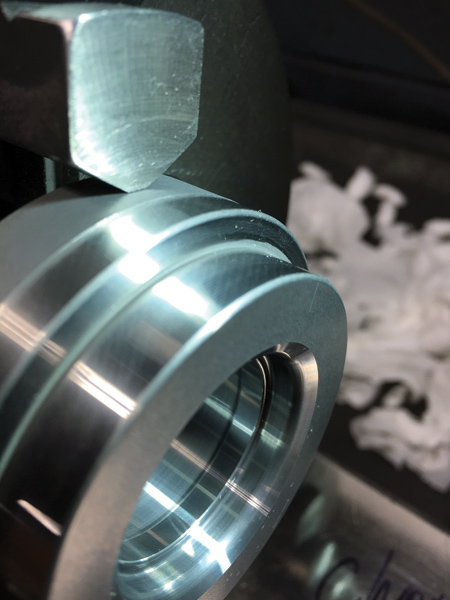
Solid carbide step drawing die illustrating Studer Contour grinding
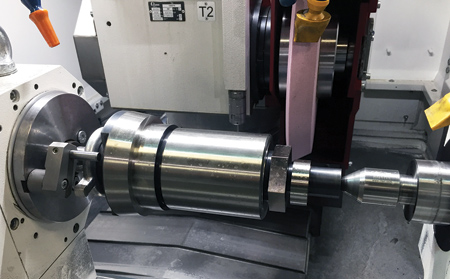
O.D. grinding on centers-straight, shoulder, angular and non-round grinding all on one workpiece
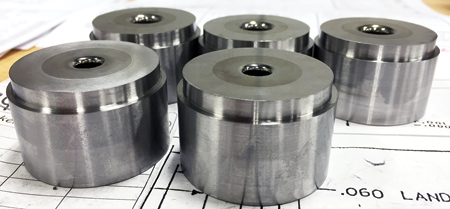
Set of five carbide inserted drawing dies ground complete O.D. and I.D. and contour
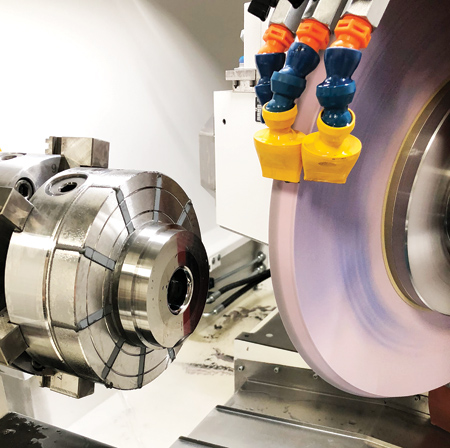
O.D. and step grinding of a hardened steel housing using a 30 angle wheel
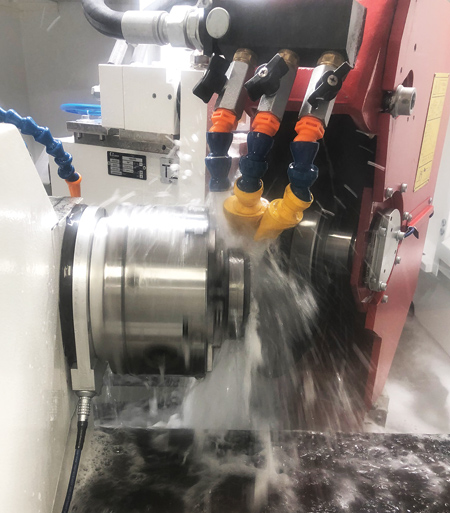
O.D. grinding a hardened steel plug gauge
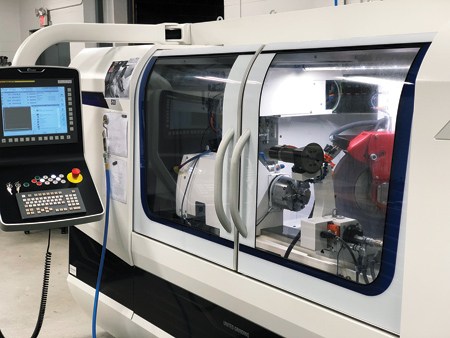
View of the Studer S33 showing the swing down rotary diamond dresser and the control
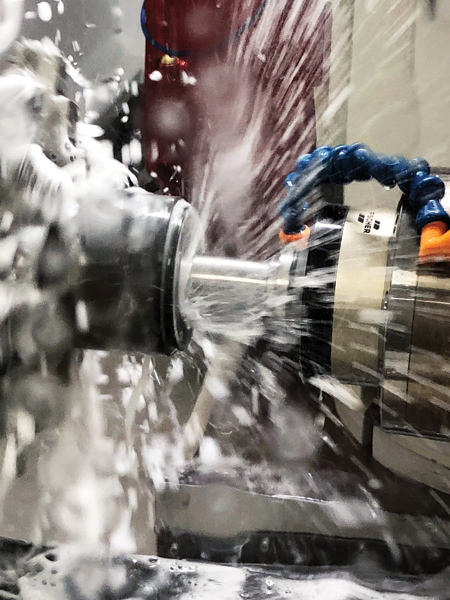
