
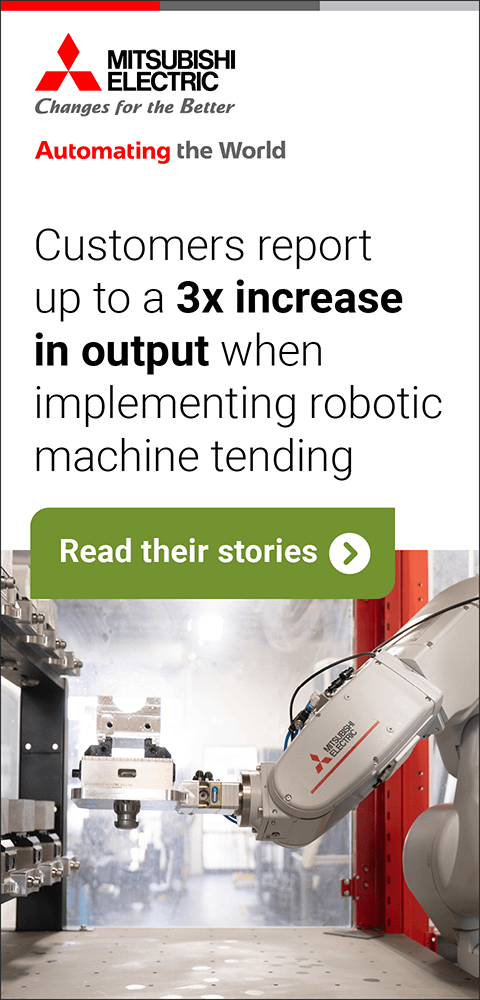
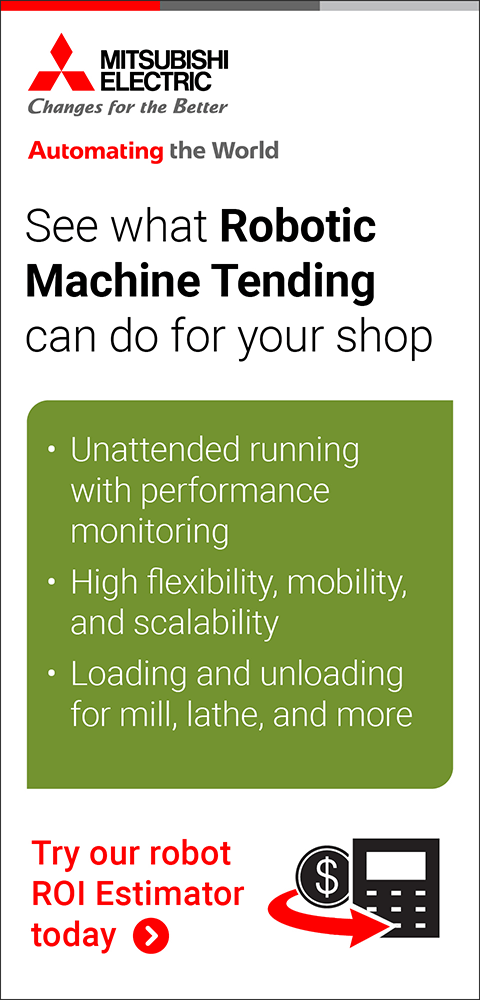
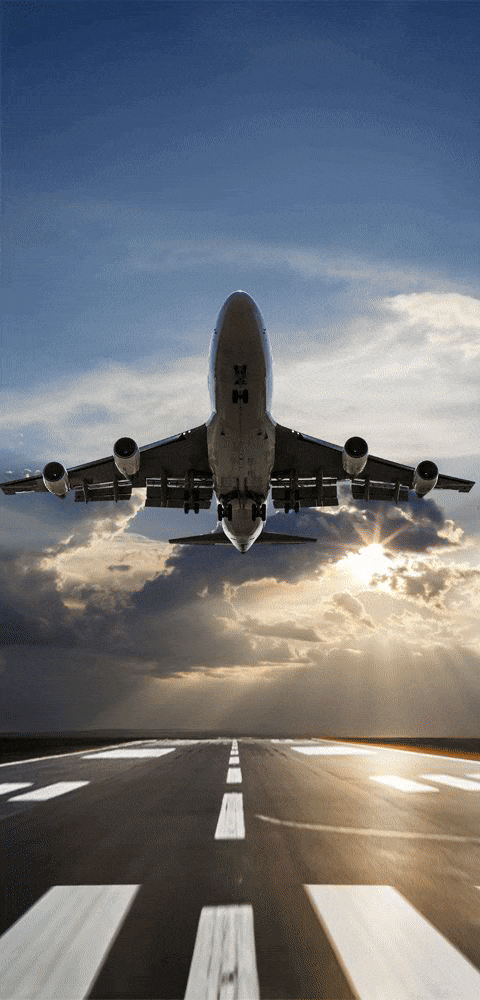
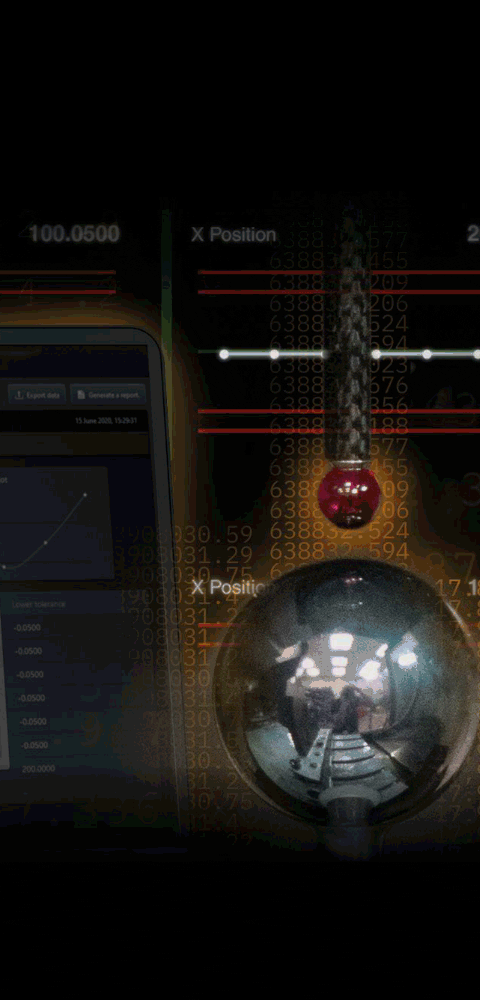
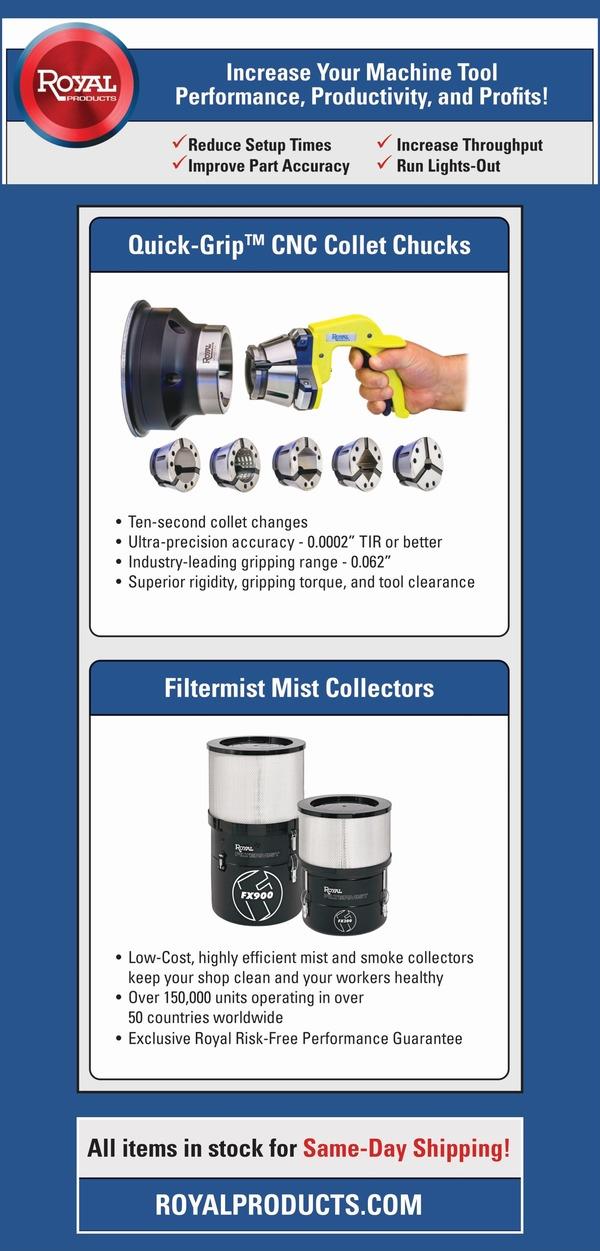
