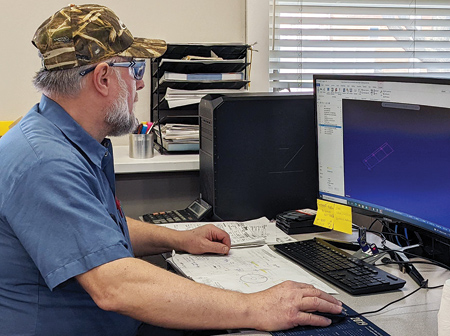
An Avers manufacturing engineer/CNC programmer programs a part in Mastercam.
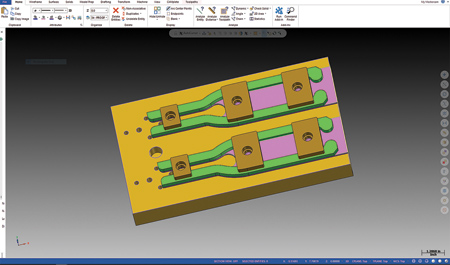
Mastercam screenshot of a custom fixture for a rack. The fixture was machined with one end mill.
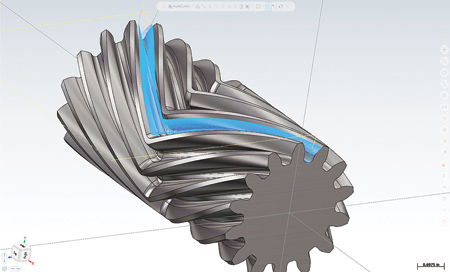
Mastercam screenshot of a complex Avers gear with herringbone teeth.
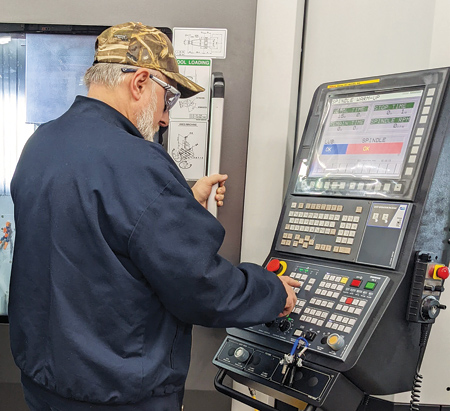
An Avers manufacturing engineer/CNC programmer prepares to machine a part on a Doosan DVF-5000.
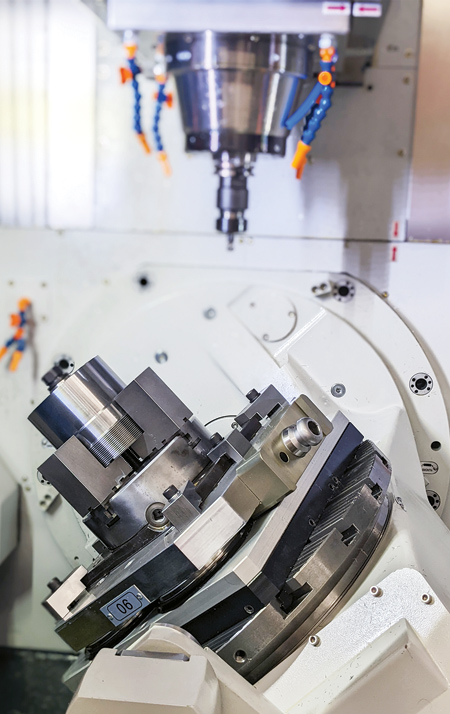
Avers uses Mastercam CAD/CAM software for multiaxis machining of complex gears and other parts.
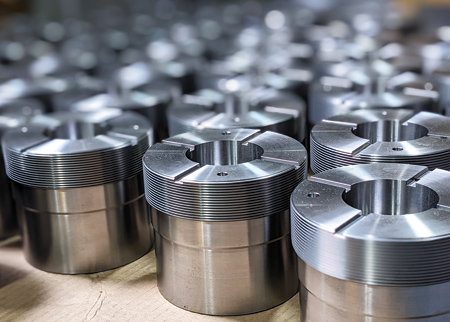
Blanks in line for 5-axis milling process.
