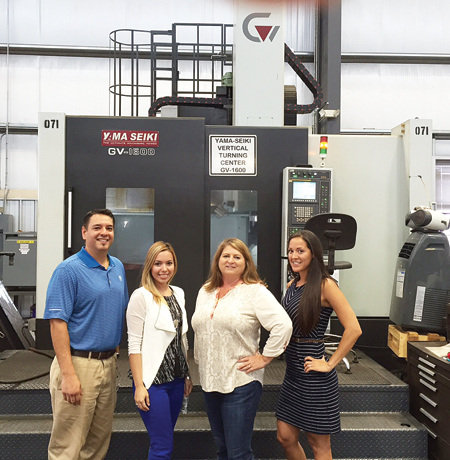
The WOODCO USA sales team: (l-r) Shawn Reyes, Cynthia Zermeno, Cindy Brown and Jaclyn Mascorro
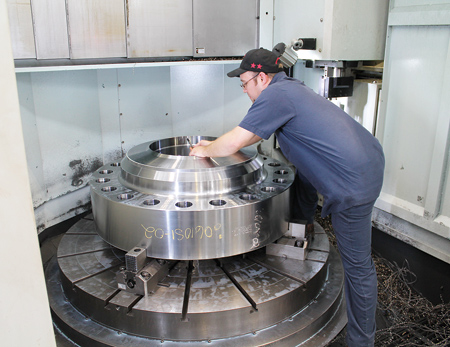
An operator sets an API double studded adapter on the new Yama Seiki GV1600 VTC
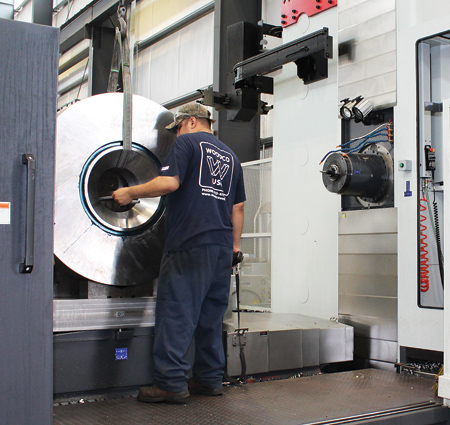
An operator positions an API double studded adapter on the new Yama Seiki BL2018 HBM
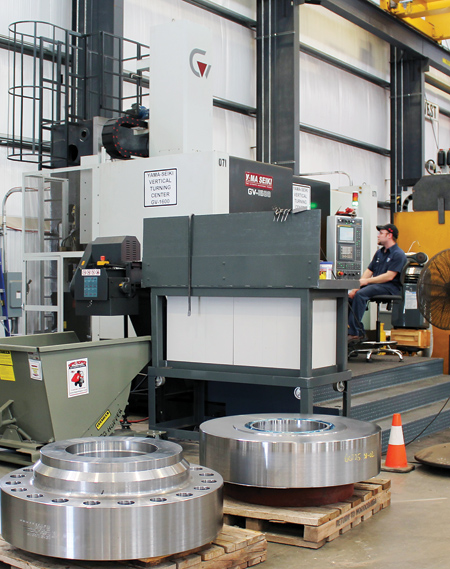
Yama Seiki GV 1600 with API weld neck flanges.
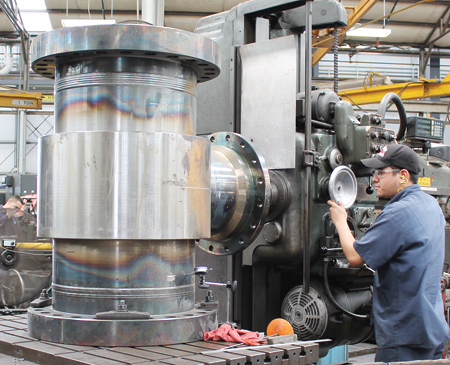
WOODCO USA's manual machine could not keep up with increasing product demand, resulting in a backlog.
