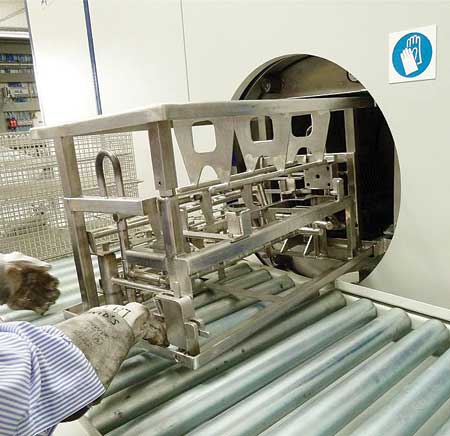
The dedicated jetting basket developed by MecWash ensures that the wash and rinse solutions penetrate into all critical bores and passageways of the components.
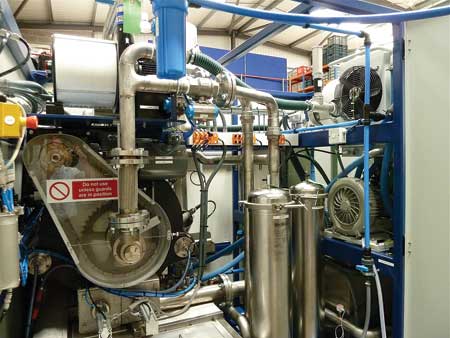
Inside the MecWash Midi 800 at Woodward's facility.
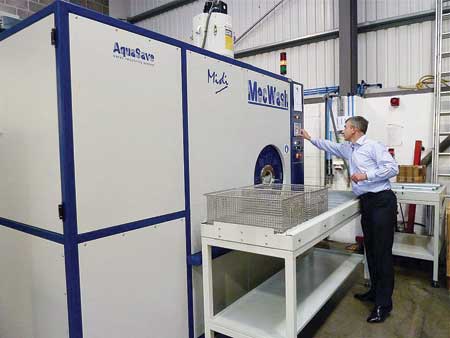
The MecWash Midi 800 at Woodward's facility. "With the MecWash Midi, once the components are loaded into the baskets and pushed into the chamber, we just push the 'Start' button and walk away," said Woodward Manufacturing Engineer Jeremy Griggs.
Woodward of Loveland, CO, makes diesel fuel injection pumps for high horsepower engines used in large mining trucks as well as marine applications and power generation equipment. Delivering fuel into these engines at high pressure allows that fuel to burn cleaner and meet ever more stringent emissions specifications. To attain pressures of up to 36,000 psi, the Woodward components are machined to very tight tolerances. At these pressures, even the smallest foreign debris left over from machining would be catastrophic, so they have a demanding cleanliness specification. A MecWash Midi 800 aqueous parts washing system with dedicated jetting helps them to meet and exceed their most stringent cleanliness requirements.
Woodward fuel pump components are manufactured, stocked and then assembled to order. When a build order comes in, the cast iron and steel components are pulled from stock and demagnetized. Demagnetization breaks the bond that holds these filings, making it easier for the parts washer to flush out this unwanted debris. This cleaning process was developed along with the original pump design at Woodward's research and development facility in Aken, Germany.
All metallic components used in this build require washing prior to assembly, several of which require special interior jetting. This includes the housing, which at approximately 18" in length and 12" in height is the largest of the components.
The housing is placed in a special wash fixture fitted with dedicated jetting - a process developed by MecWash designed to ensure that the wash and rinse solutions penetrate into all critical bores and passageways of the components. Specially fabricated fixtures designed by MecWash are used to secure components for full rotation in the Midi as well as position the component for dedicated jetting. The fixtures are made from aluminum framing and stainless steel piping equipped with spray nozzles pointing directly at the specified machined bores to be cleaned. When the jetted fixture is pushed into the cleaning chamber, the fixture engages with a water inlet coupling in the rear of the Midi, which feeds the fixture piping with the wash then rinse water so the component is washed both over the surface and through its interior. The jetting fixture sprays wash and rinse water into the interior of the component during full rotation. During full rotation, gravity ensures that any metal particles flushed out of the component fall out during this rotation. Full rotation is a complementary part of the dedicated jetting process. In addition, the dedicated jetting feature is also used to blow hot air into the component to dry its interior cavities, ensuring the component is dry and ready for assembly.
