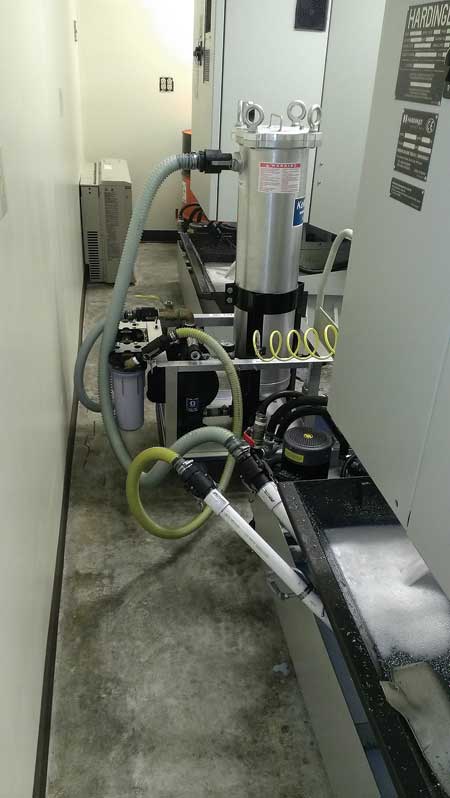
Pump/filter unit cleaning machine sump. (Model shown with optional cartridge filters on pump discharge.)
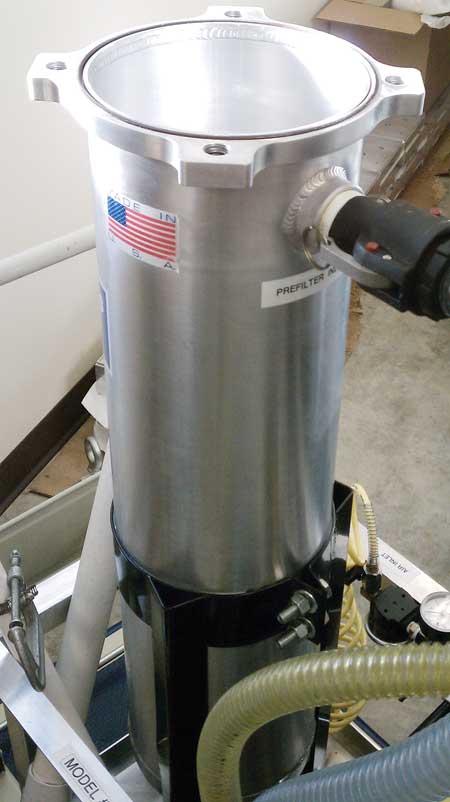
Pump/filter unit open for service.
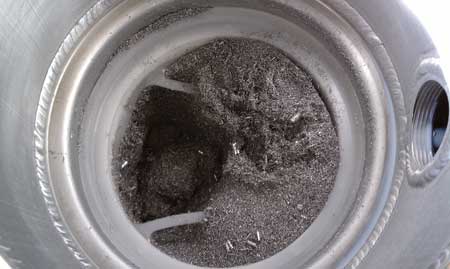
Aluminum fines fill the filter bag.
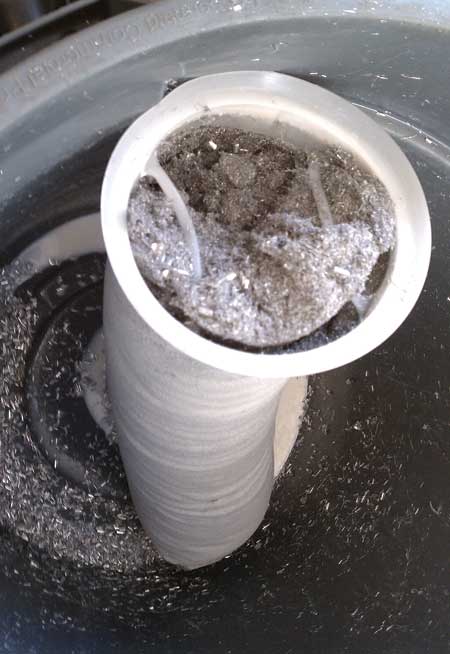
Filter bag full of aluminum fines removed from the filter housing.
Brooks Precision Machining Inc., a rapidly growing New England shop specializing in aluminum sub-assemblies and complex components for a variety of industries, was faced with the problem of buildup of aluminum fines in the machine sumps. The fines buildup was limiting coolant life and required frequent stoppages to clean out the sumps.
Eric Brooks, Operations Manager, assumed responsibility for solving the problem. An inquiry to a local distributor led Eric to Keller Products Inc. Keller Products specializes in filtration and separation solutions designed to keep coolant as clean as possible for as long as possible in the machine sumps. A review of the situation led Keller to recommend the portable pump/filter system Model PFA-1002.
"The PFA-1002 pump/filter unit contains a rugged, high flow rate air-operated diaphragm pump and a high capacity bag filter that removes solids as fine as 1 micron, mounted on a compact cart," said a Keller Products spokesperson. "With a recirculation rate of 20 gallons per minute, the PFA-1002 completely cleans fines and chips from a typical sump in minutes, and then is easily moved to another sump and set up to run simply by connecting a 1/4" compressed air line. With no electricals, the unit is inherently explosion-proof. The self-priming pump pulls the coolant from the sump through a large diameter vacuum hose into the bag filter and continuously pumps the filtered liquid back to the sump at high velocity. The force of the filtered liquid discharge scours the bottom of the sump and keeps chips and fines suspended in the coolant for pickup by the inlet hose. Because the coolant is not drained from the sump during the brief cleaning operation, the machine tool need not be taken offline for solids removal, thus minimizing downtime. Routine maintenance on the pump/filter unit consists of changing or emptying the filter bag when the pumping rate slows. In many applications, particularly when filtering aluminum, the filter bag may be emptied and reused a number of times."
Brooks purchased one PFA-1002 to service all 16 machines in the shop. Brooks reported that with the PFA-1002, the requirement to pump out the machine sumps has been completely eliminated. The reduction in downtime and labor and the corresponding increase in productivity has allowed Brooks to maintain on-time deliveries even during the company's dramatic growth. He said that these improvements were obtained at the relatively low cost of the pump/filter unit. "The PFA-1002 was an inexpensive and convenient solution to difficult and costly production problems," said Brooks.
For more information contact:
Jonathan Strauss, Sales Manager
Keller Products, Inc.
6 Ledgerock Way, Unit #6
Acton, MA 01720
800-352-8422 / 978-264-1911
info@kellerfilters.com
www.kellerfilters.com