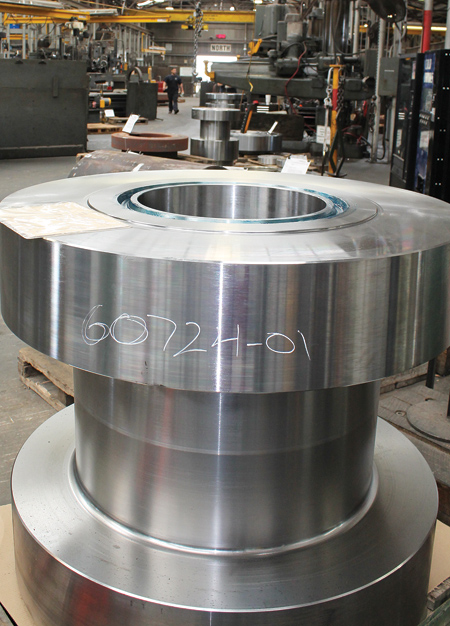
Spacer Spool staged for drilling on the Yama Seiki BL2018 HBM.
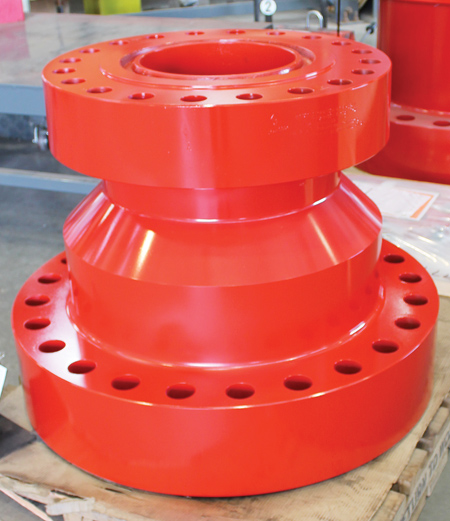
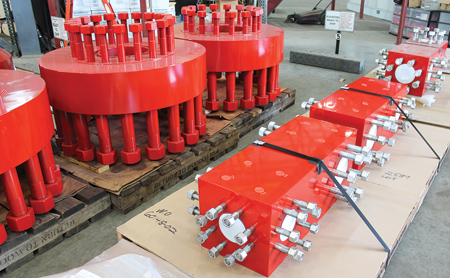
Finished products at WOODCO USA
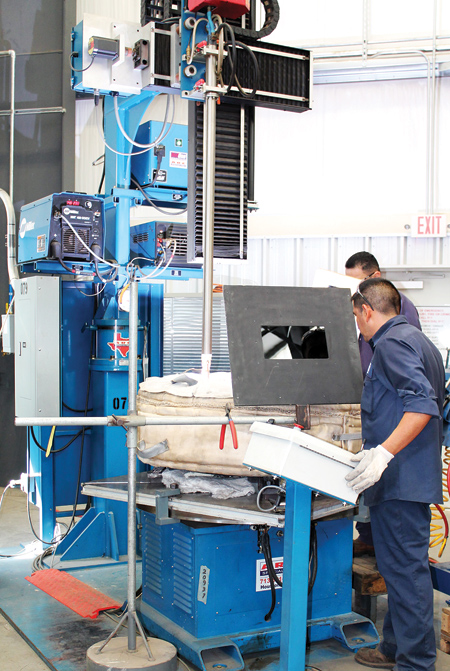
Most of WOODCO USA's Inconel cladding is now performed in-house.
The demand for WOODCO USA's larger oil and gas pressure control products and clamps was increasing rapidly and customers needed quicker delivery. Being a predominantly conventional manufacturing facility, multiple set-ups and the use of conventional methods simply did not allow it to produce the numbers of components quickly enough to meet the required delivery times. According to Tommy Malone, WOODCO USA's Director of Technology, the major challenges were productivity and efficiency.
While WOODCO USA had some CNC equipment, its CNC machines were not large enough to produce the larger pressure control products. The WOODCO USA team considered outsourcing, but ultimately decided that losing control of scheduling and quality was not an option.
