
DMG MORI Premiers New Machines at DECKEL MAHO Pfronten Open House
January 26, 2016The focus of the DMG MORI Open House event at DECKEL MAHO Pfronten, Germany, from January 26-30, 2016, will be on the latest innovations and technologies. In an exhibition area of 79,653 sq. ft., the machine tool manufacturer will be showcasing in total 90 live exhibits in operation, including DMG MORI best-sellers, as well as six world premieres featuring turn-mill complete machining, universal milling, XXL parts machining and new technologies.
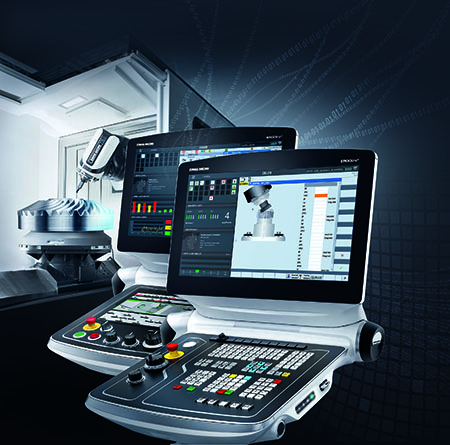
DMG MORI technology cycles: Software solutions for complex machining processes
“Besides production and automation solutions, with CELOS and DMG MORI technology cycles, DMG MORI will be giving answers to the question of digitization on the path to intelligent production in Industry 4.0,” said a company spokesperson.
CELOS and DMG MORI Technology Cycles for Industry 4.0
“With CELOS, DMG MORI is offering a user interface that can be expanded with new apps and updates, which provides a solution to Industry 4.0,” said the spokesperson. CELOS is designed to be easy to use, networks all machines within a manufacturing organization and can simplify the process from the idea to the finished product. Sixteen apps help the operator prepare, optimize and process production jobs and enable the consistent administration, documentation and visualization of order, process and machine data.
“With 31 DMG MORI technology cycles as another highlight, DMG MORI is presenting software solutions on the 5-axis and turn-mill machining centers to make complex machining processes a reality,” said the spokesperson. Due to parameterized context menus, complex processes can be directly programmed on the machine up to 60% faster. For the easy to learn and ready-made windows to enter data, programming is hardly needed and complicated DIN programming are avoided. DMG MORI technology cycles are designed for application-specific shop floor programming.
World Premiere: CTX gamma 3000 TC Second Generation
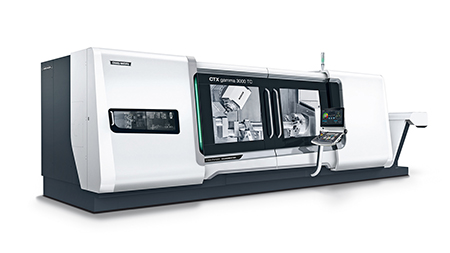
The CTX gamma 3000 TC Second Generation features 31.5” X travel with the new compactMASTER turn-mill spindle rated at 162.3 ft-lbs. torque.
A turning length of 120” makes the CTX gamma 3000 TC Second Generation the largest turn and mill complete machining center in the now completely revised CTX TC series from DMG MORI. DMG MORI has equipped this latest machine with a new compactMASTER mill-turn spindle, with which 162 ft-lbs. achieves a 120% higher torque.
