
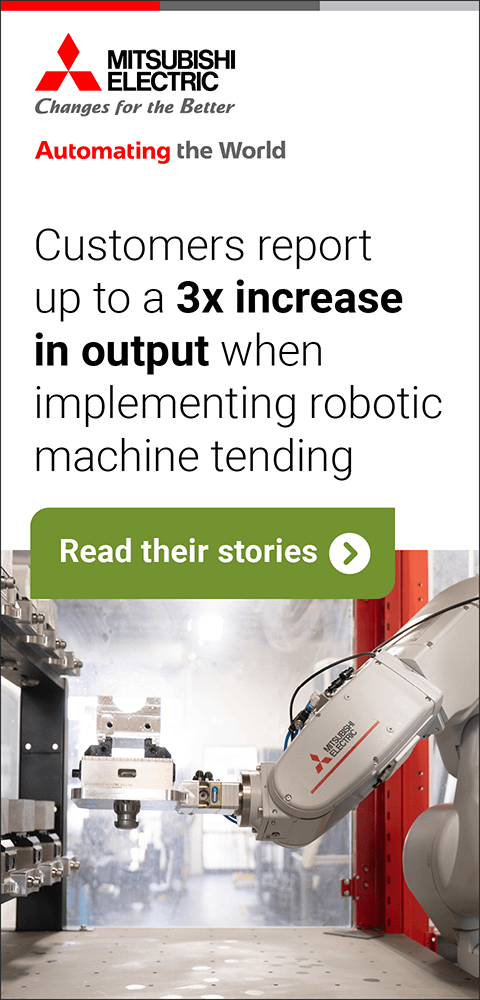
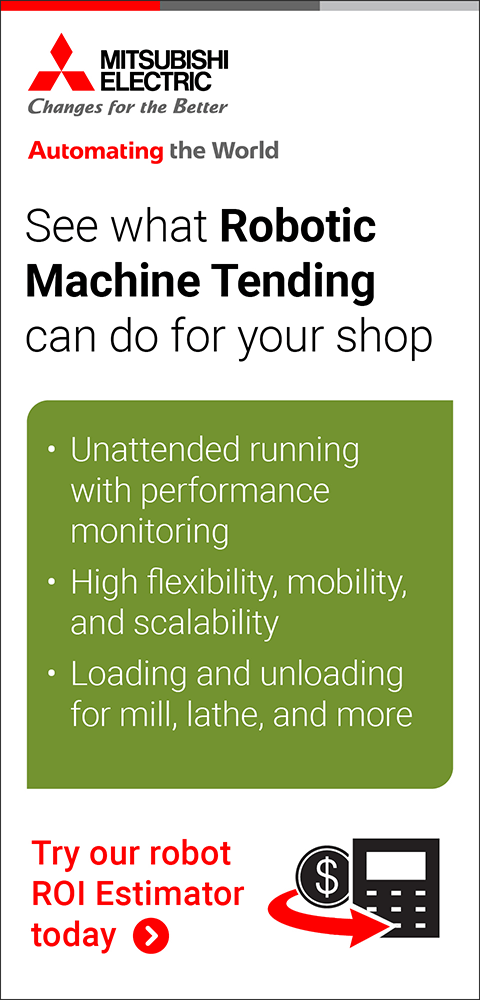
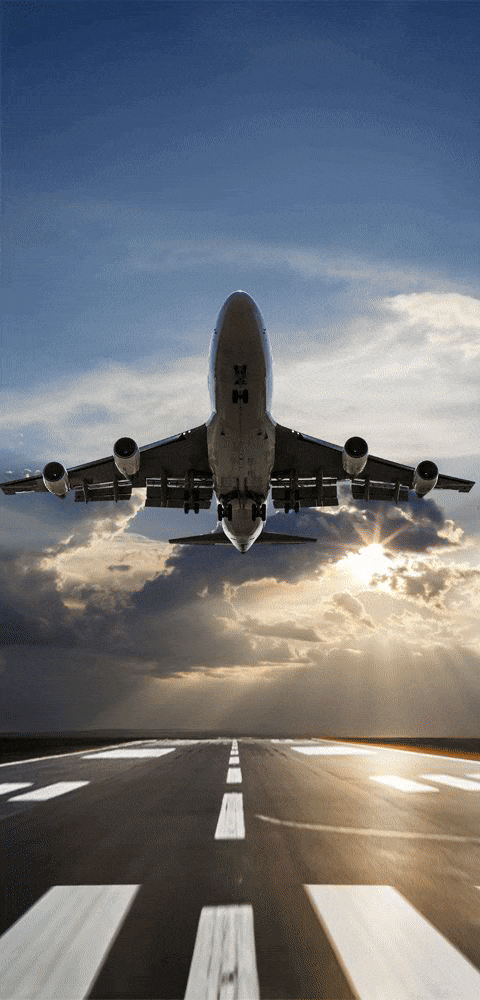
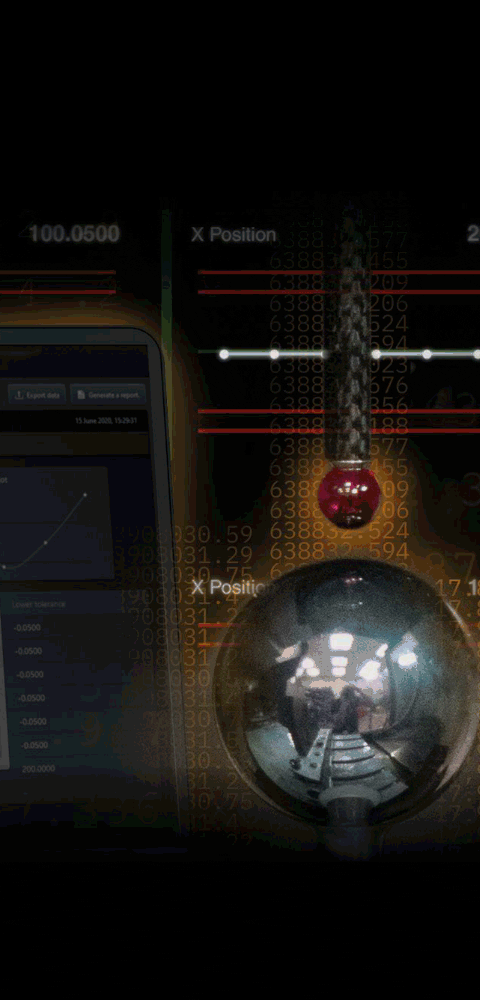
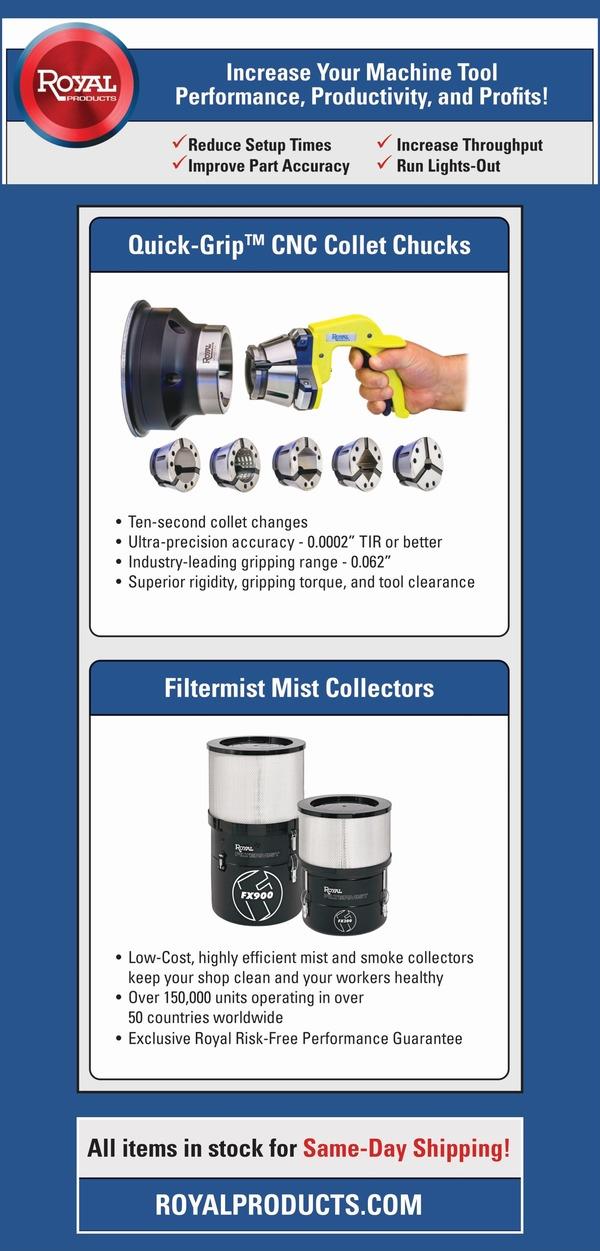
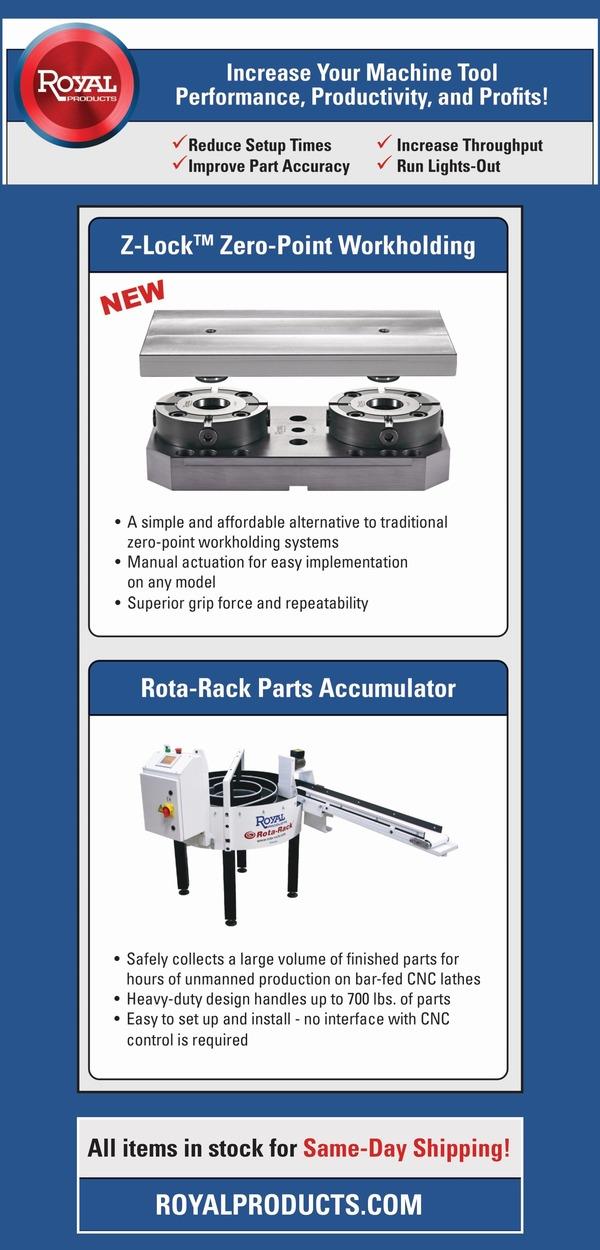
Renishaw's New RenAM 500 Ultra Cuts Additive Manufacturing Build Times; System on Exhibit at Upcoming SHOT Show 2024 in Vegas
January 29, 2024Renishaw has expanded its RenAM 500 series with the launch of the RenAM 500 Ultra AM system, cutting build times by up to 50 percent—without compromising on quality and giving metal additive manufacturing (AM) users the tools to produce parts faster.
The new system was launched at Formnext 2023 in Germany in November 2023. In January 2024, the new Ultra AM line, along with the Equator gauging system, are featured in Renishaw’s exhibit at SHOT Show 2024 in Las Vegas, NV, January 23-26. Visitors to the Renishaw booth will see finished additive parts and learn how the new system delivers significant productivity benefits at a highly competitive price point.