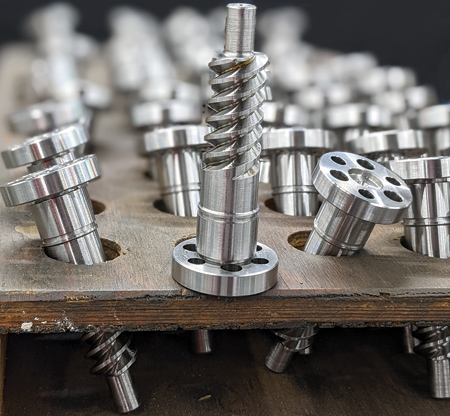
Hardened and ground parts produced by Avers.
When Avers Machine and Gear (Schiller Park, IL) expanded its machine shop through acquisition, it needed to find a way to bridge the gap to achieve future business goals. Team members evaluated what was driving value at each facility and implemented best practices, leveraging their systems to provide a successful integration.
Started in 1989, Avers is home to a 35,000-sq.-ft. facility. The company recently finished a building add-on and air conditioned its entire shop and offices with environmentally friendly units. President Chris Wellman and his partners decided to grow the operation and searched for two years before finding Innovative Rack and Gear (Wood Dale, IL), which consisted of a 20,000-sq.-ft. facility. Avers creates machine parts and gears, whereas Innovative Rack primarily manufactures racks. There is no customer overlap.
Together, two facilities and a combined 60 employees provide gear manufacturing, rack manufacturing and CNC machining services, offering Innovative Rack customers the opportunity to buy new parts beyond the racks they traditionally purchased. To optimize their strengths, Avers and Innovative Rack and Gear employees-including 45 machinists, 14 of whom are programmers-used their expertise to integrate their solid modeling, CAD/CAM and ERP systems.
"Everybody lives and dies by these systems," said Wellman. "We fully use them and take advantage of most of their capabilities, and we are training people every day on them. Once everybody is up to speed in their area of expertise, it is a great benefit to our organization."
More and more of Avers programmers are becoming proficient in using Mastercam CAD/CAM software to increase their own milling efficiencies, so they shared their knowledge to maximize profitability of the rack products.
"Innovative Rack was heavy into milling, which was one of our strengths. All of their products got milled at some point, but the company was not as strong in Mastercam," Wellman said. Before the acquisition, Innovative Rack had one seat of the software.
The new owners analyzed each product and discovered that one rack was losing money in manufacturing costs. According to Wellman, he questioned the impact of not continuing to manufacture this particular part. "That was really not the intent-to purchase this company and then get rid of work," he said. "The intent was to grow the business."
Wellman met with the engineers and programmers to assess the rack's current production methods. The team found that the rack was being held in a simple plate fixture. The cycle time of the machine was roughly two minutes before it would be manually flipped by an operator, repeating two times. Including the time required for part changes, the complete operation had more downtime than uptime.
To make the rack cost effective, the team needed some sort of fixture to prevent the machine from stopping so many times. If the part was clamped to an island with the ends overhanging, it would allow the part to be suspended and machined on the top and bottom sides, without having to be flipped. The team got to work designing a solution in SOLIDWORKS (Dassault Systèmes) that could hold eight workpieces at once.
The solid model of the fixture was then imported into Mastercam. It was tweaked and programmed using the 2D Dynamic Contour toolpath, which ensured the proper chip load. The whole fixture was efficiently machined on one end mill, with one tool completing the majority of the work.
"Once completed, the program was somewhere between 800 to 1,000 lines of code," Wellman said. "We could not manually do that. You would have to use a CAM program to do that."
Since the number of tools was minimized, machining the fixture on one end mill saved on programming time and tool cost.
After the fixture was complete, the set-up time for the rack was successfully reduced to a single process, letting the machine run more effectively. The two new fixtures were loaded into a 3-axis Okuma Genos M560 machining center with high-pressure coolant. The output changed substantially, increasing from 12 parts per hour to 45 parts per hour.
"You can be the best programmer in the world, but if you do not have the right fixturing, you are not going to be able to get the right results," said Wellman.
The integration of CAD and CAM software allowed operations to be streamlined throughout the Avers and Innovative Rack facilities. This provided the company with common designing and programming tools, regardless of the equipment. Within five minutes, programmers can pull up the original file for a part manufactured on one machine, run it through a post and create a new program for a different machine. This new program can be conveniently downloaded to the intended equipment through the intranet.
