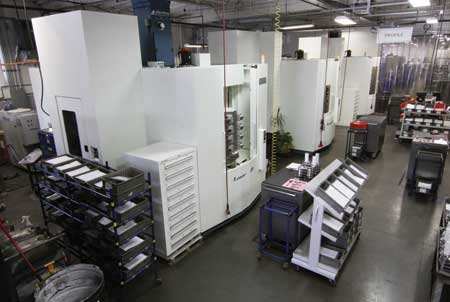
Optimized workflow in the Kitamura aisle of the Profile Machining Department at CP-Carrillo. CP-Carrillo has two Mycenter-HX400IFTGA (400 mm) and three Mycenter-HX500iTGA (500 mm) horizontals.
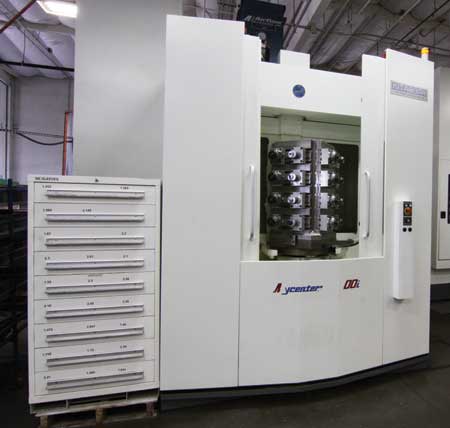
CP-Carrillo utilizes Kitamura machines for complex multi-angle large part machining using multi-part tombstone fixturing.
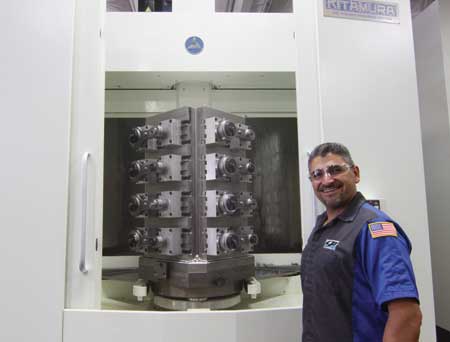
CP-Carrillo Supervisor Rigo Vargas and the tombstone design used with the Kitamura machines. This allows for more parts per load and provides access to more machining angles.
CP-Carrillo, a worldwide supplier of high-end motorsports components, needed to increase manufacturing productivity of its pistons and connecting rods for the motorsports racing industry, OEM and high performance vehicles. The company identified two main areas to meet this challenge: machine operators needed to be able to operate multiple machines at a time rather than just one, and more part features needed to be machined with one clamping. To accomplish this, the company needed to replace its older, slower machines with more modern, productive units.
The CP-Carrillo team took into consideration several solutions as they reviewed their options. These included new and used horizontal machining centers (HMCs), retrofit vertical machining centers (VMCs) with a pallet changing unit, and a new tombstone design.
After diligent review, the team selected new Kitamura Mycenter HMCs and new tombstone designs. The HMCs provide an expansive work envelope allowing for easy loading and unloading of parts, as well as machining access to several surfaces per clamping. In addition, a new machine was close enough in price to validate the purchase - and has the added benefit of a new warranty. A new tombstone design allows more parts per load and provides access to more angles.
"We have made the correct choice - the new HMCs are performing as expected," said Barry Calvert, CEO/President, CP-Carrillo. "We are able to machine parts from different angles. More features machined per clamping reduces tolerance stacking. Our productivity has greatly increased, and one operator can now run several machines."
CP-Carrillo has two Mycenter-HX400IFTGA (400 mm) and three Mycenter-HX500iTGA (500 mm) horizontals. Both machines feature the versatility of a standard full 4th axis rotary table for both complex multi-angle large part machining and multi-part tombstone fixturing.
The Mycenter-HX400IFTGA is designed for fine surface finishes and high precision. It is engineered for machining precision parts in medium to large quantities, large parts with extensive machining and parts made from tough materials. It features a 25 HP AC motor as standard, solid boxways with precision twin ballscrews, 1,969 IPM feeds on each axis, #40 spindle taper tooling and 5-second pallet change - all within a compact footprint. Table work area measures 15.7" x 15.7" and table load capacity is 880 lbs. XYZ travels are 28.9" x 24" x 24".
The Mycenter-HX500iTGA is designed for large capacity, high production precision machining. It can machine large parts with multiple faces and can handle tough materials, and is designed to complete more precision parts in less time. Within a space efficient footprint is a standard 35 HP AC motor, precision hardened boxways with precision twin ballscrews on each axis, #50 spindle taper tooling and six second pallet changes. Table work area measures 19.7" x 19.7" and table load capacity is 1,760 lbs. XYZ travels are 34.3" x 28" x 26".
CP-Carrillo manufactures high-performance connecting rods for motorsports that are precision machined from heat treated steel or aluminum. "In the past, we were using VMCs with usually four parts per load," said Calvert. "With the change to horizontals, we are able to get to several sides of each part and load eight parts per load, with an additional eight parts on the other pallet."
The team is now also able to combine several machining operations in each clamping. In one example, they are able to profile a part on one plane, and then rotate the pallet 90° and drill in an area that usually would have required an entirely different set-up.
"Tolerance control is vastly improved due to the high accuracy of the machines and the multiple machining steps that have been combined," said Calvert. "This has resulted in reduced tolerance stack up."
According to Calvert, their strategy of moving leftover manual operations to CNC and vertical CNC operations to horizontal CNCs has led to 30% more volume while using 30% fewer workers. "Employees are being retrained to run the new equipment, creating a win-win situation for everyone involved," he said.
CP-Carrillo is ISO 9001:2008 certified and TS 16949 compliant. "We are committed to growth through quality, value, customer service and continuous improvement," said Calvert.
For more information contact:
Barry Calvert, CEO/President
CP-Carrillo
1902 McGaw Ave.
Irvine, CA 92614
949-567-9000
bcalvert@cp-carrillo.com
www.cp-carrillo.com
Kitamura Machinery of USA Inc.
78 E. Century Drive
Wheeling, IL 60090
847-520-7755
info@kitamura-machinery.com
www.kitamura-machinery.com