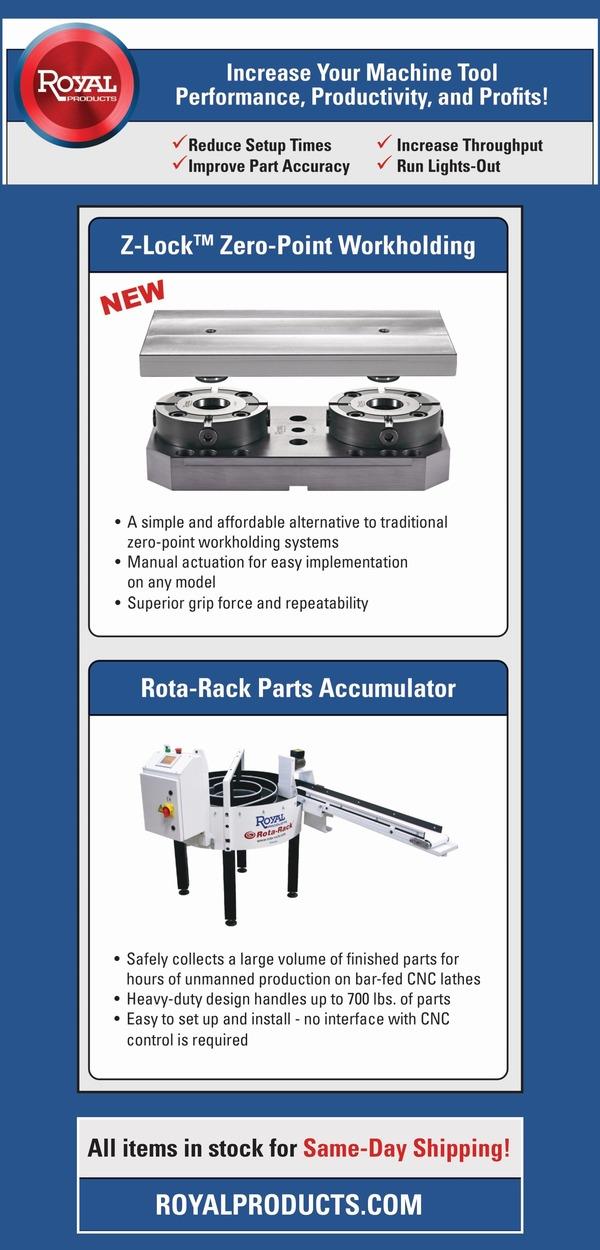

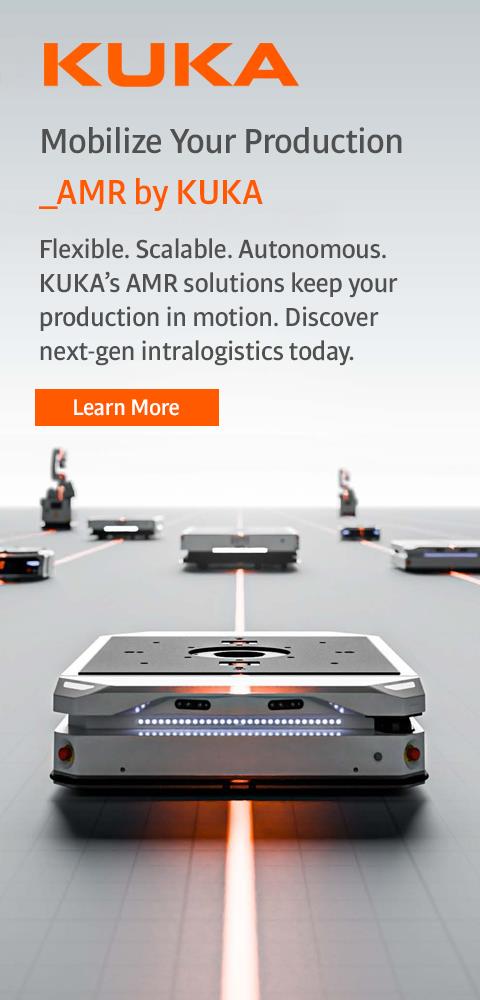
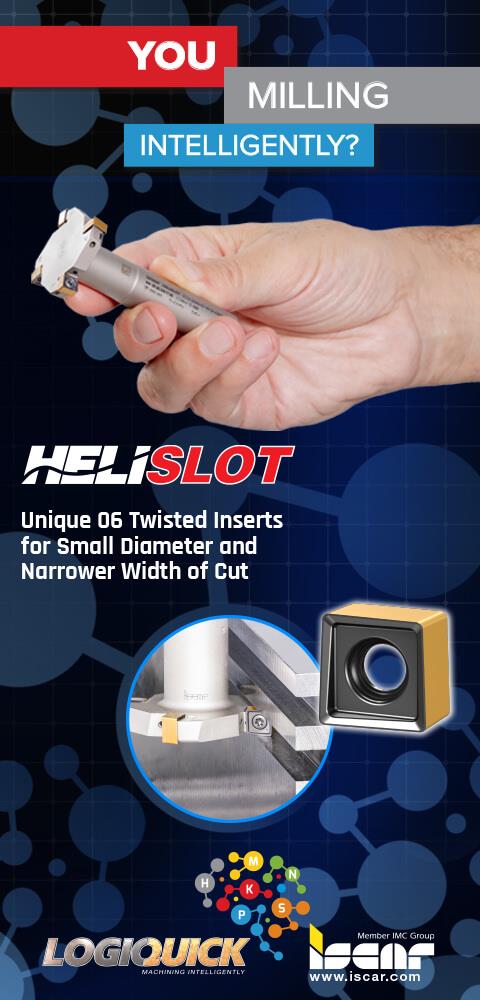
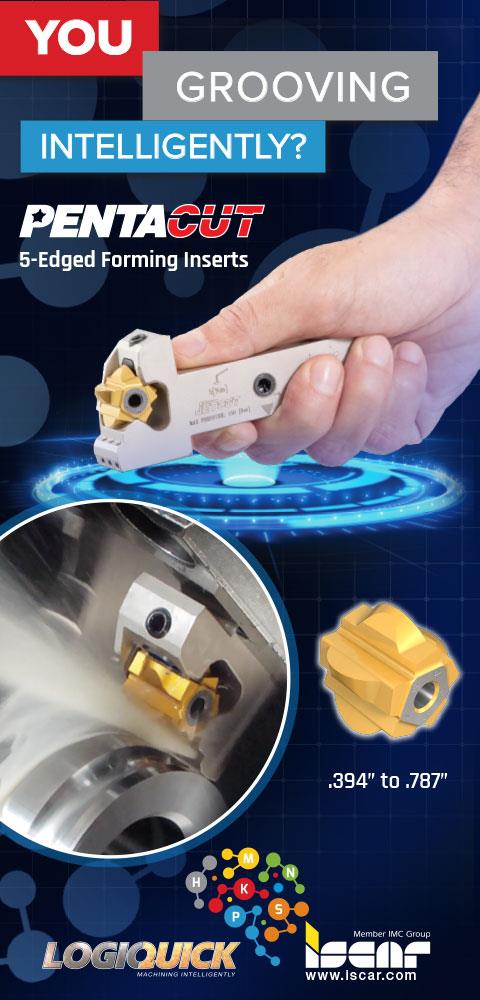
CNC Grinding Solutions
November 1, 2018
Hardinge Inc. has introduced the new Kellenberger 100 and Kellenberger 1000 Universal CNC grinding systems. "These innovative systems improve the precision and productivity for the most demanding range of machining applications. The updated functional and user-friendly design elements on both of these systems allow users to have the control and performance required," said a company spokesperson.