Although it has some planning visibility, Avers receives new jobs frequently and has to adapt its schedule daily.
"If you have one machine that can only do certain jobs and then all your customers order all those jobs at once, you cannot tell your customer, `Sorry I am not going to be able to deliver it to you for 20 weeks because we have too much work,'" Wellman said.
The manufacturer's standardization of programming allowed workflow scheduling to be distributed more efficiently, creating a steadier workload of part orders for each department. Whether a part was initially run on the facility's Doosan or Okuma machines, programmers now have the ability to change equipment as needed based on customer demand.
"Mastercam gives us tremendous flexibility to run repeat jobs in a multitude of work centers," Wellman explained. "I think the key to any job shop is to be flexible."
After they took ownership, the team members knew they had to immediately integrate the planning system. From the first day, they started taking Innovative Rack orders on the M1 ERP system (ECI Software Solutions). They began training employees on the system and within two months everyone knew how to process new jobs.
Looking to the future, Avers increased its manufacturing capabilities by upgrading to 5-axis machining. Building on their 3D milling experience, programmers initially started using positional strategies, repositioning the part on the screen in the software so they could mill each side. Once they became savvy with that method, they learned how to perform actual 5-axis programming where the axes are working in conjunction. Now, the programmers can create parts with complicated geometries.
Wellman remembered a complex gear with a staggered tooth herringbone that team members were able to raw machine for a customer. The part was 13.5" by 18" and weighed 385 lbs. It had 180 teeth per part, with tight tolerances of one-thousandth of an inch or less. Avers programmers used Mastercam Swarf and Morph toolpaths to mill the teeth, as well as Project Curve to create a 5-axis chamfer. It required four axes moving at the same time in one positional job, running at high speeds of 120 IPM. Even though the gear was intricate, the software allowed the programmers to use standard tools. Each part took 9.5 hours to complete.
As Avers' capabilities expanded, the company used the Maintenance Program through its Mastercam Reseller, Shopware Inc. (Elgin, IL) to help keep up with the latest technology. Employees have access to the most up-to-date software versions, as well as new features. When Avers first implemented 5-axis machining, a Shopware representative came in to train the programmers and teach foundational skills, such as how to present the part properly to the tool and avoid interferences.
"We are doing a lot more complex programs, so having technical support all the time is critical," Wellman said.
Avers employees can call a Shopware helpline if any assistance is required. They indicate whether they have a CAD or CAM issue, and the relevant team member will call them back. For basic problems, Shopware responds within minutes. In the case of complex issues, Wellman said the support staff takes no longer than 24 hours to respond and help solve the problem.
Avers' management believes in the power of workforce development and exposing as many people as possible to the software to gain the most benefit.
"I think you always have to have different level programmers, and then team members need to teach each other, and as a result, the company gets that much stronger and that much more efficient. You cannot have a bottleneck with programming," said Wellman. "You have to have a lot of people do different things."
Employees can start learning the basics and becoming familiar with the screens from online Mastercam training courses. Then, they can graduate to on-the-job training. The software has a user-friendly interface and simple design, making it intuitive to use. Avers' entry-level programmers make simple changes, like updating the tools, while experienced programmers work on complex jobs, like 5-axis programming.
The Tool Library increases programming efficiency, taking advantage of similar parts and equipment that have already been optimized. When working with new parts, operators can transfer the toolpath from a similar program. Additionally, when working with new equipment, operators can transfer the toolpath from a similar machine. Avers incorporates revision control to ensure the best feeds and speeds are being utilized, which is significant for parts that may not have been run in five or 10 years.
Like with any transition, there were bumps along the way, but Avers was able to overcome these challenges and integrate its acquisition successfully.
"Systems are extremely important," concluded Wellman. "Whatever system you choose, everybody needs to be fully trained and integrated, and everybody needs to use it."
For more information contact:
Avers Machine and Gear
3999 25th Ave.
Schiller Park, IL 60476
847-447-3430
sales@aversonmachine.com
www.aversonmachine.com
Innovative Rack and Gear
365 Balm Court
Wood Dale, IL 60191
630-766-2652
CNC Software, Inc.
671 Old Post Road
Tolland, CT 06084
800-228-2877
info@mastercam.com
www.mastercam.com