"The RenAM 500 Ultra system includes all the existing benefits of the RenAM 500 series, including industry-leading optical, chamber and gas-flow design, and it adds new productivity-boosting TEMPUS technology and advanced process monitoring software," a Renishaw spokesperson said.
TEMPUS technology incorporates new scanning algorithms that allow the laser to fire while the recoater is moving, saving up to nine seconds per build layer. The RenAM 500 Ultra’s advanced process monitoring software also delivers detailed insights into the build, equipping users with data and providing in-process visibility. The RenAM 500 Ultra metal AM system is the latest model in the RenAM 500 family, which also includes the Flex system, optimized for R&D work, and the flagship closed-loop powder recirculation model for series production. The entire RenAM 500 family is available with one (500S) or four (500Q) high powered lasers, each able to access the whole powder bed simultaneously.
Also on display at SHOT Show 2024 is the Equator gauging system, the proven integral component in supporting manufacturers’ drive to develop their own smarter processes and embrace factory automation. The Equator system, capable of operating at a temperature range of 5 – 50°C and up to 80 percent humidity, is optimized for part loading via a robot or shuttle system, the company reported.
"Configured for easy communication between the system and a variety of automated work cell equipment, integration into an automated cell is simplified. The result is significantly reduced cycle times, improved productivity and increased throughput," the spokesperson added. "Introducing flexible gauging close to the point of manufacture also allows the validation of discrete machining operations, enabling automated process control and tool offset management. This leads to increased confidence in final part quality."
Equator gauging systems have been designed to cope with a wide range of parts and design changes, and the system’s automatic stylus changing rack enables the inspection of multiple parts in quick succession. It is a proven example of how manufacturers are future-proofing their business activities with an efficient and cost-effective solution to part gauging.
For more information on Renishaw metal additive manufacturing, and/or the Equator gauging system, visit www.renishaw.com.
Shot Show 2024, Booth #51610
< back