"These systems were made to satisfy the requirements of our customers. We took their feedback, and from the rigid base to the hydrostatic guides on all axis all the way to the new user interface on our controls, we delivered two systems that will meet the most demanding of those requirements. These machines are equipped with OPC UA communication gateways for secure external access, making them well prepared for the future," said Helmut Gaisberger, Global Product Manager Grinding.
Kellenberger 100
The Kellenberger 100 is a high-performance, economical grinder for universal grinding requirements. The machine is the combination of capabilities that are found in the VISTA and VITA machines as well as the Tschudin T25, and the Jones & Shipman Ultramat CNC and Ultragrind 1000. It offers diverse of configuration options for a wide range of grinding operations for customers looking to optimize production costs for the machine.
Features and benefits:
- New compact wheelhead design - The Kellenberger 100 has a new tandem grinding wheelhead in compact and collision free construction with the motor spindle. Reinforced casing for larger grinding wheel diameters for internal grinding. Choice of 10 wheelhead variations for the optimum layout of the machine based on the components to be processed.
- Increased productivity with higher grinding wheel drive power
- Enhanced performance
- New dressing concept due to extended travel of X- and Z-axis
- Greater profile accuracy with redesigned Z-guideways
- High precision B-axis with direct drive and absolute measuring system
- Increased accuracy for noncircular grinding with C-axis with direct drive
- The user-friendly and ergonomic design of the Kellenberger 100 features a new, intuitive operator guidance system on a touchscreen panel. The machines are equipped with the latest FANUC 31i CNC controls with 19" touchscreen. The user interface is available in two different versions: BLUE Solution the intuitive touch programming; and RED Solution, the extended graphic programming.
Kellenberger 1000
"The new Kellenberger 1000 is the next generation of the VARIA universal cylindrical grinding machine that has been the standard in high precision grinding for over 20 years," said a company spokesperson. The Kellenberger 1000 offers advanced technology, design and features for high-precision production of prototypes and small and medium-size series.
Features and benefits:
- Precision and productivity with hydrostatics - The Kellenberger 1000 features the newest generation of hydrostatic guideways for enhanced precision and productivity. "They provide increased damping, stick-slip-free operation, high rigidity and a constant machine temperature, resulting in outstanding surface quality and more reliability without any friction loss and wear," said the spokesperson.
- Enhanced taper, thread, profile and out of round grinding
- Enhanced stability and rigidity with larger workspace - In the Kellenberger 1000, the machine table has been considerably extended, so it allows enhanced, optimal positioning of the grinding wheel and a larger travel distance, ready for a wider variety of machining options and application-specific configurations. With the reinforced machine bed, Kellenberger 1000 can now work with workpieces of up to 300 kg and larger heights of and distances between centers, offering consistently better performance.
- Flexibility with unique machine concept - The Kellenberger 1000 is available with distances between centers of either 1,000 or 1,600 mm, and heights of centers of either 200/250 or 300 mm, as required. Travel on the X-axis and Z-axis has been extended. More than 30 wheelhead variations with external and internal grinding spindles permit an array of machining possibilities, and the right application-specific configuration at all times.
- More operator friendly and reliable with functional machine casing - The increased sheet metal thickness means even more process reliability, allowing larger internal grinding wheel diameter of up to 125 mm.
- Compact and maintenance-friendly elements such as the power supply, electrical cabinet and a central connection point for lubricating coolant, water cooling system and compressed air were all integrated into the casing. The Kellenberger 1000 is known for the compactness of the space it requires for set-up.
- Optimized energy management performance and optimized central cooling system for minimized thermal drift with the result of minor deviation on the workpiece.
For more information contact:
Hardinge Inc.
P.O. Box 1507
Elmira, NY 14902-1507
800-843-8801
info@hardinge.com
www.hardinge.com/product-brand/kellenberger
< back