Woodward's other components requiring only surface wash - cam shafts, flanges, fasteners and more - are washed in basket stacks. These basket stacks are also specially designed to hold as many small parts in sub-compartments, so in conjunction with the two dedicated jetting baskets, an entire pump housing family of small parts can be cleaned together in one cleaning cycle. Woodward's components, made from cast iron and steel, are cleaned using MecWash AC-38 cleaning compound. A rust inhibitor in the compound (in both the wash and rinse tanks) prevents corrosion of the components.
"With the MecWash Midi, once the components are loaded into the baskets and pushed into the chamber, we just push the 'Start' button and walk away," said Woodward Manufacturing Engineer Jeremy Griggs. The operator literally starts the process with the push of a button and the Midi operates on full-automatic mode. "Once the machine finishes the washing cycle, the part is clean, dry and ready to go into the clean room. There is no question whether it is clean, and no question that it is dry," said Griggs.
According to Griggs, the ability to fine-tune the wash programs with the Midi PLC interface - by increasing or decreasing the dedicated jetting, flood wash, ultra-sonic and dry times - ensures that the components are cleaned and dried in the timeliest manner possible. And since the MecWash PLC unit can store up to 22 programs, there is ample opportunity to create unique cleaning programs for new part designs. This "push button" convenience allows Woodward personnel to attend to other tasks while the MecWash Midi cycles through its steps.
Since the now-cleaned components exiting the MecWash chamber are very hot, they are allowed to cool inside the clean room. Once cool, they are assembled and sent to a test cell that mimics engine load conditions before the pump is crated for shipment.
"We are pleased to work with Woodward here in Colorado and in Germany," said Bill Westbrook, North American Operations Manager for MecWash Systems. "Our dedicated jetting design, which can be installed across the entire model range of MecWash cleaning systems, is really the perfect application for Woodward's high pressure fuel pump assemblies. Furthermore, Woodward is a worldwide manufacturer with a customer base in aerospace, industrial and defense industry companies and is second to none. For us at MecWash, it is an honor to build equipment for them."
MecWash Systems offers a complete line of aqueous cleaning for cleaning turned parts, machined components, castings, pressings, extrusions and other high-value engineered components. It offers equipment designed for 24/7 operation in the most demanding cleaning applications in the aerospace, automotive, hydraulic, pneumatics, medical and precision machining industries. MecWash cleaning systems can be found in the manufacturing facilities of companies that include Rolls-Royce Aerospace, Goodrich, TRW, Caterpillar, Delphi, GE, Parker, SKF and others.
Woodward is an independent designer, manufacturer and service provider of control solutions for the aerospace and energy markets. Its aerospace systems and components optimize the performance of fixed wing and rotorcraft platforms in commercial, business and military aircraft, ground vehicles and other equipment. Its energy-related systems and components enhance the performance of industrial gas and steam turbines, reciprocating engines, compressors, wind turbines, electrical grids and other energy-related industrial equipment. The company's innovative fluid energy, combustion control, electrical energy and motion control systems help customers offer cleaner, more reliable and more efficient equipment. Customers include leading original equipment manufacturers and end users of its products.
For more information contact:
Woodward, Inc.
P.O. Box 1519
1000 East Drake Road
Fort Collins, CO 80522-1519
970-482-5811
www.woodward.com
Bill Westbrook
MecWash Systems
220 Campus Drive
Aurora, OH 44202
440-564-7894
billwestbrook@mecwash.com
www.mecwash.com