With a diameter of 7.9“ the length of the compactMASTER spindle has been reduced by 2.8” so that it now measures only 17.7”. The interplay of the 5.9” larger X-axis (-0.9 / +6.9”) and the 0.8” longer Y-travel of ± 8.3” brings a large gain in freedom for users. This enables, for example, the radial machining of workpieces with maximum diameters of 27.6” with 6.7” long tools (with the B-axis in a vertical position). The CTX gamma 3000 TC Second Generation is equipped with 36 tool pockets in its standard version. This capacity can be increased optionally to 80, 120 or 180 tools. Maximum tool length is 21.7”
World Premiere: DMU 160 P duoBLOCK Fourth Generation
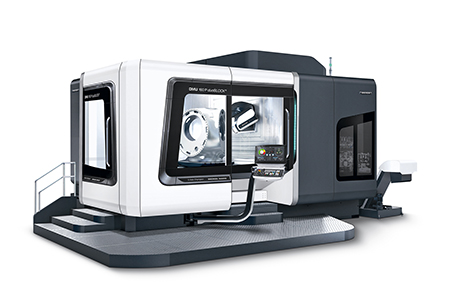
The DMU 160 P duoBLOCK Fourth Generation with 30% higher precision, power and efficiency
The world premiere of the DMU 160 P duoBLOCK Fourth Generation complements the duoBLOCK series from DMG MORI and has improvements in precision, performance and efficiency of around 30%. Added to this the high level of rigidity, extensive modular spindle range and innovative cooling measures help ensure machining performance and long-term accuracy. Equipped with CELOS the machine also offers user-friendly production.
“As a stable universal 5-axis machine the DMU 160 P duoBLOCK Fourth Generation unites precision with maximum performance,” said the spokesperson. With travel paths of 63.0” x 63.0” x 43.3” in X, Y and Z it has space for a wide spectrum of components, with workpieces weighing up to 9,920 lbs. The wheel magazine has – depending on expansion stage – space for up to 453 tools (SK40/HSK63) and helps ensure flexibility where tools are concerned. The modular spindle range of the DMU 160 P duoBLOCK Fourth Generation offers a variety of choices. The offer ranges from the powerMASTER motor spindle with 1,000 Nm to a gear spindle with up to 1,327 ft-lbs. and on to include the speedMASTER spindle with high speeds of up to 30,000 RPM.
World Premiere: DMU 210 P Second Generation
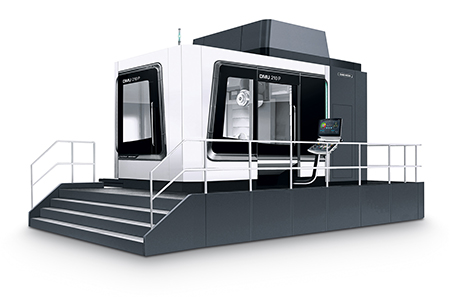
The DMU 210 P Second Generation with 5X torqueMASTER for maximum cutting power with 958.8 ft-lbs. torque
The DMU 210 P Second Generation has an optimized work area, which now measures 82.7” x 82.7” x 49.2”. “It is the prelude to the new generation of portal machines from DMG MORI,” said the spokesperson. “A higher level of rigidity and an intelligent cooling concept that includes a spindle growth sensor help ensure long-term accuracy for the DMU 210 P Second Generation, making it more accurate than its predecessor.”
The DMU 210 P Second Generation is easy to install due to its three-point support and features 30% reduced energy consumption. The modular concept of the new portal machine includes a wheel magazine that can hold up to 303 SK50 tools and a variety of spindle choices. The 738 ft-lbs. powerMASTER motor spindle and the torqueMASTER gear spindle with up to 1,327 ft-lbs. are available for heavy-duty machining.
World Premiere: DMU 600 G linear

The DMU 600 G linear gantry machine with linear drives in the X-, Y- and Z-axes for improved surface quality
“In the XXL Center at DECKEL MAHO in Pfronten, DMG MORI designed and constructed the DMU 600 G linear for best surface quality and high dynamics. These are achieved through the use of the innovative contactless linear motor drive technology,” said the spokesperson. The design of the machine has been optimized with regard to static and dynamic rigidity and ensures consistent temperature stability due to extensive temperature control measures for the structure, components and guides. Energy-efficient consumption is achieved by the use of innovative cooling technology and needs-based activation of units.