I.D. bore grinding a solid carbide drawing die
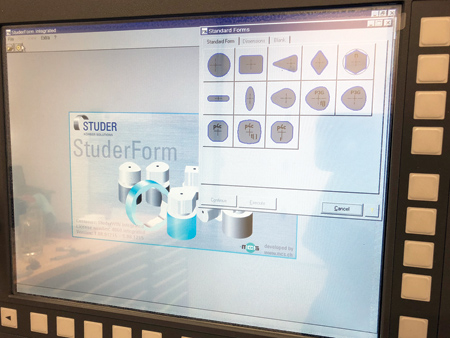
StuderForm integrated screen shot of the standard programmable shapes that the software allows
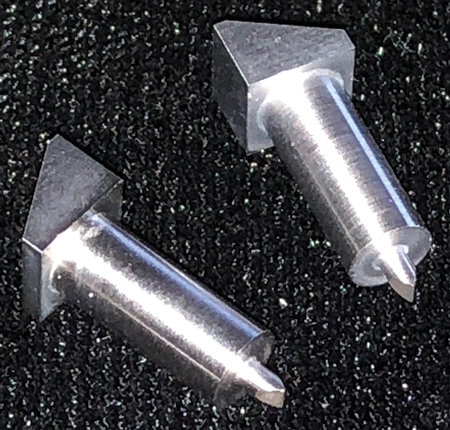
Hardened steel forming punches-non-round grinding as well as standard O.D. and contour grinding
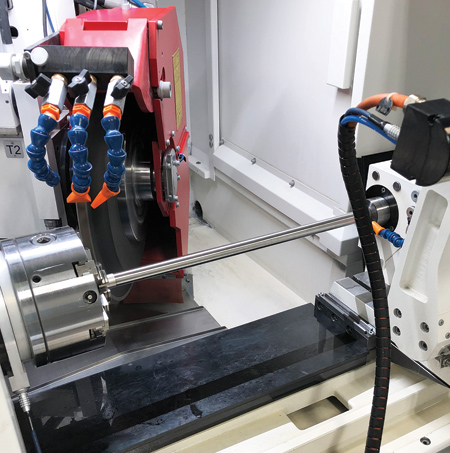
Solid carbide shaft, approximately 17" long, being taper ground
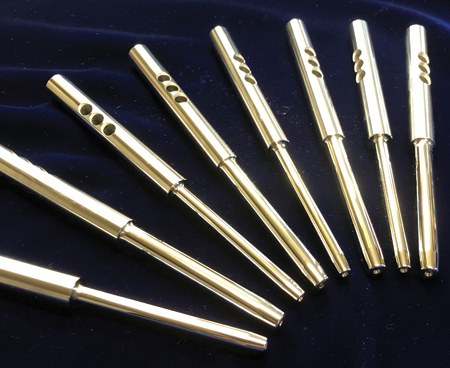
Hardened steel punches O.D., step and angle ground to 4 RMS finishes
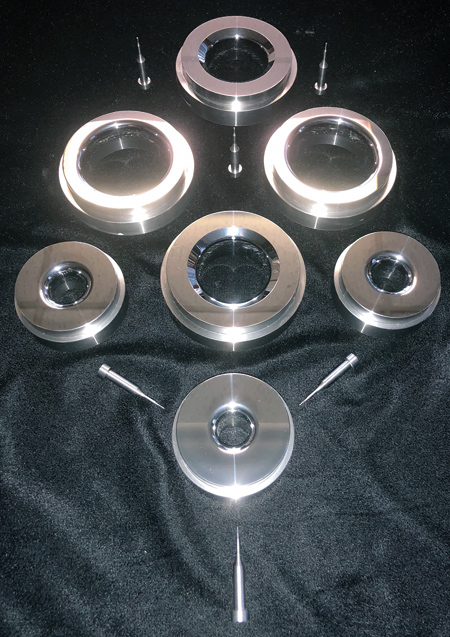
Solid carbide punches and dies illustrating low microinch surface finishes, ground using Studer Contour Software and then hand polished to a mirror finish.
