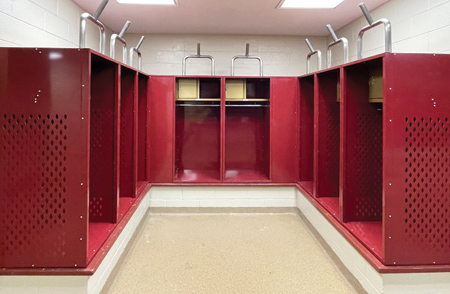
Open front athletic lockers with helmet racks added on top. These lockers have been used in elementary, middle, high schools and colleges with modifications to fit business or sports uses.
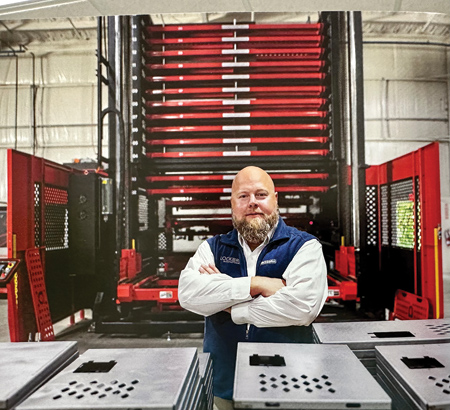
Keith Dunham, founder/CEO of LockersMFG
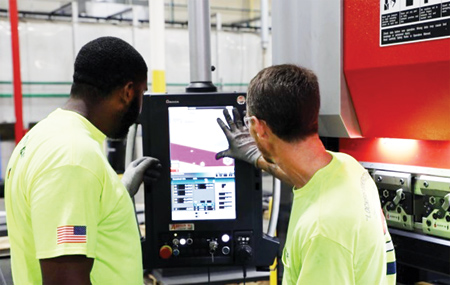
Programming a press brake
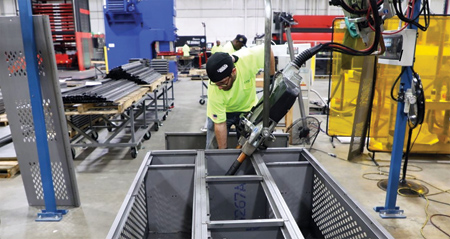
Weld assembly station
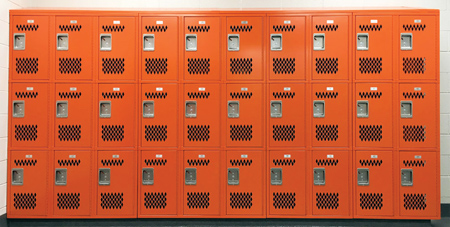
Lockers for a sports club
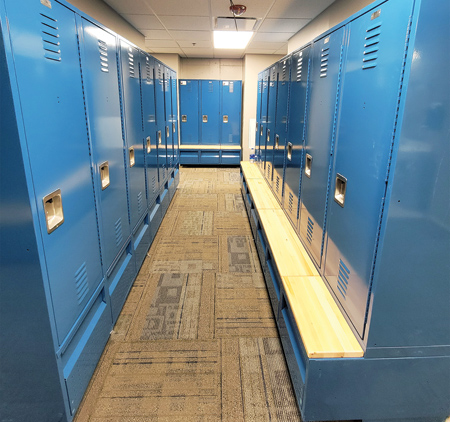
Military/government lockers
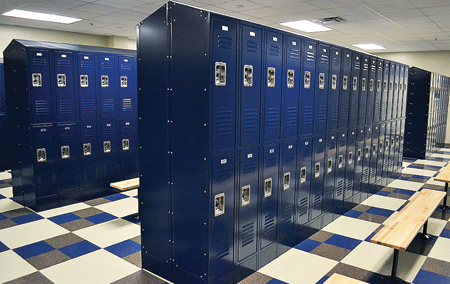
LockersMFG designs, engineers and manufactures lockers for a diverse customer base.
In 2013, Keith Dunham set out on a mission to bring reliable storage product manufacturing back to the U.S. Today, LockersMFG designs, engineers and manufactures lockers for its diverse customer base from its state-of-the-art facility in Mississippi.
Dunham and his team decided that, rather than purchasing an existing factory and refurbishing it for their product mix, they would start with a blank slate.
"We decided to take a very comprehensive look at the vendors that sell the type of sheet metal equipment we needed," said Dunham. "We knew that selecting the right partner was essential, and we could not afford to get it wrong. We ultimately chose Amada equipment as the superior product and service line. Amada provides state-of-the-art CNC equipment and machines and also offers a training and service package, which was just what we needed to launch this start-up factory operation from scratch."
The Amada fiber laser selected by LockersMFG has a speed capability of up to 5,000 mm/s. With a 3-kW output, it is capable of efficiently cutting mild steel up to 1" in thickness. The turret punch has a substantial punching force of 22 tons and can handle materials with a maximum thickness of 3.2 mm. Its average feeding speed is 70 mm/s, with a maximum hit rate of 900 IPM and accuracy of 0.1 mm. For bending operations, the brake press has a maximum tonnage capacity of 243 tons with a bed length of 4 m. The resistance/spot welders feature 7 kA of current at around 80 PSI of pressure.
LockersMFG recently invested in AMADA's IIoT software solution, Influent. "It provides real-time visibility so we can quickly pivot our strategy based on the performance metrics of every machine in our shop," said Dunham.
The material primarily used by LockersMFG is cold-rolled sheet steel, ranging anywhere from 20 gauge to 14 gauge with a standard sheet size of 74" x 60". This will sometimes vary based on job specifications but will not deviate too far from the standard.
The manufacturing process begins with product modeling using CAD software. The product design undergoes a series of CAM processes to generate the requisite manufacturing programs.
Once the programs for the various parts are created, they are loaded onto the laser cutting machine. The laser precisely cuts the parts, which are then carefully stacked and separated into their designated staging locations. In the case of parts requiring perforation, they are processed through the turret punch.
All parts are then transferred to the press brakes, where they undergo precise bending. Following the bending process, the individual parts are resistance welded together to form a cohesive unit. This unit is then suspended on the in-house powder coating line, where it undergoes a thorough painting process. LockersMFG's seven stage powder coating line includes two ovens from Parker Ionics. All of the end products endure a 1,000-hour spray test.
Upon completion of the painting stage, the necessary small components such as doors, hooks and other relevant parts are securely riveted onto the unit. Finally, the finished product is wrapped and prepared for shipping.
LockersMFG manufactures and oversees locker installation for school, factory, public and private locker projects, and also provides heavy duty military lockers and a line of smart lockers and related products.
For more information contact:
LockersMFG
209 Pearson St.
Batesville, MS 38606
662-338-4340
www.lockersmfg.com
Amada America, Inc.
7025 Firestone Blvd.
Buena Park, CA 90621
877-AMADAUS / 714-739-2111
www.amada.com