance fixtures for plastic moldmaking. Students get hands-on with the shop's three mills and five lathes as well as manual equipment.
A key addition to the program was the acquisition of a new SHARP mini mill SV-2414S. It was chosen because of its size, which is well suited to a smaller shop, and because of its FANUC controller.
The value of going hands-on with and being taught CNC programming is considerable. By spending one-on-one time with students and through the assistance of volunteers from Ironwood Plastics, a local company that has been very supportive of the program, and using time after school and on weekends, the students are able to become quite proficient. Students just 15 years old are working with the control, indicating parts, calling up the program and setting tool offsets. There are plans for a CAD CAM class to be implemented for basic onsite programming.
The students start by taking on small, one-run parts for iron and plastic, testing fixtures, and then move on to more complex work as they get more proficient with the machine.
The expectation is that some of these students will be motivated to pursue a career in manufacturing and enroll in tech schools after they graduate. Already some have applied and been accepted into the Wisconsin Indianhead Technical College for machining and welding programs. Local companies are hiring on a monthly basis, so there are plenty of opportunities available.
As for the program, the teachers hope it will continue to expand in the future. In terms of equipment, they plan to update their manual mills and lathes, and eventually acquire a new band saw, a new CNC lathe and even a plasma table. Community members are positive about the program and local manufacturers continue to provide considerable support through training opportunities and actual work projects.
For more information contact:
Jacob Hostettler, Instructor
Northwoods Manufacturing
Technology Education Shop
Hurley K-12 School
5503 W Rangeview Dr.
Hurley, WI 54534
715-561-4900 xt 314
hostettler@hurley.k12.wi.us
www.northwoodsmfg.org
Sharp Industries, Inc.
3501 Challenger Street
Torrance, CA 90503
310-370-5990
info@sharp-industries.com
www.sharp-industries.com