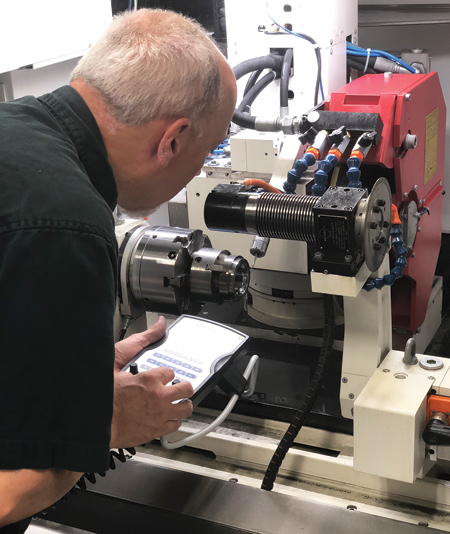
Joe Almeida setting up a Z-axis probing cycle. Note the programmable swing down rotary diamond dresser.
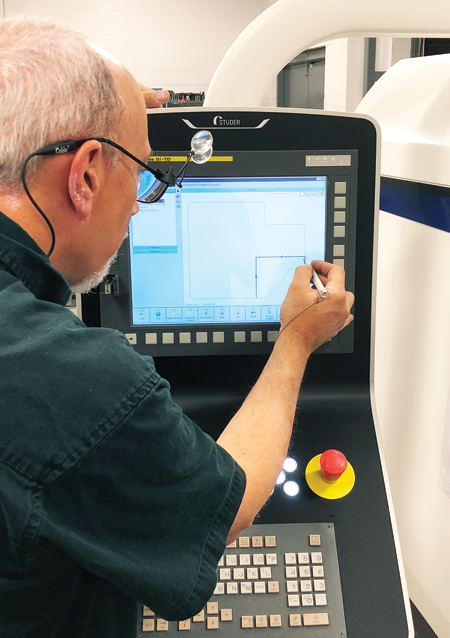
Almeida programming a Studer Contour grind job with the touch screen control
I recognized all the way back in 1992 that the process of finish grinding high precision tooling was a problem that needed to be addressed. A fair percentage of our work at New England Die Co. (NEDCO) involves components manufactured from various grades of tungsten carbide and very hard grades of tool steel. Unfortunately, most of the final details required to complete the parts cannot be done with the more traditional turning or milling processes. The raw materials are simply too hard to machine. As a result, the lion's share of our parts require grinding.
Most of that grinding needs to be done to a very high degree of accuracy-in fact, +/-.0001" is not uncommon, and in some cases even tighter tolerances are requested by our customers.
So why the challenge, what changed? Well as anyone in our industry can attest, tolerances are getting tighter, margins of error smaller and surface finishes need to be finer. Were we able to meet these specifications before? Sure. To do that required skilled hands with techniques honed by years of repetitive actions by highly skilled toolmakers. There is the rub-my toolmakers were getting older, and no one can stop the clock!
Grinding is an art (sure, and some science) that does not have the typical "gee whiz" aspect to it that chipmaking does. Persons new to the trade and apprentices never really wanted to stand in front of a normally wet and dirty machine and tickle away the .0001's slowly. They want to grab a piece of material, write a program and ultimately create something that is tangible. That does not describe the grinding process. It was time for a CNC grinder.
Back in 1992, we had already acquired CNC machine tools that could lathe turn, mill, EDM and wire EDM our parts; we just did not have the grinding aspect covered. Why? It was just a matter of cost. CNC O.D./I.D. and profiling grinders are an extraordinarily expensive piece of equipment and we were a small shop without any type of long term contract in place to produce a product. We were and are a job shop. Even with that in mind, I began the process of researching the purchase of a grinder. To coin an old Beatles song, "it was a long and winding road!"