WOODCO USA personnel, which included Tommy Malone, Plant Superintendent Mike Deleon and CNC Machine Shop Supervisor Hector Montes, began researching large diameter vertical turning centers and boring mill solutions.
The WOODCO USA team selected Yama Seiki's Goodway GV1600 vertical turning center to turn large spools and adapters because it can swing over 75" and support a 17,500 lb. part. The GV1600's 60 HP true geared headstock produces over 17,000 ft-lbs. of torque.
Once turned, WOODCO USA can drill and thread mill holes on its new Yama Seiki AWEA BL2018S horizontal boring mill. The BL2018S is the smallest in its family of boring mills but it can support a 78" x 70", 26,000 lb. part, which is all WOODCO USA needed to drill the holes in its larger API double studded adapters and other pressure control equipment.
According to Deleon and Montes, what once took 8 hours on large conventional turning lathes is now being turned in 4 hours on the Yama Seiki GV1600. Likewise, what once took an additional 8 hours on conventional drilling machines is now being done in 2.5 hours on the Yama Seiki BL2018S. Further, the cutting tool and fluid technology applicable to its new CNCs is much more economical, efficient and available. The whole process is much safer for the operators and easier on the shop's environment. The API double studded adapters that once took 24-30 hours to machine are now being machined in 9 hours.
WOODCO USA's heavy API double studded adapters, which are machined from 4130 heat treated steel, require a crane or forklift to move them from machine to machine and to reposition them on a machine. The ability to process them near complete at two stations (the new VTL and the new HBM) significantly reduces non-cutting time.
The power and speed of the new Yama Seiki GV1600 VTC allows for more efficiency and more aggressive cutting tools to be utilized, thus increasing metal removal rates. Montes stated that what once took 8 hours to turn now takes roughly 4 hours. He added that the combined high capacity automatic tool changing and CNC functionality also reduces operator intervention dramatically and increases operator safety.
The API double studded adapters that WOODCO USA produces contain 20 2-7/8" diameter holes, threaded 3" 8UN. Before the purchase of the Yama Seiki BL2018 HBM, these holes took roughly 8 to 9 hours to drill and tap. The taps were very expensive, as was the labor due to the fact that the holes required continuous operator involvement. CNC functionality, high-pressure coolant and thread milling have dramatically simplified the process. According to Deleon, the holes on a large API double studded adapter now take only 2.5 hours on the new Yama Seiki BL2018 HBM.
Almost every product that WOODCO USA manufactures requires one or more Inconel clad API ring groove. WOODCO USA has recently added a second arc welding machine from Arc Specialties, so now most of its Inconel cladding is done in-house.
Founded in 1958, Wood George established Wood George & Co. as a private business engaged in buying, repairing and selling used oilfield drilling equipment. The subsequent and present owner, Ashley George, purchased and incorporated the business in the State of Texas in 1973. By 1975, the company had evolved into a manufacturer of specialty oilfield products. The corporation began doing business under the name WOODCO USA in 1984 and currently has 67 employees.
Wood George & Co. acquired its first American Petroleum Institute (API) Monogram license in 1978. Today WOODCO USA currently has four API Monogram licenses to manufacture and monogram (mark with the API logo) a variety of equipment.
Ashley George believes that his commitment to quality and the development of long-term employees have been the key to the company's success. Mr. George's philosophies can be summed up in the quote: "Our primary goal is not to make money, but to make a great product and one that will not fail in service; making money is a welcome by-product."
For more information contact:
WOODCO USA
773 McCarty Drive
Houston, TX 77029
713-672-9491
contact_us@woodcousa.com
www.woodcousa.com
Yama Seiki USA, Inc.
5788 Schaefer Ave.
Chino, CA 91710
909-628-5568
sales@yamaseiki.com
www.yamaseiki.com
SOUTHWEST ONLY
Hillary Machinery, Inc.
1825 Summit #207
Plano, TX 75074
800-683-1516
sales@hillaryinc.com
www.hillaryinc.com