The DMU 600 G linear is designed for workpieces weighing up to 60,000 lbs., with a point load of 3,072 lb/ft2. The table measures 196.8” x 118.1” in a work area of 236.2” x 137.8” x 59.1” in the standard configuration. The plunger with optimized interference contour enables travel up to 78.7” in the Z-direction. The modular spindle range includes a torque spindle with 12,000 RPM and 221.3 ft-lbs., a vertical headgear spindle for maximum torques up to 1,844 ft-lbs. and a motor spindle with a high speed of 28,000 RPM.
World Premiere: DIXI 125
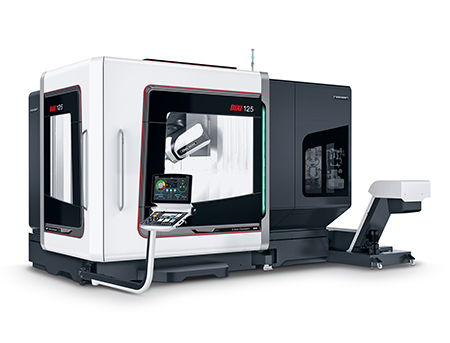
The DIXI 125 features maximum volumetric precision of < 0.0006” and up to 0.0002” positioning accuracy
DMG MORI has extended DIXI series to include the smaller DIXI 125 for workpieces with diameters up to 49.2”. The DIXI 125 has a volumetric accuracy of less than 0.0006”. “The basis for this are the manually scraped guide contact surfaces that achieve a flatness and straightness of 3 µm when mounted, perfect machine geometry and on-site volumetric measurement and compensation,” said the spokesperson.
A 259 gal. coolant unit with reference-guided temperature control and a – also reference-guided – machine cooling unit for the main drive, feed drives, guides and machine structure together with a thermo shield that insulates against ambient influences provide thermal stability. “This is further optimized by the individual thermal compensation of every single machine and the use of the spindle growth sensor (SGS) for direct measurement and compensation of spindle rotor displacement,” said the spokesperson.
World Premiere: ULTRASONIC 20 linear Second Generation
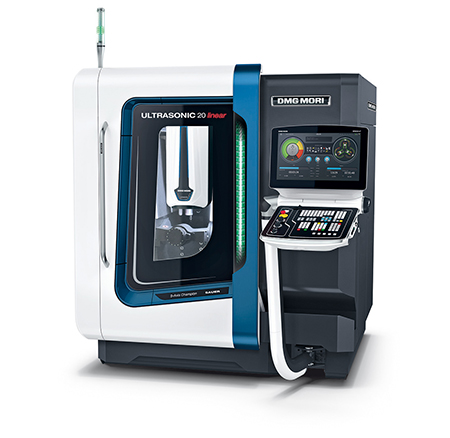
The ULTRASONIC 20 linear Second Generation offers compact 5-axis grinding of advanced materials as well as the latest generation HSC milling
The revised ULTRASONIC 20 linear Second Generation features a new, functional design and a reduced footprint of 37.7 sq. ft. The technological optimizations include the now optional 60,000 RPM speed of the spindle, up to 47% (A-axis) more powerful drive motors, a 33 lb. higher load weight and the use of larger tool diameters up to 2.0”. “Another highlight is the high-speed C-axis (1,500 RPM) for high-precision and productive internal and external cylindrical grinding of rotational-symmetric workpieces made of advance materials,” said the spokesperson.
“Where control is concerned, the ULTRASONIC 20 linear Second Generation supports users with a multitude of new functions. The ULTRASONIC parameters are automatically determined and tracked during processing. In the CELOS control, a CELOS app shows the ULTRASONIC technology cycles and key process parameters such as frequency, amplitude and output, enabling maximum utilization of the ULTRASONIC and machine performance.”
For more information contact:
DMG MORI - Americas Headquarters
2400 Huntington Blvd.
Hoffman Estates, IL 60192
847-593-5400
Service Hotline: 855-DMG-MORI (364-6674)
www.us.dmgmori.com
< back