Exploring Solutions
Considering our budget and lack of long term contracts, I tried to approach the problem from the simplest direction. I began by exploring a retrofit to any of our existing grinders. That was problematic, as it turns out. There just were no readily available manufacturers out there who regularly adapted controls to existing manually operated grinders. Figuring that out, after visiting various manufacturers and attending trade shows, consumed quite a bit of my time. So, I put together a document complete with a number of drawings that represented what I would like this machine tool to be able to accomplish, and I focused on tungsten carbide workpieces. I knew that if the machine can process those successfully, it would have no problem with tool steel.
Numerous visits, five unfulfilled purchase orders and a lot of years would transpire before the solution to my problem was found. During the journey, we did purchase a CNC surface grinding piece of equipment and tried adapting that to do our O.D. and I.D. grinding by using a rotary type device mounted to the worktable, but the platform really was not nearly rigid enough to be competitive. Over the years, we worked with and explored many manufacturers (and yes, my toolmakers got older and the same issues were becoming more pronounced). Certainly, we continued training our existing apprentices on our manual grinders, and as we hired seasoned toolmakers, we made sure that they cycled through the grinding department as well, but the solution was only becoming more clear: CNC.
A New Way of Part Processing
After reviewing all of the possible options, I called Ryan Michels of UNITED GRINDING and told him that it was time. I gave him the drawings and my general requirements, and in a very short period of time he presented me with a formal quotation for a CNC O.D. and I.D. grinding system that would meet my needs. It was quite a process from that moment on as we went through a couple iterations of the machine, hardware and software options and attachments we would need to be able to competitively grind all of our tooling and machine parts. It was a tall order.
They refer to these machines as universal grinders, and that is an accurate description for ours. We are in the strictest regard a job shop. Our typical lot size is one. Sure, there are times that we process some small quantities, perhaps a couple dozen, but the bulk of our business is one-off parts, some round, some O.D. only or I.D. only, non-round shaped components and certainly contoured tooling as well. The S33 that Ryan selected was the perfect fit for our work and our budget.
I certainly had an idea of what I was getting into with the S33, or so I thought. This was a whole new way of processing our parts that I was not really prepared for. What I expected of the machine was far exceeded by the end of the first month. I knew it would grind; I did not realize just how well and how flexible the machine tool and software was. In fact, I would have been severely disappointed with any less of a machine.
The motorized B-axis (the turret under the O.D. and I.D. grinding spindles) is a must. Coinciding with the B is the Quickset software that keeps all of the relationships of the machine in sync-the probe, both spindles and all of the angular offsets. Basically, I start up the machine in the morning, probe the Z0 surface of my workpiece and begin to grind. The control knows where both spindles are automatically, as well as any of the I.D. grinding quills and previously mounted O.D. wheels. My machine has one O.D. and one I.D. spindle, but I already have a grinding wheel catalog of over three dozen different wheel combinations. Any of the I.D. quills can be utilized in the program with nothing more than a quick program stop and a quick quill change. Quickset keeps all of the wheel length and diameter data current. This is how I can quickly program and grind many different components, one-off, in a single day. I commonly utilize two or three I.D. wheels in a single program. Flexibility is the key and the software on this control allows me to switch directions all day long.
Now, I do not want to make it appear too simple, however, the devil is in the details. As my trainer (and right-hand man from UNITED GRINDING) Long Phan would say "It's the physics, Joe!" This was the part of the equation I was not as prepared for. The machine is so incredibly rigid that all variations in the process affect the outcome. Speeds, feeds, dwells and dressing parameters are critical, and Long gave me a great start in that department. He was concerned that when the formal training was over that I may not be ready to run as successfully as I had hoped. He was wrong in that respect. I walked and then I ran. Productivity has soared. This one machine tool outperforms my four manual grinders. Keep in mind that none of our existing machines are capable of grinding contours or out of round tooling-that is a bonus.
There is also the question of quality-has it improved? In that regard, I would have to say no. We always processed our tooling to the tightest tolerances our customers would ask for-a tenth (.0001") is a tenth, it does not matter how you get there. With that being said, we sure get there a lot quicker with quite a few less operations. A typical round tungsten carbide draw die would have had upwards of eight or nine operations; that has been reduced to three or four at most. As some would say, that is huge! When you consider non-round grinding, there is simply no comparison to the older method of setting grinding fixtures with various stops and pins and gage blocks. One application we had was reduced from 12 operations to two, and those parts were ground from the solid, which eliminated all of the time-consuming prep machining time.
Flexibility is Key
Roughly half of our work currently involves the manufacturing of tungsten carbide tooling and wear parts, so the S33 is ideal in that regard since this material cannot be otherwise machined. The balance is a good mix of various grades of tool steel from O-1 through CPM-15V and everything in between. Again, the key for NEDCO is flexibility. With that in mind, our workholding system is perhaps a little out of the norm. Since a fair amount of our work can and should be held by a chuck, that is the basis we start with when deciding how best to process a part. Do we grind on center? Of course, but to be as quick as possible in the set-up, I have designed a special holder for the chuck to convert the machine to a centers type grinder without removing the chuck. Magnetic workholding is also utilized just about every week, and we have a quick method of utilizing that device as well.
Inherent to all of these methods is preserving the function of one of the most important features of the machine: Sensitron. I will describe that option as an acoustical listening device that detects contact with the grinding wheel. In reality, it is so much more that I have not scratched the surface of what it can do. Sensitron registers contact, pure and simple, to an extremely precise degree. You can use it to monitor your grind and the dress of the wheel, and you can even use it to minimize the air gap for a much faster rapid approach to the workpiece as well.
Our machine is equipped with just about every option that is available for the S33. Quickset for instant part vs. grinding wheel relationships; Contour software that allows for rapid programming of radial, angular and other circular forms in any level of complexity; StuderForm for the generation of non-round features; and Studer Technology to rapidly set a starting point for speeds and feeds as well. Did I mention the motorized B turret? It is a must have for small lot grinding. The ability to simply rotate in a new grinding head or to grind parts at various angles with a straight wheel is critical to one piece batches. With all of these available tools, set-ups really are quite simple. For a typical chucked workpiece, simply tighten the chuck, swing in the probe and automatically set Z0 and begin grinding.
NEDCO has been in business for over 75 years, and I been with the company for almost 48 years. I was hired by the company founder and started out polishing and sizing tungsten carbide wire draw dies; by the age of 15 I was training some apprentices, and the rest is history.
We currently have eight employees, a great number I think from a flexibility standpoint. We also have an active state of Connecticut approved apprenticeship program with two apprentices currently in the program. I strongly feel that as skilled craftsmen, we need to give back for the future of the career, and we can best do that by training other toolmakers.
NEDCO has CNC turning and 4-axis CNC milling machines, both manual and CNC surface grinding, laser marking, ram and wire EDM and of course CNC grinding. We really are a true job shop focusing on tight tolerance, low micro inch surface finished components. NEDCO is also Connecticut's oldest EDM company since we been "burning" here since 1957. We began in the wire EDM field in 1979 and specialize in close fits, fine finishes and small wire EDM work.
As far as company goals and philosophy, our logo really says it all: "A tradition of Excellence." At NEDCO, we are sticklers for the details and we maintain tolerances. That is commonly said, but not commonly achieved. We regularly produce tooling, punch and die sets with fits and clearances in the 80 millionths of an inch range. Quality and attention to detail is really what we are all about. Customers never have to concern themselves as to whether or not the tooling or precision machined parts they receive will be correct. They will be spot on in every criterion. We have the ability to measure every feature on every component we manufacture-that is no small undertaking. Quite often when I am giving a plant tour, I relay that very same mantra. You should only have faith in those companies that can demonstrate the ability to measure and verify everything they do. If you cannot measure it, you probably should not take the job. Excellence is what we do, it is who we are. Our goal is to maintain that reputation no matter what industry we are serving or what tolerance a customer is expecting us to achieve. I teach our apprentices those same guidelines. "Know where you are and know where you are going" is one of my favorite phrases. We are going to outperform any and all competitors using the latest technology available.
Authored by Joe Almeida, Owner, New England Die Co., Inc.
For more information contact:
New England Die Co., Inc.
48 Ford Avenue
Waterbury, CT 06708
800-955-0820 / 203-574-5140
sales@newenglanddie.com
www.newenglanddie.com
UNITED GRINDING North America Inc.
2100 UNITED GRINDING Blvd.
Miamisburg, OH 45342
937-859-1975
info@grinding.com
www.grinding.com